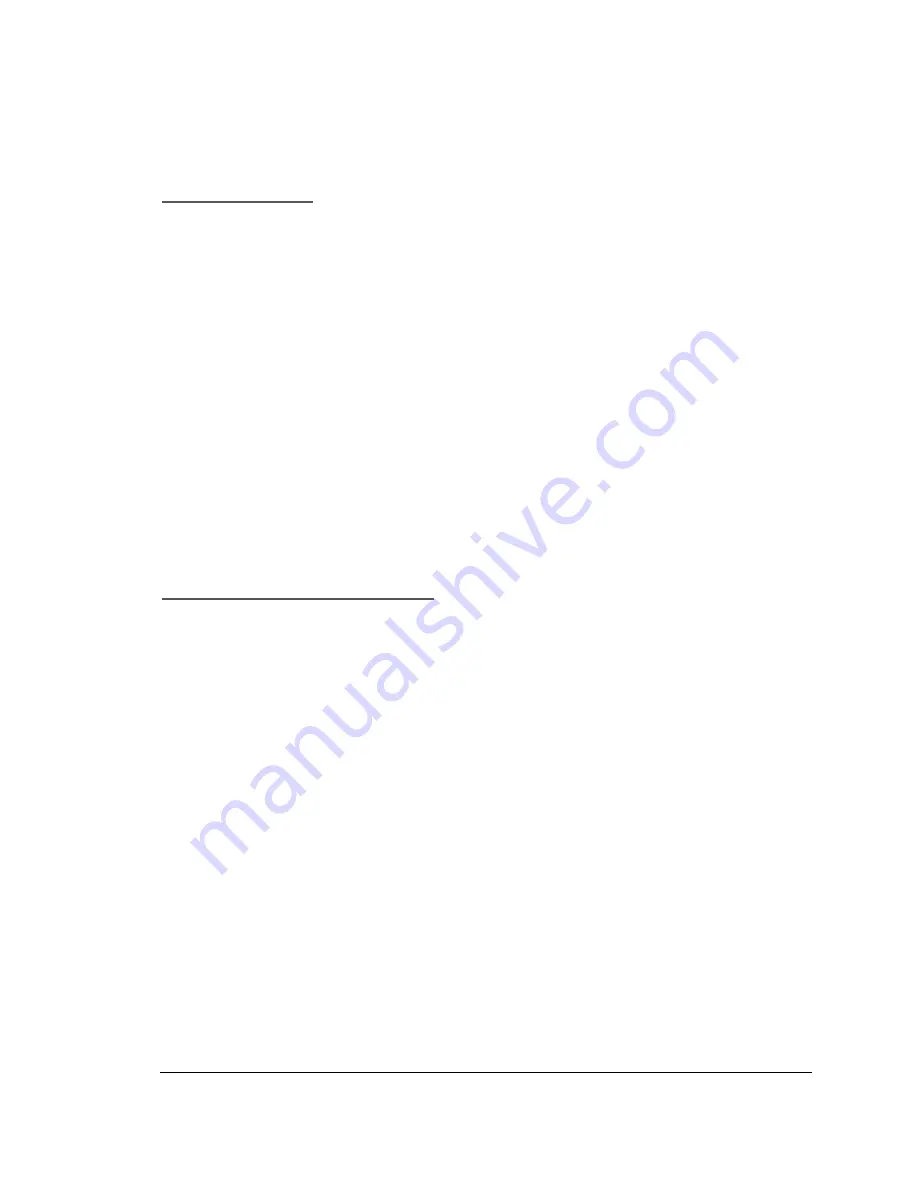
SNOWPURE, LLC, 2005-2018
VERSION 3.5 (XL+EXL)
–FEBRUARY 2018
PAGE 32
The product quality is optimized if the module is in balance and does not have extreme
internal current densities. The quality of the continuous regeneration of the polishing
portion of the bed is critical for achieving the highest resistivities.
Ionic balances and pH
Electrical neutrality must be maintained on an ionic level. It is not possible for more
cations to diffuse than anions.
Because of this, counterions matter highly. If the ions in the feed are made up of a
highly mobile cation and a slow anion, then the EDI “kinetics” will adjust to the rate of the
slowest ions. In addition, the mobile protons (H
+
) and hydroxyls (OH
-
) will play a role in
adjusting the ionic balance. If there is a large mismatch in the ions in the feed, then
there will be large pH shifts between the product and concentrate streams. The quality
will not be optimized.
Therefore, pH highly influences quality. At lower pH, excess protons will diffuse as the
counterions to the feed anions. The feed cations will not be as effectively removed.
At higher pH, there will not be protons to act as fast counter-cations. However, the
carbon dioxide will be more highly charged (carbonate) and therefore more mobile. The
silica, too, is more charged and mobile.
The recommended pH for optimal operation is 7.0 with minimal CO
2
present.
Affecting the location of the “ionic front”
As said above,
the location of the ionic front (the interface between the “working bed” and
the “polishing bed” sections of the EDI module) is important to the quality of the product.
For the highest resistivity water, and the lowest silica, the variables must be set to maximize
the depth of the polishing bed.
The ionic load must be minimized.
The product flow rate should be at the high end of the given range.
The voltage should be at the optimum (not too high or too low).
The concentrate outlet flow should be correct (e.g., 90% recovery) to effectively
remove ions from the surfaces of the membrane in the concentrate chambers.
This will also use more of the applied voltage across the critical purifying
chambers.
The load of carbon dioxide should be minimized.
The pH should be at 7.0.
To save energy, if lower quality water is sufficient for the application, one can extend the
depth of the working bed and limit the depth of the polishing bed. This is achieved by:
Lowering the voltage.
Lowering the concentrate flow (higher recovery)
—this lowers the resistance of
the stack. This can also be achieved with concentrate recirculation or salt
injection. Note: the risk is hardness scaling in the concentrate.