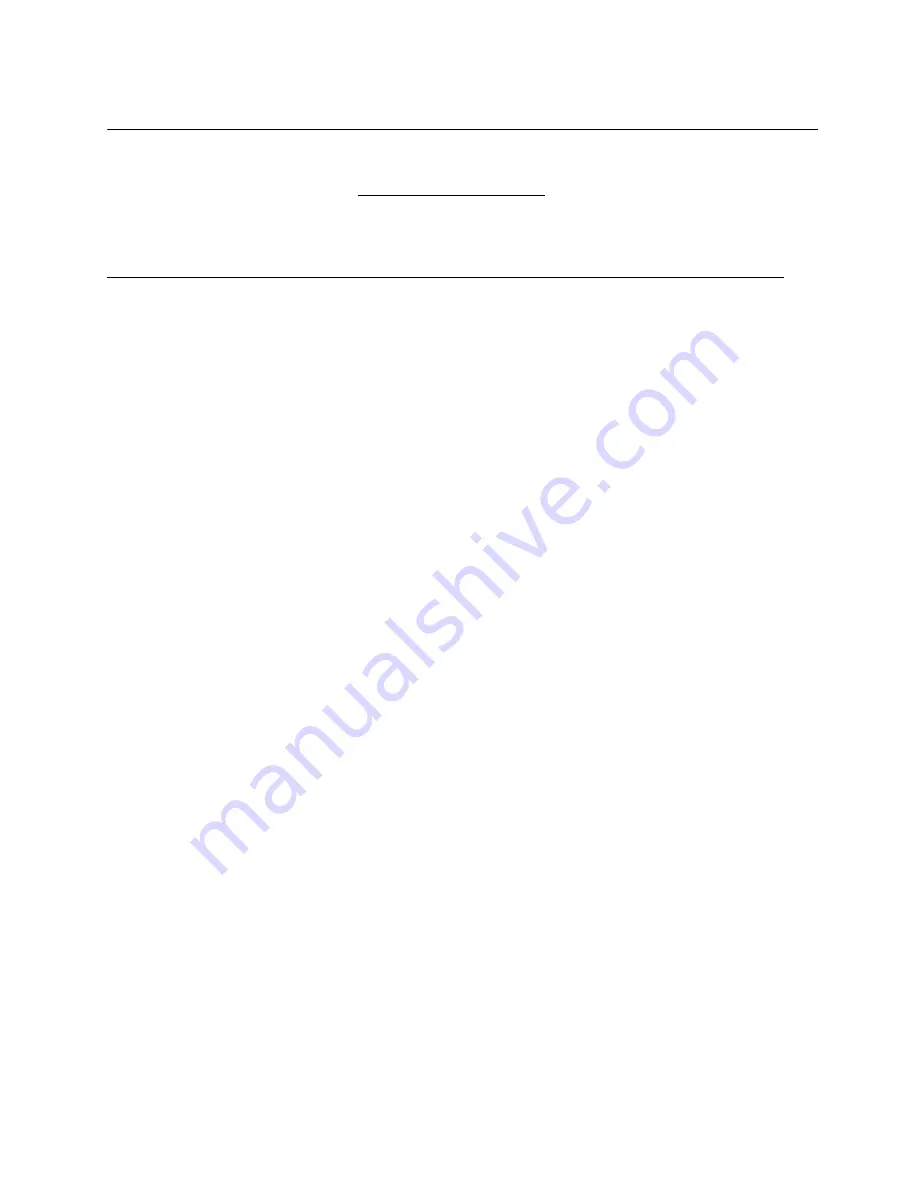
PAN SELECTION & TIME SCHEDULES
SECTION 3: MODELS: GC-2 & GC-3
COOKING CHART - cont'd
ITEM
PAN DEPTH
(FULL SIZE)
TIMER SETTING
IN MINUTES
WEIGHT LBS
PER PAN
NUMBER
OF PANS
Carrots (sliced)
2-1/2"
18 - 21
9
1 - 3
Perforated
21 - 25
4-6
Corn
2-1/2"
9-10
5
1 - 3
Perforated
11 - 13
4-6
Chicken
2-1/2"
18 - 25
8
1 - 3
Blanched-Cut
Perforated
25 - 30
4-6
Eggs - out of
2-1/2"
6-7
4 dozen
1 - 3
Shell
Solid
7-8
4-6
Eggs - in
2-1/2"
2-3
3 dozen
1 - 3
Shell
Perforated
4-6
4-6
Fish-Fillets
2-1/2"
8-12
3
1 - 3
Perforated
10 - 15
4-6
Meatloaf
2-1/2"
35 - 40
15
1 - 3
Solid for Broth
40 - 45
4-6
Peas
2-1/2"
6-7
5
1 - 3
Perforated
8-9
4-6
Potatoes cut
2-1/2"
20 - 25
10
1 - 3
Regular
Perforated
25 - 30
4-6
Potatoes cut
2-1/2"
15 - 18
10
1 - 3
French Fry
Perforated
18 - 20
4-6
Spinach
4"
3-5
3
1 - 2
cut, cleaned
Perforated
4-6
3-4
Rice
4"
22 - 24
4
1 - 2
1 Gallon Water
Solid
-,25-27
3-4
Spaghetti
4"
20 - 22
3
1 - 2
1-3/4 Gal. Water
Solid
23 - 26
3-3
Turkey
2-1/2"
50 - 60
10 - 12
1 - 3
Perforated
60 - 75
4-6
7
Summary of Contents for CQ-325S
Page 10: ...PERIODIC MAINTENANCE SECTION 4 MODELS GC 2 GC 3 FIG 2 SIDE VIEW 8 ...
Page 14: ...PERIODIC MAINTENANCE SECTION 4 MODELS 6C 2 GC 3 FIG 3 12 EXHAUST TO DRAIN STEAM IN ...
Page 25: ...PARTS LIST SECTION 7 COMPARTMENT DOOR ASSEMBLY FIG 4 23 ...
Page 28: ...PARTS LIST SECTION 7 COOKER ASSEMBLY FIG 5 25 ...
Page 30: ...PARTS LIST SECTION 7 COOKER CONTROLS FIG 6 27 ...
Page 32: ...PARTS LIST MODELS GC 2 GC 3 SECTION 7 CABINET FIG 7 29 ...
Page 34: ...PARTS LIST SECTION 7 MODELS GC 2 GC 3 GENERATOR CONTROL BOX ASSEMBLY FIG 8 31 OVERRIDE ...
Page 36: ...PARTS LIST SECTION 7 MODELS GC 2 GC 3 GDA 2 GHD 2 GENERATOR ASSEMBLY FIG 9 33 ...
Page 40: ...WIRING DIAGRAM 37 SECTION 8 MODELS GC 2 GC 3 ...
Page 41: ...WIRING DIAGRAM SECTION 8 MODEL GDA 2 38 ...
Page 42: ...WIRING DIAGRAM 39 SECTION 8 MODEL GHD 2 ...
Page 43: ...WIRING DIAGRAM MODELS EDA 2 SCDA 2 GDA 2 DDA 2 SECTION 9 SUPPLEMENT ...