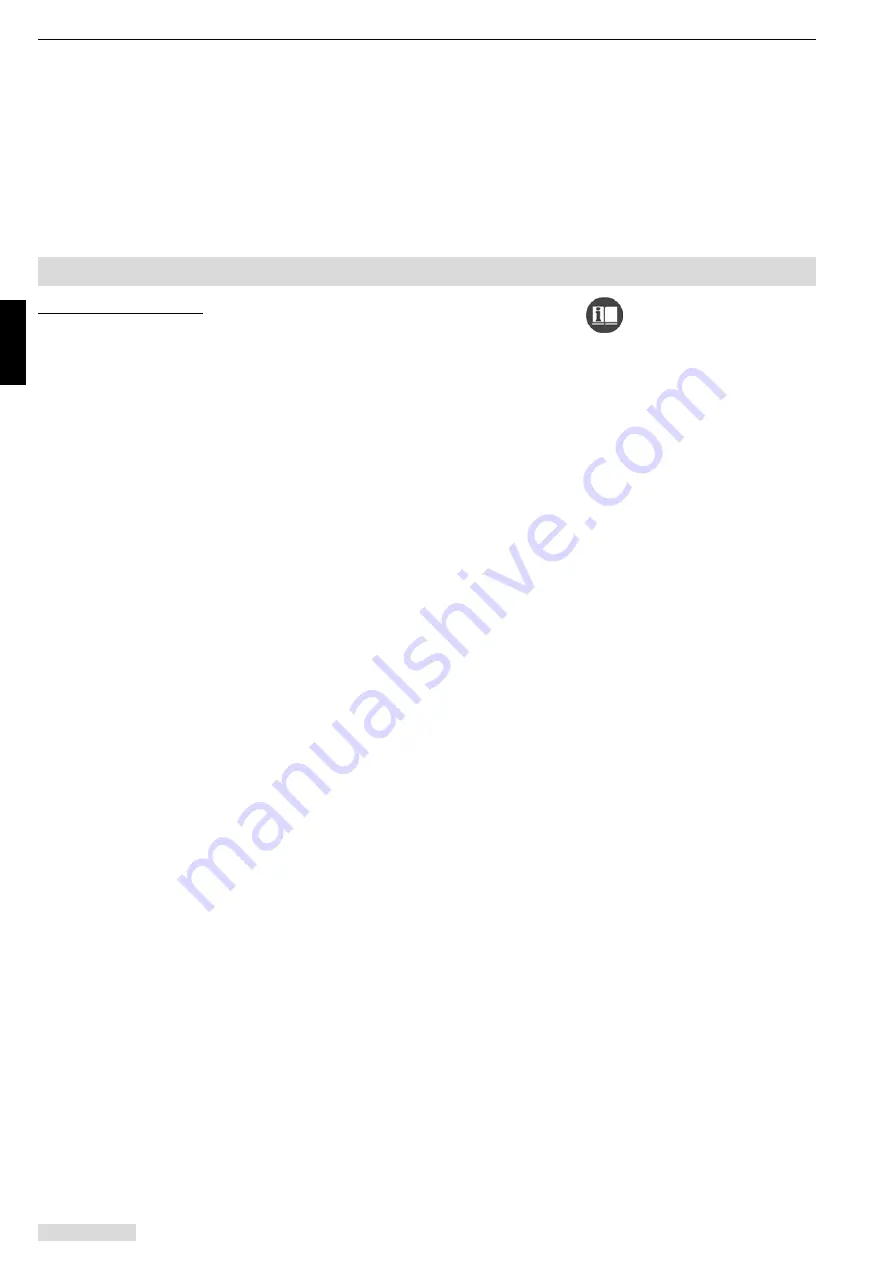
Operating and maintenance notes
ENGLISH
38
Furthermore, a specialist workshop authorised by us must be charged, among others, with the following
service in the scope of the annual customer service:
•
Complete inspection of the entire power tool
•
Professional motor cleaning (fuel tank, cylinder ribs, …)
•
Inspection and, if applicable, replacement of the wear parts, in particular annual replacement of the fuel
filter
•
Best settings of the carburettor
Possible malfunctions:
è
•
Engine does not start up
– Stop dial
Ø
Turn the stop dial to the operating position "1". ...............
è
Chap. 6.1, page 24
– Spark plug
Ø
Clean or replace ...............................................................
è
Chap. 8.5, page 34
– Old fuel
Ø
Empty and clean tank, fuel up with fresh fuel ..................
è
Chap. 5.5, page 18
•
Cutting disc is not accelerated properly
– Foreign body inside the protective cowl
Ø
Clean protective cowl .......................................................
è
Chap. 8.1, page 30
– Ribbed belt tension too low
Ø
Correctly set ribbed belt tension ......................................
è
Chap. 5.6, page 20
•
Cutting disc is driven in idle operation
– Idle stop screw "T"
Ø
Correctly adjust idle stop screw "T" .................................
è
Chap. 8.3, page 32
– Coupling defective
Ø
Service workshop
•
Bad engine output
– Air filter clogged
Ø
Clean air filter thoroughly .................................................
è
Chap. 8.4, page 33
– Carburettor settings (L/H-settings)
Ø
Service workshop
•
Insufficient or no water supply in wet cutting
– Valve lever of the water supply line not opened
Ø
Open valve lever ..............................................................
è
Chap. 5.7, page 20
– Connection of the water supply closed
Ø
Open water supply
– Water supply pressure tank empty or pressure-relieved
Ø
Top up water or recover pressure supply
– Screen filter insert contaminated
Ø
Thoroughly clean screen filter insert ................................
è
Chap. 8.2, page 31
•
Changed noise emission and motor does not reach high speeds
(only for models 881-12 and 881-14)
– Not enough engine oil in the oil tank
Ø
Fuel up engine oil .............................................................
è
Chap. 5.5, page 18
8.9 Self-aid advice