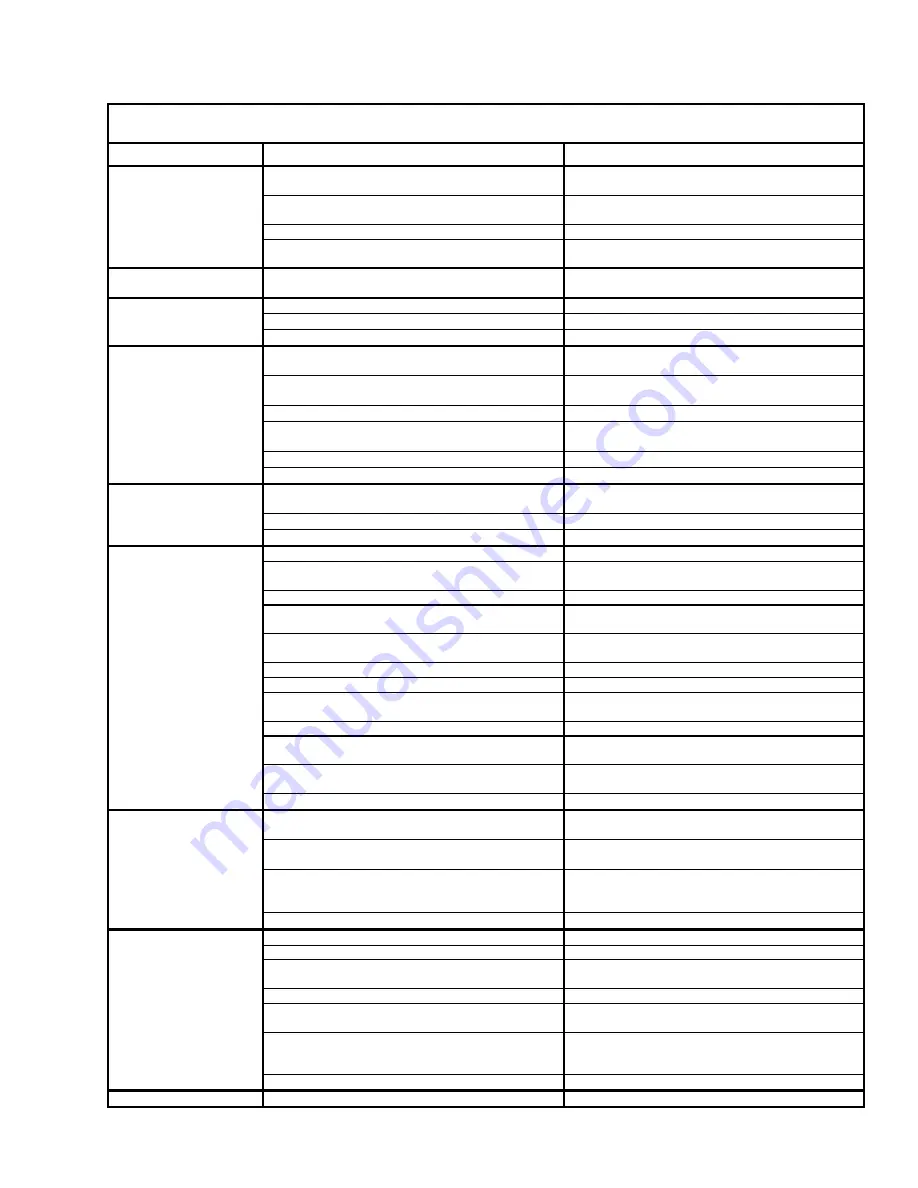
17
TROUBLESHOOTING
•
Check for symptoms and possible causes in the order presented from the top of this chart to the bottom.
•
The symptoms and possible causes are in a logical progressive order as in a flow chart.
SYMPTOM
POSSIBLE CAUSE
CORRECTIVE ACTION
1.
Heaters not isolated during high pressure leak
testing.
1.
Replace combination gas valves on each
heater.
2.
All gas lines not completely bled of air.
2.
Disconnect flex hose at each heater until gas is
present. Connect flex hose and leak test.
3.
Gas supply regulator reversed.
3.
Remove and install properly.
New installation.
4.
Electrical supply line voltage & neutral polarity
reversed.
4.
Correct electrical supply polarity.
Gas odor.
1.
Gas pipe joints loose.
1.
Check joints with soap solution, tighten as
needed.
1.
Power supply fuse defective.
1.
Replace fuse.
2.
115 VAC not reaching heater.
2.
Check thermostat and wiring and fix.
Blower / PL-1 light does
not come on when
system energized.
3.
Blower defective.
3.
Replace blower.
1.
Inlet or exhaust piping not the proper size and
length. (Refer to manual.)
1.
Replace piping as required.
2.
Inlet or exhaust termination fittings not to factory
specifications.
2.
Replace fittings as required.
3.
Inlet or exhaust blocked.
3.
Clear blockage.
4.
Airflow tubing or snubber orifice blocked in one
or both tubes.
4.
Clear blockage.
5.
Blower wheel dirty or damaged.
5.
Clean or repair wheel.
Pressure switch does
not close / PL-2 light
does not come on.
6.
Airflow pressure switch defective.
6.
Replace airflow pressure switch.
1.
115 VAC not reaching the Ignition Detection
Control (IDC) due to loose wire or connector.
1.
Repair loose wire or connector.
2.
High-voltage wire loose or damaged.
2.
Secure high-voltage wire or replace ignitor.
Ignitor does not spark /
PL-3 light does not
come on.
3.
Ignition Detection Control (IDC) defective.
3.
Replace IDC box.
1.
Gas supply not turned on.
1.
Open all manual gas supply valves.
2.
Ignitor not sparking at the tips.
2.
Measure spark gap and adjust gap as
necessary to 5/32" [0.156" (3.96mm)].
3.
Ignitor not sparking at correct gap.
3.
Replace ignitor.
4.
Gas inlet pressure not correct. (See serial
plate). Gas inlet piping not sized correctly.
4.
Replace inlet gas piping with correct size pipe.
5.
Gas inlet pressure not correct. (See serial
plate). Gas supply regulator not set correctly.
5.
Adjust gas supply regulator to set inlet pressure
to proper level. (See serial plate).
6.
Gas supply regulator sticking.
6.
Replace gas supply regulator.
7.
Combination gas valve not in the ON position.
7.
Turn combination gas valve to the ON position.
8.
Ignition Detection Control (IDC) not sending
115VAC to combination gas valve.
8.
Replace IDC box.
9.
Combination gas valve defective.
9.
Replace combination gas valve.
10. Combination gas valve outlet (manifold)
pressure not correct. (See serial plate).
10. Adjust combination gas valve regulator to set
inlet (manifold) pressure to proper level.
11. Main or sub gas orifice blocked by spider web,
etc.
11. Clear blockage.
Burner does not ignite.
(There are three trials-
for-ignition before the
IDC goes into lockout).
12. Gas orifice(s) or air orifice size not correct.
12. Install correct size gas orifice(s) or air orifice.
1.
Power supply not grounded to a true earth
ground.
1.
Install a true earth ground to the power supply.
2.
Flame sensor wire loose or damaged.
2.
Secure flame sensor wire or replace wire
harness to IDC box.
3.
Flame signal not at least -17 VDC.
3.
Check gas inlet and manifold pressures
compared to the possible causes in the previous
symptom where the burner does not ignite.
Spark does not stop
when the burner ignites.
4.
Ignition Detection Control (IDC) is defective.
4.
Replace IDC box.
1.
Flame sensor wire is loose or damaged.
1.
Replace wire harness to IDC box.
2.
Ground connection to IDC loose.
2.
Tighten ground connection to IDC.
3.
Electrical supply line voltage & neutral polarity
reversed.
3.
Correct electrical supply polarity.
4.
Inlet or exhaust partially blocked.
4.
Clear blockage.
5.
Airflow pressure switch erratic or defective.
5.
Consult factory or replace airflow pressure
switch.
6.
Flame signal not at least -17 VDC.
6.
Check gas inlet and manifold pressures
compared to the possible causes in the previous
symptom where the burner does not ignite.
Burner does not stay lit
until the thermostat is
satisfied.
7.
Ignition Detection Control (IDC) defective.
7.
Replace IDC box.
Heater will not turn off.
1.
Thermostat defective.
1.
Replace thermostat.