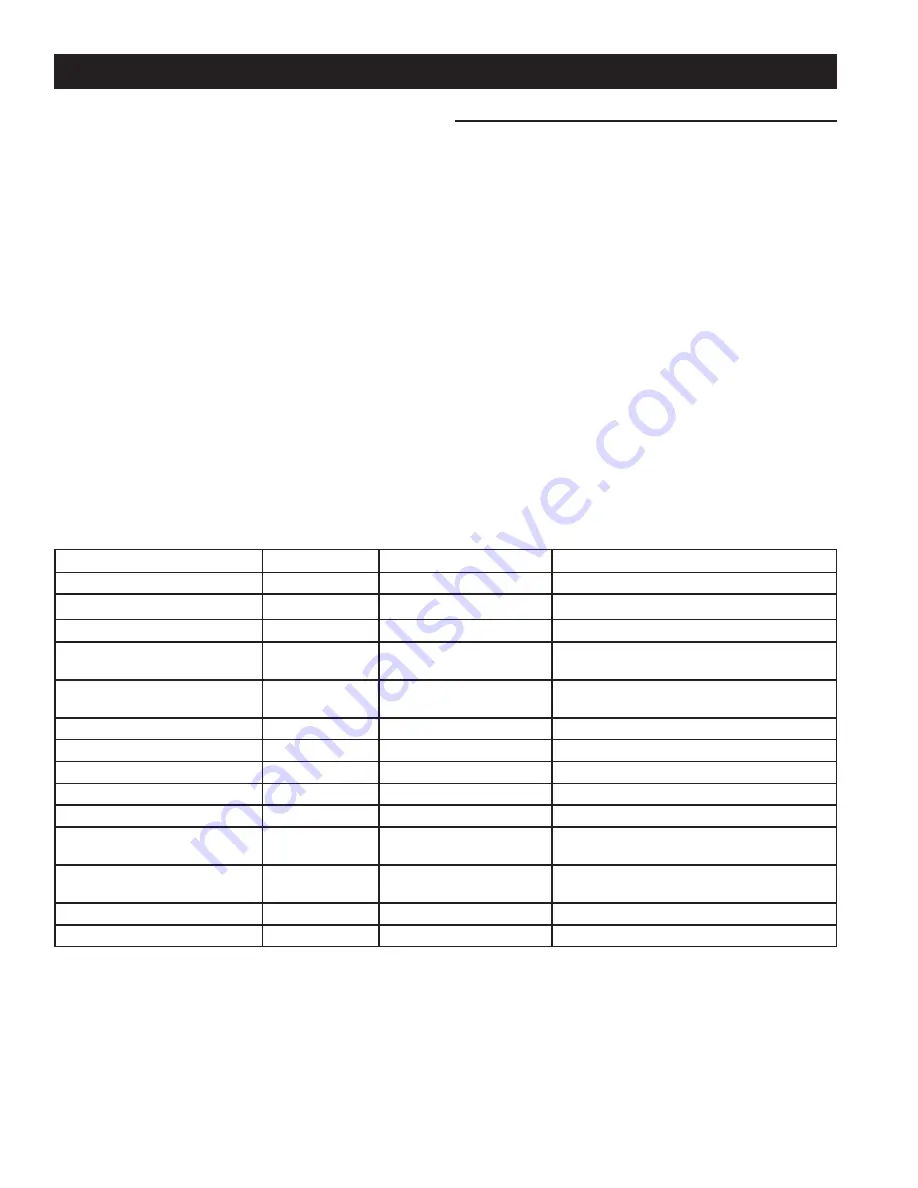
6
Where required by the local authorities having jurisdiction, a fuel
cleaning device such as a filter or strainer should be installed in
the main gas supply line to the unit (see Figure 1 on Page 3).
A gas service pressure regulator is required to maintain the
gas supply pressure below the maximum allowable pressure
indicated on the appliance rating plate. A gas pressure relief
valve, if required by the local code authority, should be installed
upstream of all operating and safety controls in the gas train
and downstream of the gas pressure regulator in the gas supply
line (see Figure 1 on Page 3).
Pertinent operating, cleaning and testing procedures are outlined
in this supplement in the TESTING AND MAINTENANCE section.
A Manufacturer’s/Installing Contractor’s Report for ASME CSD -
1 Certification and Reporting (CG-500) requirements is provided
with the instructions. This report shall be made available to
the authorized inspection agency or the inspector for action
as required by the local jurisdiction. Installing contractors shall
maintain a data report for each installation completed. It is the
responsibility of the installing contractor to deliver the pertinent
operating, cleaning and testing procedures together with the
complete wiring and piping diagrams, to the owner/user and to
obtain a receipt for the instructions. The receipt shall be filed with
the installation report.
TESTING AND MAINTENANCE
Periodic testing of all boiler controls and safety devices is
required to verify correct operation. Precautions shall be taken
to protect against bodily injury or property damage while tests
are being conducted. Cover plates that require removal in
order to gain access to items requiring maintenance or testing
shall be replaced before the boiler is put back in service. Since
it is essential to have all control and safety devices operating
as intended at all times, a periodic testing and maintenance
schedule should be set up and followed with results being logged
on a regular basis. Operators or maintenance technicians should
follow the recommended procedures set forth in the instructions
and allow for any additional circumstances that arise based on the
particular installation when preparing a maintenance program.
The operator or technician should thoroughly understand the
operating procedures and be able to recognize an equipment
malfunction. Obtain a receipt for the instructions. The receipt
shall be filed with the installation report.
Table 1, provided herein is a recommended guideline to follow
for periodic testing of the boiler's safety devices and controls.
Detailed maintenance procedures are included here as well.
ITEMS
FREQUENCY
ACCOMPLISHED BY
REMARKS
1. Gauges and Indicators
Daily
Operator
Visually inspect, log observations.
2. Burner Flame
Daily
Operator
Visually inspect for uniform blue flames.
3. Pilot Burner
Daily
Operator
Visually inspect for uniform flame envelope.
4. Flame Failure Detection
Weekly
Operator
Close Pilot Manual Shutoff Valve, check
safety shutdown time, log results.
5. Gas Valves
Weekly
Operator
Open Operating Control, listen for valve
closure, check for voltage.
6. Flow Switch
Weekly
Operator
See detailed instructions.
7. Vent System
Monthly
Operator
See detailed instructions.
8. Optional Power Vent
Monthly
Operator
See detailed instructions.
9. Burner Components
Monthly
Service Technician
See Owner’s Manual
10. Heat Exchanger Assembly
Semi-Annually
Service Technician
See detailed instructions.
11. Transformer
Semi-Annually
Service Technician
Check primary and secondary voltage, log
results.
12. Manual Reset High Limit and
Auto Reset High Limit
Annually
Service Technician
See detailed instructions.
13. Safety Valves
As Required
Operator
See detailed instructions.
14. Drip Leg and Gas Strainer
As Required
Operator
See detailed instructions.
TABLE 1. PERIODIC TESTING PROCEDURES
TESTING AND MAINTENANCE