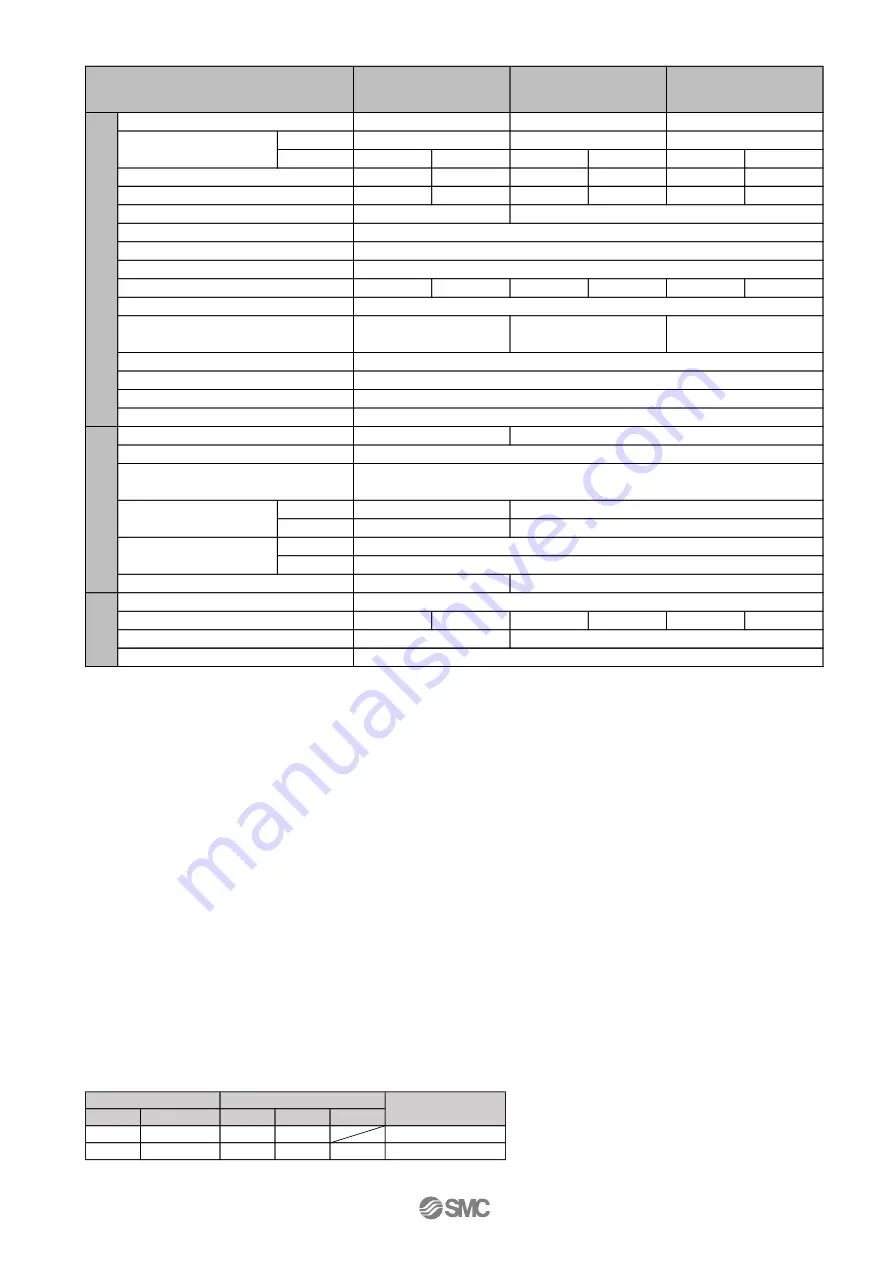
-6-
LESYH*(D,R,L)*
(
T6/T7
) ・・・
Motor type T6/T7
Horizontal
Vertical
6
12
10
20
10
20
65 to 131
127 to 255
79 to 157
154 to 308
98 to 197
192 to 385
400
200
400
200
400
200
12
6
20
10
16
8
Horizontal
Vertical
Horizontal
Vertical
131
255
157
308
197
385
Pushing speed [mm/s]
*2
35 or less
30 or less
Model
LESYH16*T6
LESYH25R/LT7
(Parallel)
LESYH25DT7
(In-line)
A
ct
u
a
to
r
sp
e
ci
fi
ca
ti
o
n
s
Stroke[mm]
50,100
50,100,150
50,100,150
Max. work load [kg]
8
12
12
Force [N](Set value: 12 to 24%)
*1
Max. speed[mm/s]
Max. acceleration/deceleration[mm/s
2
]
5000
Positioning repeatability [mm]
±0.01
Lost motion [mm]
*3
0.1 or less
Lead [mm] (including pulley ratio)
Impact/Vibration resistance [m/s
2
]
*4
50/20
Actuation type
Ball screw(In-line)
Ball screw+Belt(parallel)
Ball screw+Belt[1.25:1]
Ball screw
Guide type
Linear guide (Circulating type)
Operating temperature range [°C]
5 to 40
Operating humidity range [%RH]
90 or less (No condensation)
E
le
ct
ri
c
sp
e
ci
fi
ca
ti
o
n
s
Motor output/Size
100W/□40
200W/□60
Motor type
AC servo motor (200 VAC)
Encoder
[LECSB-T□,LECSS-T□,LECSN-T□]:Absolute 22-bit encoder (Resolution: 4194304 p/rev)
[LECSC-T□]:Absolute 18-bit encoder (Resolution: 262144 p/rev)
Standby power consumption
when operating [W]
*6
2
8
Regeneration option
May be required depending on speed and work load
Power
consumption [W]
*5
45
65
145
175
Lo
ck
u
n
it
sp
ec
if
ic
at
io
n
s
Type
*8
Non-magnetizing lock
Holding force[N]
Power consumption [W] at 20°C
*9
6.3
7.9
Rated voltage [V]
24 VDC 0/−10%
Max. instantaneous power consumption [W]
*7
445
724
* 1 The force setting range (set values for the driver) for the force control with the torque control mode. Set it with reference
to “Force Conversion Graph” of the catalog.
The driver applicable to the pushing operation is "LECSB-T", "LECSS", and "LECSS-T. "
The LECSB-T is only applicable when the control method is positioning. The point table is used to set the pushing
operation settings.
To set the pushing operation settings, an additional dedicated file (pushing operation extension file) must be
downloaded separately to be used with the setup software (MR Configurator2
™
: LEC-MRC2
□
).
Please download this dedicated file from the SMC website: https://www.smcworld.com/
When selecting the LECSS or LECSS-T, combine it with a master station (such as the Simple Motion module
manufactured by Mitsubishi Electric Corporation) which has a pushing operation function.
* 2 Allowable impact speed when "impact work" in torque control mode, etc.
* 3 A reference value for correcting an error in reciprocal operation.
* 4 Impact resistance: No malfunction occurred when the actuator was tested with a drop tester in both an axial direction
and perpendicular direction to the lead screw. (The test was performed with the actuator in the initial state.)
Vibration resistance: No malfunction occurred in a test ranging between 45 to 2000 Hz, when the actuator was tested in
both an axial direction and a perpendicular direction to the lead screw. (The test was performed with the actuator in
the initial state.)
* 5 The power consumption (including the controller) is for when the actuator is operating.
* 6 The standby power consumption when operating (including the controller) is for when the actuator is at the set position
during the opration. Except during the pushing operation.
* 7 The maximum instantaneuos power consumption (including the controller) is for when the actuator is operating. This
value can be used for the selection of the power supply.
* 8 Only when the motor option, "with lock", is selected.
* 9 For an actuator with lock, add the power consumption for the lock.
Product weight
[kg]
Size
Motor type
50
100
150
16
T6
2.02
2.41
0.30
25
T7
3.77
4.37
5.77
0.40
Model
Stroke
Additional weight
with lock