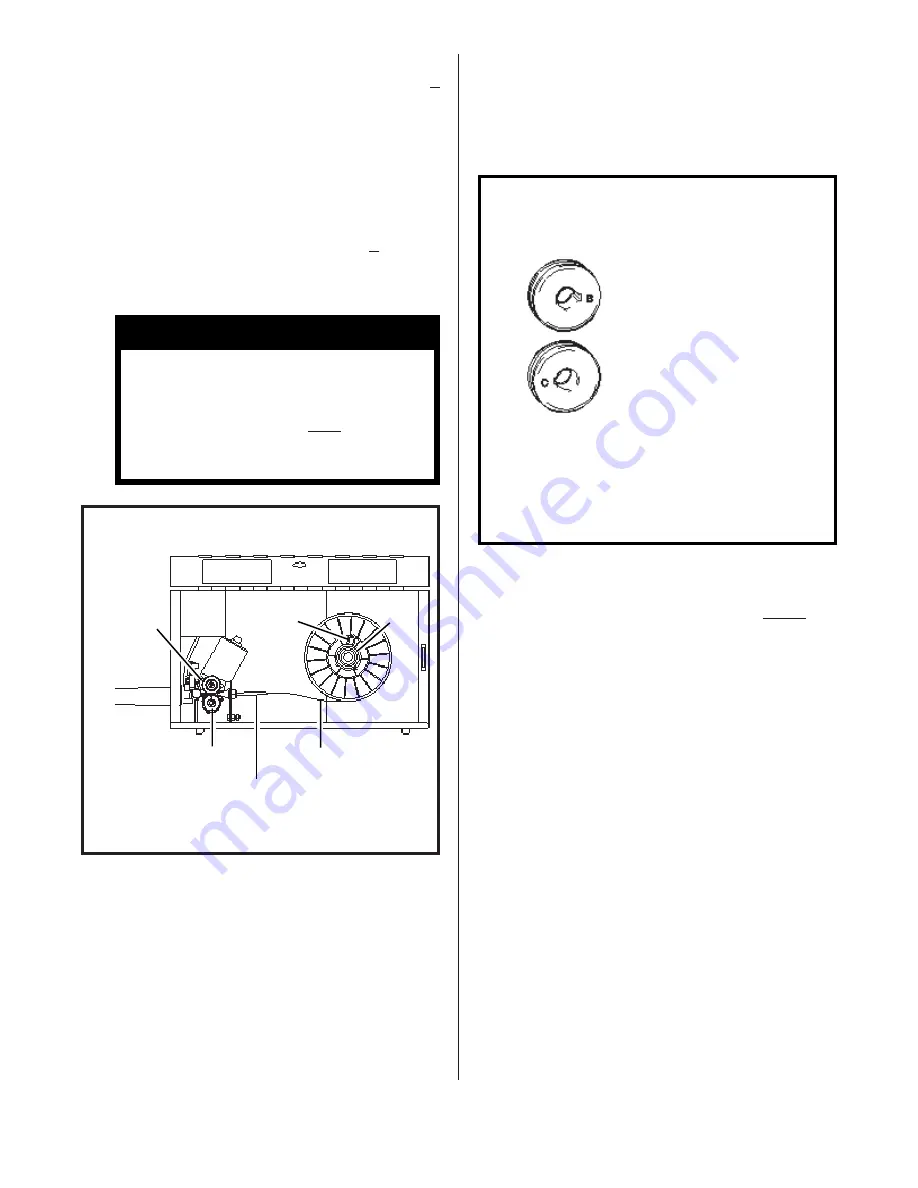
10
FITTING AND THREADING THE ELEC-
TRODE WIRE - ALWAYS USE ER70S-6
WELDING WIRE WHEN WELDING STEEL.
1. Remove the wire spool clip from
the spool hub.
2. Unpack the spool of welding wire
from its protective packaging.
3. Place the spool of ER70S-6 weld-
ing wire onto the hub. The wire
is fed off the bottom of the
spool.
CAUTION
Look for wire protruding
from the center of the
spool. The protruding wire
is electrically HOT during
welding and must not touch
the machine.
6. Make sure the double v-groove
drive roll is installed to match
the wire size. To change the
wire size setting, remove the
drive roll, turn it over and
reinstall it on the shaft.
FIG. 11. FITTING AND THREADING THE ELECTRODE
DRIVE
ROLL
ELECTRODE
(MIG WIRE)
SPOOL
CLIP
PRESSURE
ROLL ARM
SPOOL
HUB
4. Replace the spool clip on the
hub.
5. Unlatch the pressure roll arm
and swing it open.
FIG. 12. DOUBLE GROOVE DRIVE ROLL
"B" SIDE FACING IN FOR
.030" - .035" STEEL WIRES
"C" SIDE FACING IN FOR
.040" - .045" STEEL WIRES
7. Release the wire from the spool
and trim off the kinked end with
wire cutters. The wire must be
straight when it enters the
inlet guide.
8. Thread the electrode wire
through the inlet guide, over
the feed roll and into the liner.
Ensure that the wire locates in
the feed roll groove. Do not
allow the wire on the spool to
loosen.
9. Close and relatch the pressure
roll arm.
10. Stretch the torch cable straight
out in front of the machine
making sure there are no kinks.
Remove the nozzle and contact
tip from the torch.
INLET
GUIDES