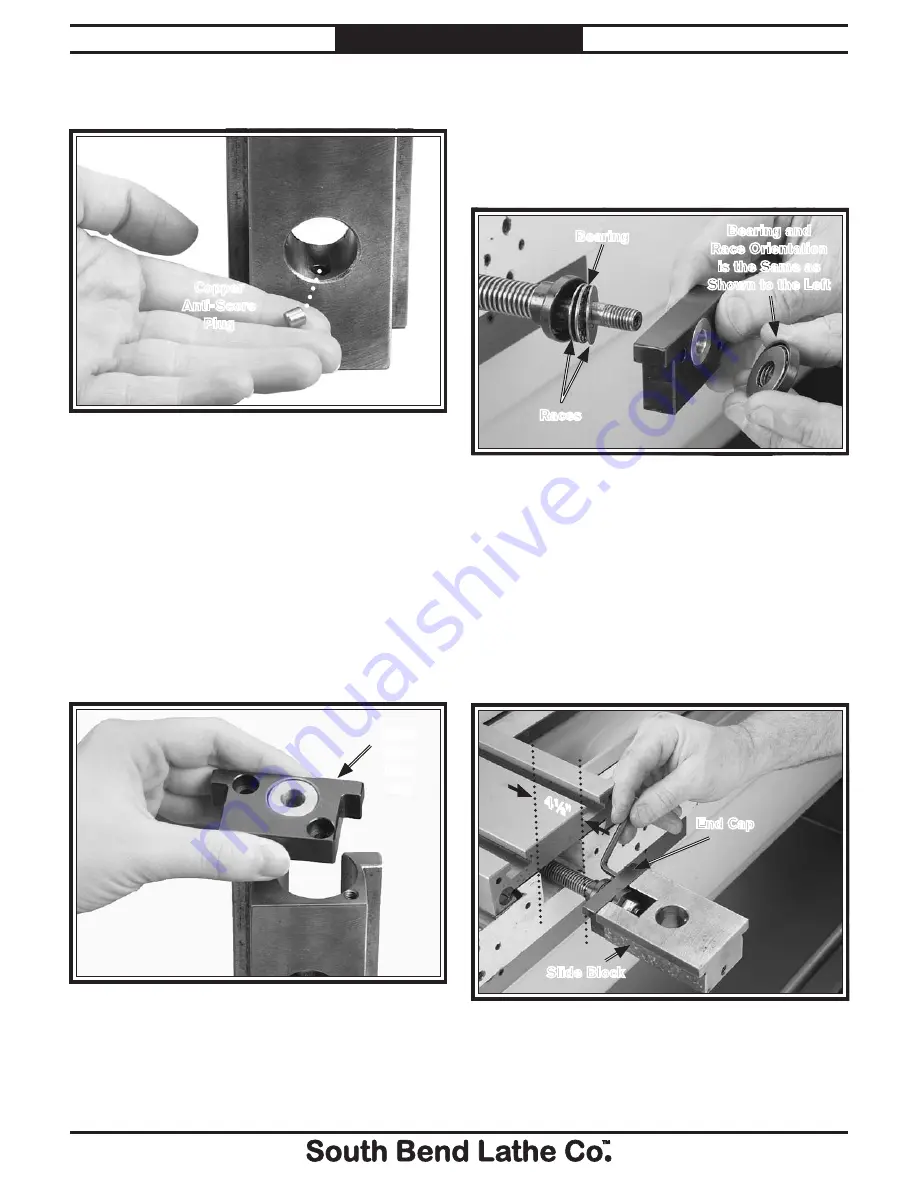
9. Lift out the slide block without losing the
copper anti-score plug (Figure 8).
12. Clean the bearings and races with mineral
spirits, then dry and repack them with white
lithium grease.
13. Install the bearings and races onto the
leadscrew in the order shown in Figure 10.
Figure 8. Slide block copper anti-score plug.
10. Apply a dab of multi-purpose grease to the
copper plug to prevent it from falling out
when handling the slide block.
Note
: This copper plug prevents the set screw
from scoring the main pivot pin when the
taper attachment is being used.
11. Using a 5mm hex wrench, remove the two
cap screws that retain the slide block, and
remove the slide block end-cap as shown in
Figure 9.
Copper
Anti-Score
Plug
Figure 9. Slide block end-cap removal.
Slide
Block
End
Cap
14. Using a 17mm wrench, thread the lock nut
onto the lead screw until the bearings are
slightly preloaded, and the slide-block end
cap has zero end play.
15. Using a 5mm hex wrench, secure the
slide block onto the endcap with the two
previously removed cap screws, as shown in
Figure 11.
Figure 10. Slide block end-cap installation,
(bearings shown without grease for clarity).
Bearing
Races
Bearing and
Race Orientation
is the Same as
Shown to the Left
16. Pull or push the cross slide assembly so the
center of the pivot pin bore is 4
1
⁄
2
" from the
carriage face, as shown in Figure 11.
Figure 11. Slide block installation.
End Cap
4
1
⁄
2
"
Slide Block
-6-
For Product Mfg. Since 1/10
Model SB1269
P R E P A R A T I O N