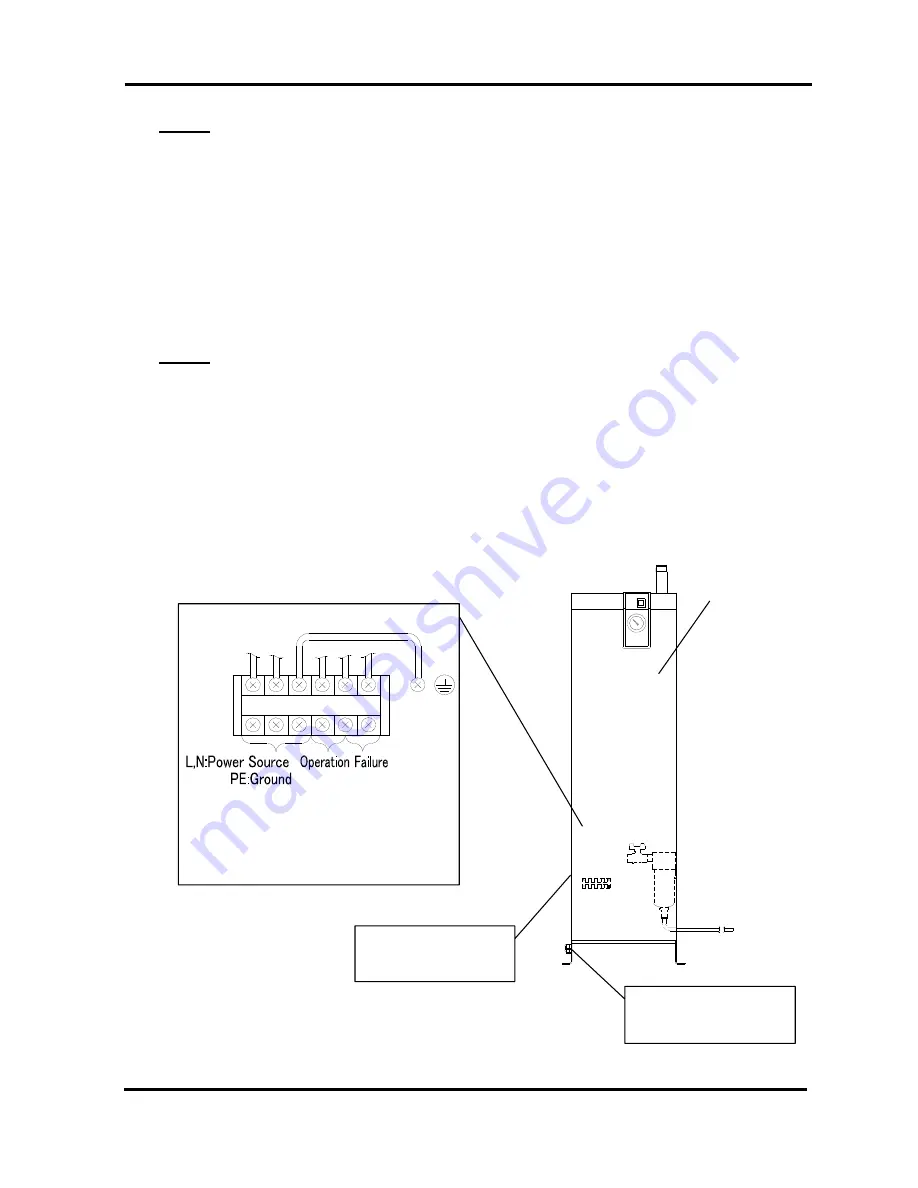
10 Specification for Option T
10 - 2
Terminal block
Grommet
Signal code inlet
Rubber grommet
Power code inlet
10 - 3 Remote operation
・
For the remote operation, turn on and off the power supply side under the condition of the
illuminated switch ON.
・
Keep 3 min. at minimum after stopping the product to restart even for the remote operation. If the
product is restarted within less than 3 min., protective equipment (overload relay) may activate and
prevent the product from restarting.
Additionally, the frequency to start and stop the operation must be restricted to 5 times per hour (to
prevent breakage of the motor).
10 - 4 How to connect the power supply and signal cable
Connect the power cable and signal cable in the following procedures.
1) Take off the front panel.
2) Insert the power cable prepared by the customer into the power code inlet (with rubber
grommet) and bring the power cable near the terminal block through the base hole.
3) Connect the power cable to the terminal.
4) Insert the signal cable prepared by the customer into the signal code inlet (with rubber
grommet) and bring the signal cable near the terminal block.
5) Connect the signal cable to the each terminal.
6) Put back the front panel.
Front panel
Customer connection side
Terminal connecting screw: M3
Crimping terminal width: 6.5mm and below
Applicable electrical wire:1.25mm
2
or more
1 2 3
PE
N
L