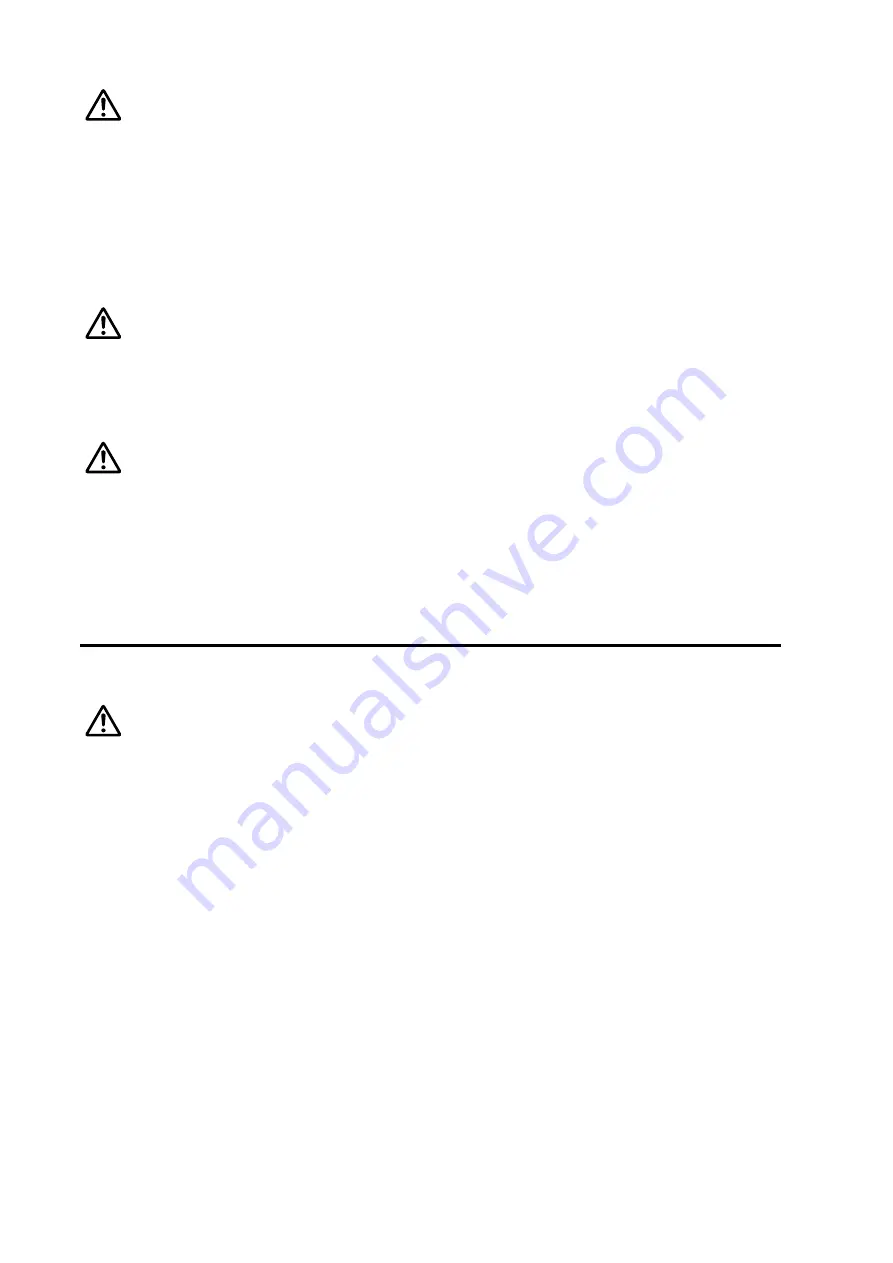
- 28 -
5-6. Operating environment
Warning
1. Do not use in an atmosphere containing corrosive gases, chemicals, sea water, water, water
steam, or where there is direct contact with any of these.
Refer to each construction drawing for information on the materials of air grippers.
2. Do not expose the product to direct sunlight for an extended period of time.
3. Do not use in a place subject to heavy vibration and/or shock.
4. Do not mount the product in locations where it is exposed to radiant heat.
5. Do not use in dusty locations or where water, oil, etc., splash on the equipment.
6. A decrease in the base oil of grease may be accelerated by the properties of the compressed air
used in pneumatic equipment, the external environment, operating conditions, etc., and the
resulting drop in lubricating performance may have an effect on the
equipment’s service life.
Caution
1. Internal lubricant or the base oil of grease may seep out of the cylinder depending on the
operating conditions (an ambient temperature of 40
°
C or more, pressure retention, low-frequency
actuation, etc.). Take great care when a clean environment is required.
5-7. Lubrication
Caution
Magnet gripper is lubricating non-lube type.
These cylinders have been lubricated for life at the factory and can be used without any further lubrication.
However, in the event that it is additionally lubricated, be sure to use class 1 turbine oil (with no additives)
ISO VG320. Do not use machine oil or spindle oil. Stopping lubrication later on may lead to a malfunction
because the new lubricant will displace the original lubricant. Therefore, lubrication must be continued once
it has been started. If turbine oil is used, refer to the corresponding Safety Data Sheet (SDS).
6. Maintenance or inspection
6-1. Maintenance or inspection
Warning
1. Perform maintenance and inspection according to the procedures indicated in the operation
manual.
If handled improperly, human injury and/or malfunction or damage of machinery and equipment may occur.
2. Maintenance work
If handled improperly, compressed air can be dangerous. Assembly, handling, repair, and element
replacement of pneumatic systems should be performed by a knowledgeable and experienced person.
3. Drain flushing
Remove drainage from air filters regularly.
4. Removal of equipment, and supply/exhaust of compressed air
Before components are removed, first confirm that measures are in place to prevent workpieces from
dropping, run-away equipment, etc. Then, cut off the supply pressure and electric power, and exhaust all
compressed air from the system using the residual pressure release function. When machinery is restarted,
proceed with caution after confirming that appropriate measures are in place to prevent sudden movement.