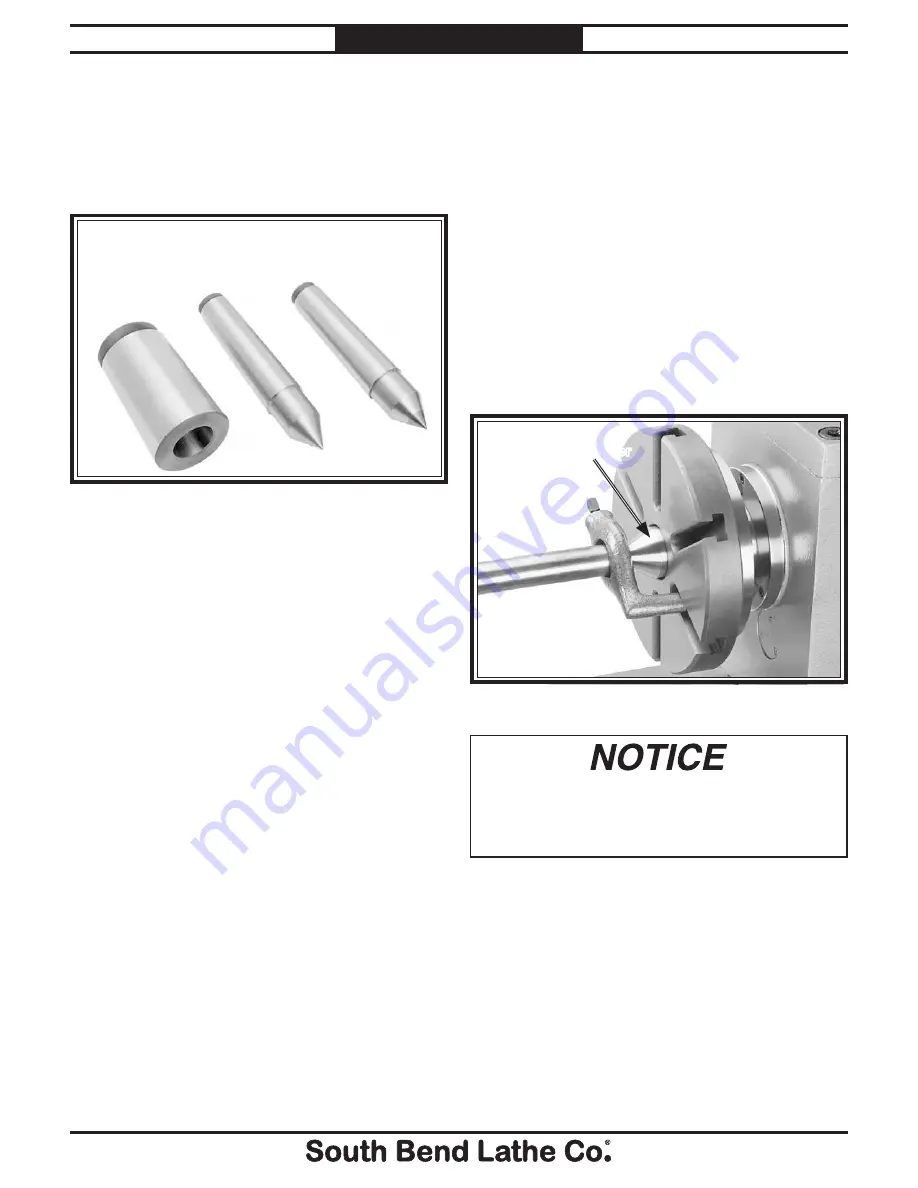
For Machines Mfg. Since 7/09
EVS Toolroom Lathes
-37-
O P E R A T I O N
Mounting Dead Center in Spindle
1.
DISCONNECT LATHE FROM POWER!
2.
Thoroughly clean and dry the tapered
mating surfaces of the spindle bore, tapered
sleeve, and the center, making sure that no
lint or oil remains on the tapers.
3.
Insert the center into the sleeve, then insert
the sleeve into the spindle bore through the
chuck or faceplate.
Figure 66
shows an example of the dead
center installed in the spindle, using a
lathe dog and faceplate for turning between
centers.
Centers
Figure 65
shows the dead centers included with
the lathe. In addition, an MT#6–MT#4 tapered
spindle sleeve is included for mounting centers in
the spindle.
Dead Centers
The dead center achieves more accurate results
than a live center, but it requires low spindle
speeds and a small amount of oil to reduce
friction heat that may damage the workpiece.
Use the dead center in the spindle, because the
workpiece does not rotate on the tip and does not
generate friction.
Use the carbide-tipped dead center in the
tailstock where the workpiece will rotate against
it and generate friction. The carbide-tipped dead
center can better withstand the effects of friction;
however, the tip of the center must be lubricated
to avoid premature wear and maximize smooth
operation. Also, using low spindle speeds will
reduce the heat and wear from friction.
Figure 66. Example of using a dead center with a
faceplate and lathe dog.
Dead Center
To avoid premature wear of the dead center
or damage to the workpiece, use low spindle
speeds and keep the tip of the dead center
mounted in the tailstock well lubricated.
Live Centers
A live center has bearings that allow the center
tip and the workpiece to rotate together, and can
be installed in the spindle and the tailstock quill
for higher speeds.
Figure 65. Tapered sleeve and dead centers.
Tapered
Sleeve
Dead Center
Carbide Tipped
Dead Center
Summary of Contents for SB1013F
Page 120: ......