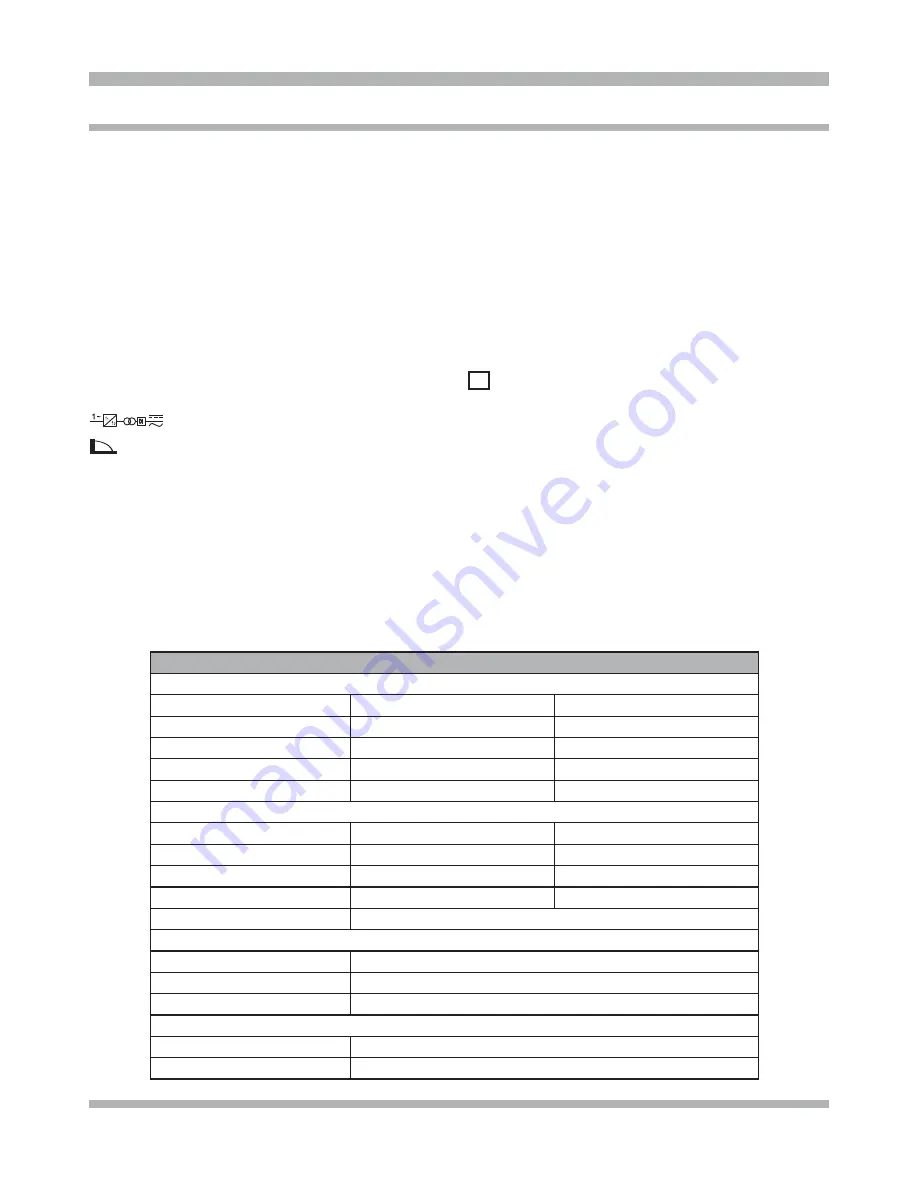
5
GENERAL DESCRIPTIONS
This welder is a constant current welder built using IN-
VERTER technology, designed to weld with stick elec-
trodes and for TIG procedures, with scratch starting.
IT MUST NOT BE USED TO DEFROST PIPES.
EXPLANATION OF TECHNICAL SPECIFICATIONS
LISTED ON THE MACHINE PLATE
This welder is manufactured according to the following
international standards: IEC 60974.1.
N°.
Serial number, which must be indicated on
any type of request regarding the welding
machine.
Single-phase static transformer-rectifier
frequency converter.
Drooping characteristic.
SMAW.
Suitable for welding with covered elec-
trodes.
TIG
Suitable for TIG welding.
U0.
Secondary open-circuit voltage
X.
Duty cycle percentage. % of 10 minutes dur-
ing which the welding machine may run at a
certain current without overheating.
I2.
Welding current
U2.
Secondary voltage with current I2
U1.
Rated supply voltage.
The machine has an automatic supply volt-
age selector.
1~ 50/60Hz 50- or 60-Hz single-phase power supply
I1 max.
This is the maximum value of the absorbed
current.
I1 eff.
This is the maximum value of the actual cur-
rent absorbed, considering the duty cycle.
IP23S
Protection rating for the housing.
Grade 3 as the second digit means that this
equipment may be stored, but it is not
suitable for use outdoors in the rain, unless
it is protected.
S
Suitable for hazardous environments.
NOTE:
The welder has also been designed for use in environ-
ments with a pollution rating of 3. (See IEC 60664).
PROTECTION DEVICES
Thermal cutout
This equipment is protected by a thermostat. When the
thermostat is tripped, the welder stops delivering current
but the fan continues to run. The yellow led (
B
) lights to
indicate when it is tripped. Do not shut off the welder until
the led has gone off.
SPECIFICATIONS
SPECIFICATIONS
Power Input
Voltage
115 Volt
230 Volt
Phase
Single Phase
Single Phase
Frequency
50/60 Hertz
50/60 Hertz
Current (MMA stick welding)
30 Amps @ 100 Amps Output
30 Amps @ 130 Amps Output
Current (TIG welding)
15 Amps @ 100 Amps Output
20 Amps @ 130 Amps Output
Power Output
Duty Cycle/Rated Output
100% @ 70 Amps
100% @ 80 Amps
60% @ 80 Amps
60% @ 90 Amps
35% @ 110 Amps
20% @ 130 Amps
Output Control
Adjustable 10 – 110 Amps
Adjustable 10 – 130 Amps
Power Input Cord
8,6 Feet
Dimensions
Height
13,5 Inches
Width
6,75 Inches
Depth
12,75 Inches
Weight
Base Unit
15 lb
Shipping
16,5 lb
Summary of Contents for TIG 130i
Page 11: ...11 WIRING DIAGRAM ...
Page 12: ...12 REPLACEMENT PARTS PARTS LIST 1 3 2 1 9 8 4 5 6 7 10 11 17 18 12 15 14 16 8 13 19 20 21 ...
Page 15: ...15 ...
Page 16: ...16 ...