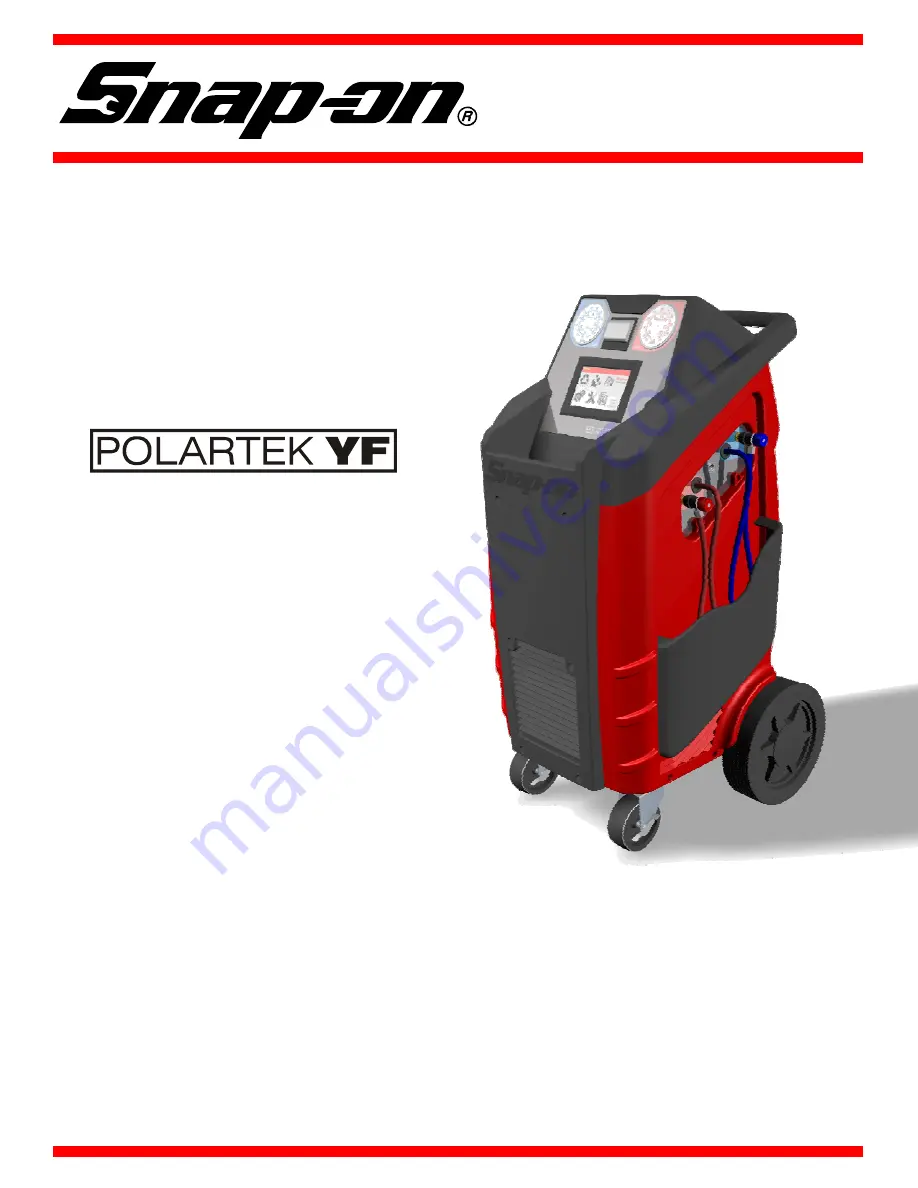
• 1 •
INTRODUCTION
Snap-on
®
Model No. EEAC333 is ETL Laboratories approved, in compliance with SAE J2843. We are dedicated to solving the issues
surrounding the safe containment and proper management of refrigerants. Your new machine incorporates the latest technology
and state of the art features to aid you in servicing R1234yf air conditioning and refrigeration systems. We hope you get as much
enjoyment using this equipment as we did designing and building it.
EEAC333
R1234yf Refrigerant
Recovery / Recycle / Recharge
Service Vehicle A/C System
M A N U E E A C . 3 3 3
E D . 8
Summary of Contents for POLARTEK YF EEAC333
Page 2: ... 2 ...
Page 4: ... 4 REPLACING THE PRINTER PAPER 44 INFO 44 WARRANTY 45 NOTES 46 ...
Page 46: ... 46 NOTES ...
Page 47: ... 47 ...