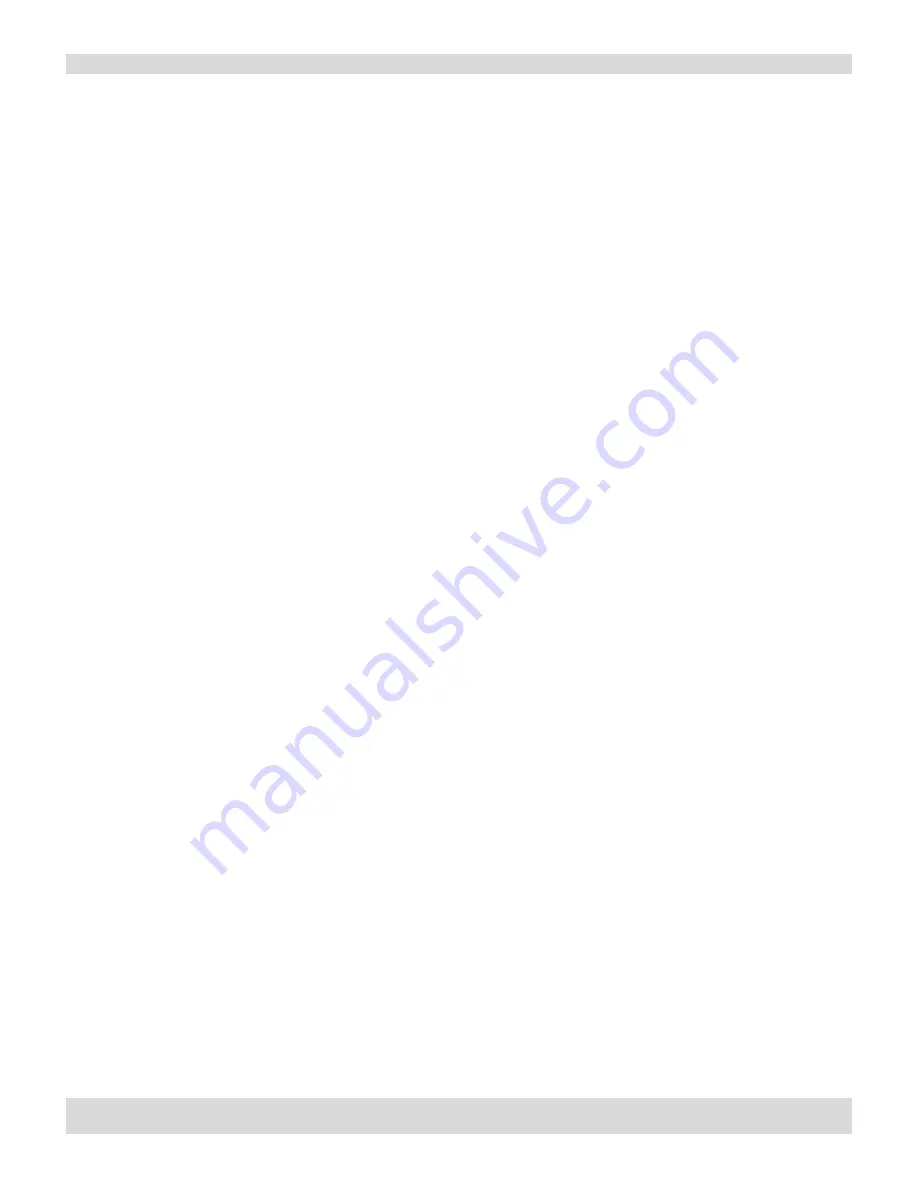
T
HERMO
C
UBE
PAO
C
HILLER
P
ART
#
52-400-2G-1-PAO
S
OLID
S
TATE
C
OOLING
S
YSTEMS
,
167
M
YERS
C
ORNERS
R
OAD
,
W
APPINGERS
F
ALLS
,
NY
12590
14
T
ELEPHONE
:
(845)
296-1300
F
AX
:
(845)
296-1303
WEB
V
ERSION
M9
The following keystrokes initiate the auto-tune function:
1)
Press and hold the Enter key until the Status Menu changes to the
Temperature Input menu.
2)
Press and hold the Enter key again until the Temperature Input menu
changes to the Parameter Input menu.
3)
Press the Enter key three times. The display should read
AUTOTUNE off.
4)
Press the Up key to change off to on.
5)
Press and hold the Enter key until the parameter input menu
returns to the Status Display.
6)
Press the Start key once. The left most display character will show
the letter A until the auto tune is complete. The ThermoCube will
then begin controlling at the set point temperature.
5.5
M
ANUAL
T
UNING
For users well versed in PID theory, Solid State Cooling Systems
recommends the closed-loop “Ziegler Nichols” method for manually
tuning the controller. The method consists of three steps:
1)
Turn off both the integral and derivative terms for heating and
cooling by setting I1, I2, D1, and D2 to zero.
2)
Set proportional band to 50 °C. Begin controlling the process at the
desired set-point temperature. Look for a small-sustained oscillation
in the coolant temperature. Observe the status menu operating mode
character and note if system is heating (+) or cooling (-). If no
oscillation occurs, lower the proportional band in 50% increments
until a small oscillation occurs. Write down this proportional band
setting (P)
3)
Measure the “Natural Frequency” (t) of the system in seconds. This
is the time required for the temperature oscillation to cycle from one
maximum temperature to the next maximum temperature.
Now set the controller input parameters as follows:
P1 HEAT = 2*P if system was heating in step 2.
P1 HEAT = 4*P if system was cooling in step 2.
I1 HEAT = 1.2*t
D1 HEAT = t/8
P2 COOL = P if system was heating in step 2.
P2 COOL = 2*P if system was cooling in step 2.
I2 COOL = 1.2*t
D2 COOL = t/8