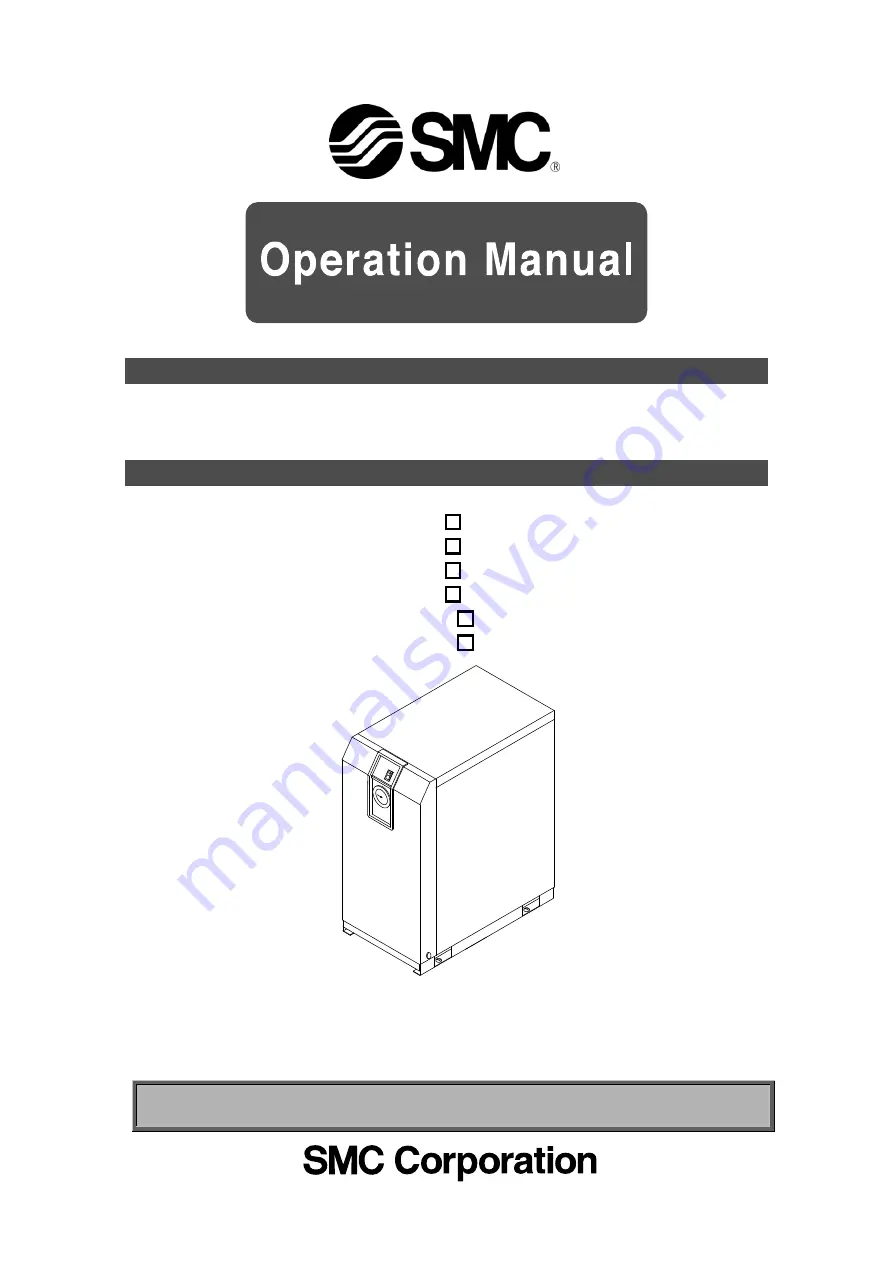
IDX-OM-W019-B
PRODUCT NAME
Refrigerated Air Dryer
MODEL / Series
IDFB3E-11 -A,S
IDFB4E-11 -A,R,T,S,V
IDFB6E-11 -A,K,R,T,S,V
IDFB8E-11 -A,K,R,T,S,V
IDFB11E-11 -A,K,R,T,S,V
IDFB15E-11 -K,R,T,S,V
Please read this manual prior of using the air dryer.
Keep the manual readily available for reference.
This manual is intended to explain the installation and operation of the product.
Only those who have thorough understanding of the fundamental operating
procedure or have basic knowledge and skills of handling industrial products
are qualified to perform installation and operation.