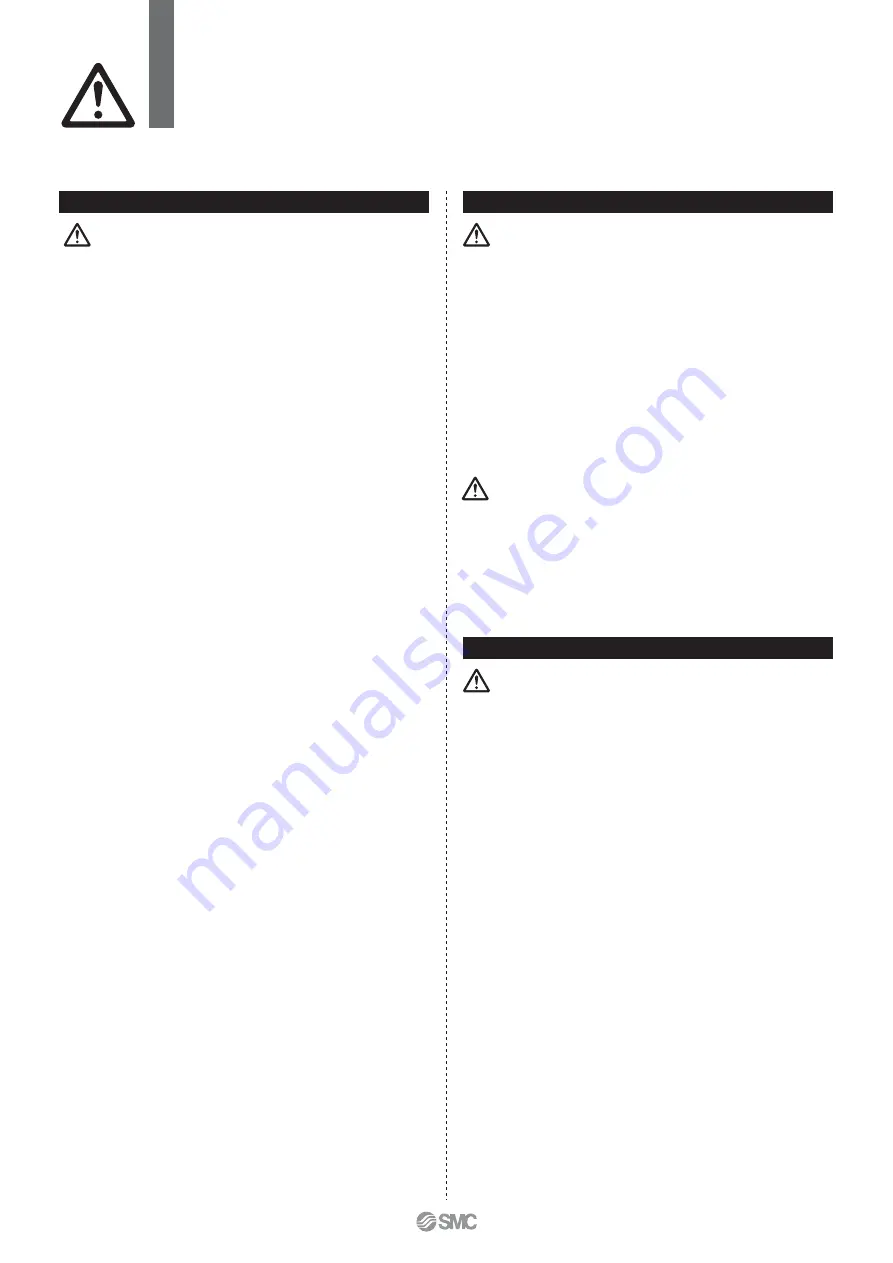
Back page 2
Actuators
Precautions 1
Be sure to read this before handling.
1. There is a possibility of dangerous sudden
action by air cylinders if sliding parts of machin-
ery are twisted due to external forces, etc.
In such cases, human injury may occur; e.g., by catching
hands or feet in the machinery, or damage to the machinery
itself may occur. Therefore, the machine should be adjusted to
operate smoothly and designed to avoid such dangers.
2. A protective cover is recommended to mini-
mize the risk of personal injury.
If a stationary object and moving parts of a cylinder are in
close proximity, personal injury may occur. Design the
structure to avoid contact with the human body.
3. Securely tighten all stationary parts and connected
parts so that they will not become loose.
Especially when a cylinder operates with high frequency or is
installed where there is a lot of vibration, ensure that all parts
remain secure.
4. A deceleration circuit or shock absorber may
be required.
When a driven object is operated at high speed or the load is heavy,
a cylinder’s cushion will not be sufficient to absorb the impact. Install
a deceleration circuit to reduce the speed before cushioning, or
install an external shock absorber to relieve the impact.
In this case, the rigidity of the machinery should also be examined.
5. Consider a possible drop in circuit pressure
due to a power outage, etc.
When a cylinder is used in a clamping mechanism, there is a
danger of workpieces dropping if there is a decrease in clamping
force due to a drop in circuit pressure caused by a power outage,
etc. Therefore, safety equipment should be installed to prevent
damage to machinery and human injury. Suspension mechanisms
and lifting devices also require consideration for drop prevention.
6. Consider a possible loss of power source.
Measures should be taken to protect against bodily injury and
equipment damage in the event that there is a loss of power to
equipment controlled by pneumatics, electricity, or hydraulics.
7. Design circuitry to prevent sudden lurching
of driven objects.
When a cylinder is driven by an exhaust center type directional
control valve or when starting up after residual pressure is
exhausted from the circuit, etc., the piston and its driven object
will lurch at high speed if pressure is applied to one side of the
cylinder because of the absence of air pressure inside the
cylinder. Therefore, equipment should be selected and circuits
designed to prevent sudden lurching, because there is a danger
of human injury and/or damage to equipment when this occurs.
8. Consider emergency stops.
Design so that human injury and/or damage to machinery and
euqipment will not be caused when machinery is stopped by a
safety device under abnormal conditions, a power outage or a
manual emergency stop.
9. Consider the action when operation is restarted
after an emergency stop or abnormal stop.
Design the machinery so that human injury or equipment
damage will not occur upon restart of operation.
When the cylinder has to be reset at the starting position,
install manual safely equipment.
Caution on Design
Warning
Warning
1. Confirm the specifications.
The products featured in this catalog are designed for use in
industrial compressed air systems. If the products are used in
conditions where pressure and/or temperature are outside the
range of specifications, damage and/or malfunctions may
occur. Do not use in these conditions. (Refer to the specifica-
tions.)
Please consult with SMC if you use a fluid other than
compressed air.
2. Intermediate stops
When intermediate stopping of the cylinder piston is performed
by a 3 position closed center type directional control valve, it is
not possible to maintain the stop position for an extended time
due to the construction of the metal seal cylinder.
Selection
Caution
1. Be certain to match the rod shaft center with
the direction of the load and movement
when connecting.
When not properly matched, problems may arise with the rod
and tube, and damage may be caused due to friction on areas
such as the inner tube surface, bushings, rod surface and
seals.
2. When an external guide is used, connect the
rod end and the load in such a way that there
is no interference at any point within the
stroke.
3. Do not scratch or gouge the sliding parts of
the cylinder tube or tube rod, etc., by striking
or grasping them with other objects.
Cylinder bores are manufactured to precise tolerances, so that
even a slight deformation may cause malfunction. Also,
scratches or gouges, etc., in the tube rod may lead to
damaged seals and cause air leakage.
4. Prevent the seizure of rotating parts.
Prevent the seizure of rotating parts (pins, etc.) by applying
grease.
Mounting
1. Operate the piston within a range such that collision
damage will not occur at the stroke end.
2. When controlling cylinder output, do not create a
restricting circuit by using a speed controller, etc.
Pressure inside the cylinder will drop and control
will become impossible. Be sure to control actuation
through pressure control.
Caution