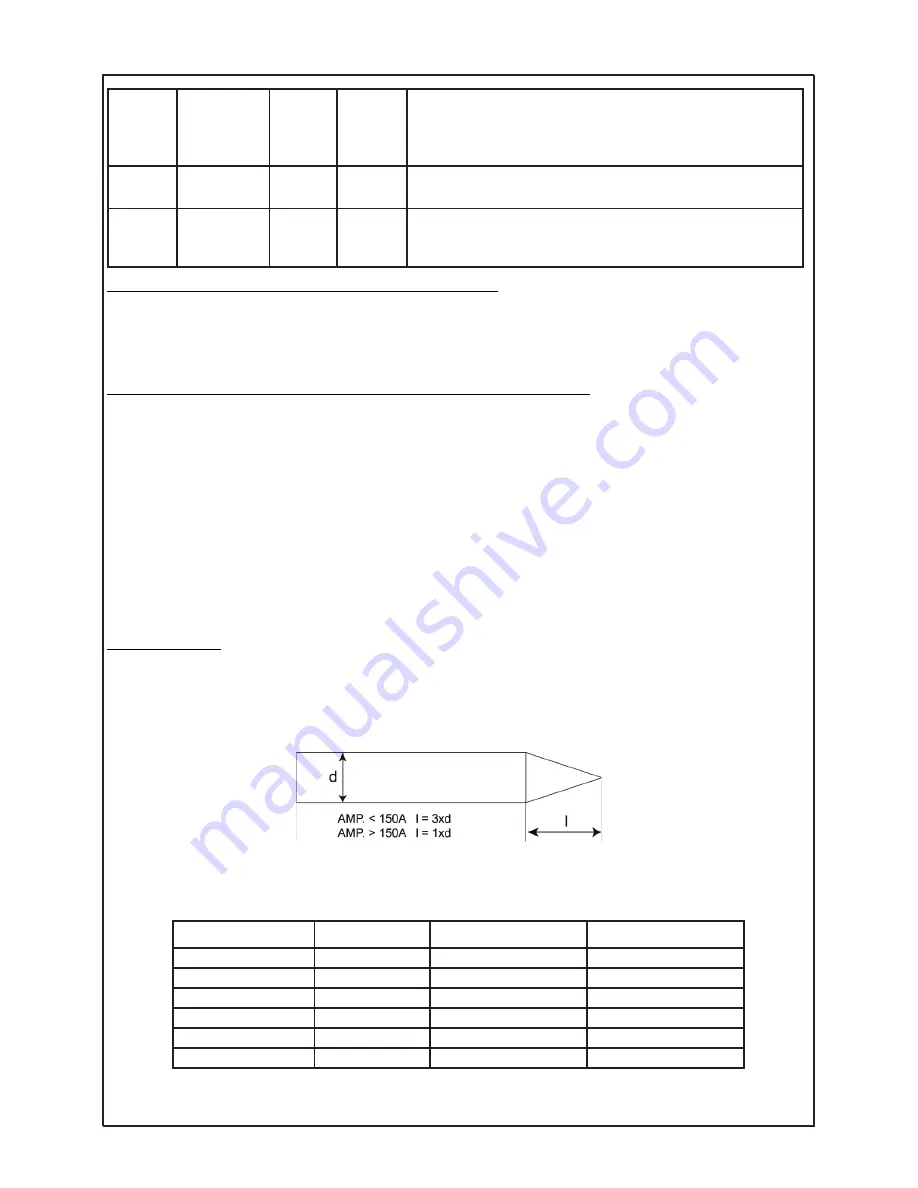
TIG MODE BY POINTS, FULL POwER POINT FEATURE - FPP
To use this feature, you must use an optional two button torch.
If you start the arc using the second button (in a TIG welding process), the FPP (Full Power Point feature) is applied.
The set power is supplied instantly without starting time lapses, ramps or stops. This feature is especially useful for a
quick initial point process.
TIG MODE wITH SECOND LEVEL OF AMPERAGE AND BI-LEVEL FEATURE
If you press the second button having started the process with the first, the machine produces a second level of am-
perage. For TIG processes without pulsed arc, the second amperage value will be the value set in parameter I2. For
pulsed arc TIG processes, either low or high-frequency, the second level is the percentage specified by the Bi-level fe-
ature in the advanced parameter P.34.
For TIG welding with 2T operation, if you press and hold down the secondary button during the down ramp, the wel-
ding current is set according to the second setting level. You can do I
NOM
again if you press and hold down the main
button again during the down ramp.
For TIG welding with 4T operation, start the process with the main button as usual. During welding, apply short pres-
ses using the second button to switch between the first or second setting level. Stop the weld in the normal way by pres-
sing the main button.
By using the adjustment potentiometer you can vary the setting of the rated current from the rated value set on the front
panel to the minimum machine operating value. This allows you to reduce or increase the welding current setting of all
parameters associated with the rated current with a single control.
TIG DC wELDING
Select the DC- polarity in TIG mode to weld different types of steel. We recommend using tungsten electrodes with tho-
rium (red), cerium (grey) or lanthanum (gold).
The electrode tip must be sharpened into a cone shape. In this way, the arc is more stable and more energy can be con-
centrated at the weld root. Depending on the amperage used, it is recommended to sharpen the electrode to a greater
or lesser extent.
For TIG DC, depending on the amperage used to weld, a specific electrode diameter, nozzle and gas flow rate is re-
commended. Follow the reference chart below as a guide.
I
STOP
Final
current
10%
100%
Determines the current value (as a percentage in relation to I
NOM
),
at which the arc finishes. This parameter reduces the possibility
of appearing pores or fissures at the end of the weld bead
T
STOP
Final current
Time
0,0 sec
10 sec
Determines the time during which the level defined by the I
STOP
parameter will be maintained.
T
POST GAS
Post gas
time
0,0 sec
10 sec
Time during which gas flows after welding. Necessary to protect
the electrode in TIG mode.
Amps range (A)
Electrode (mm)
Nozzle (mm)
Gas Flow (l/min)
10 - 60
1,0
6,5 / 8,0
5 - 6
60 - 120
1,6
6,5 / 8,0 / 9,5
6 - 7
120 - 170
2,0
8,0 / 9,5
7 - 8
170 - 220
2,4
9,5 / 11,0
8 - 9
220 - 350
3,2
11,0 / 12,5
9 - 10
300 - 420
4
16
10 - 12
SOLTER
SOLDADURA S.L.
AEROTIG AC/DC
39