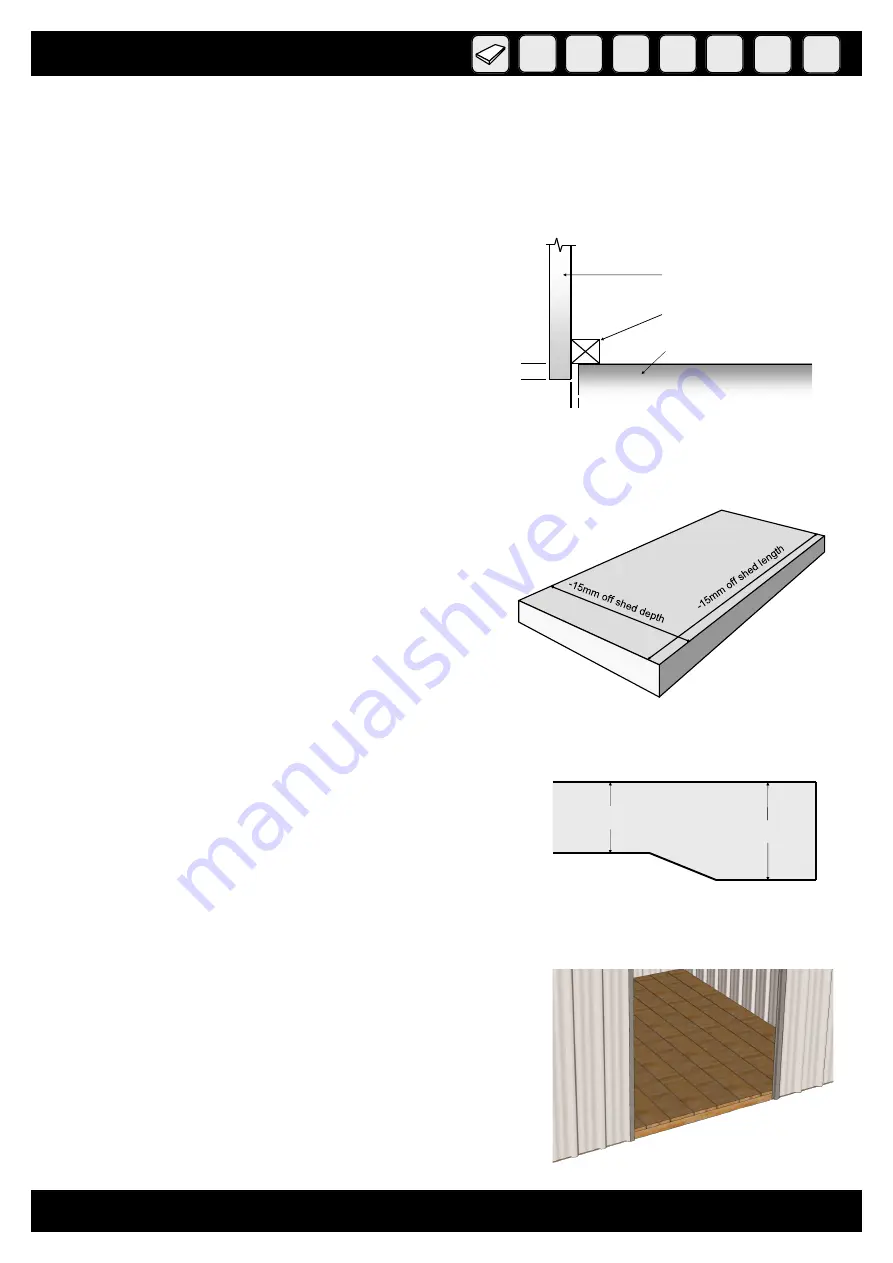
FOUNDATION
SMART STORE WOODEN FLOOR
The optional Smart Store kitset wooden floor is precut and
designed to be fitted into the shed after the shed is assembled.
Assemble shed as per instructions and fit floor last.
(see page 12 for details).
CONCRETE SLAB FOR RAISED BASE PLATE SHED
To build a raised concrete slab for your shed to sit on, we recom-
mend the following:
The raised slab size should be 15mm smaller than the base
size of the shed and at least 30mm above ground line.
The slab should be 80mm thick in the middle and 100mm
thick around the edges.
The slab should be laid on a solid or compacted base.
Plastic sheeting under slab will prevent moisture coming
through from underneath
.
During construction, you may raise the bottom timber
plate to allow the wall cladding to protrude 20mm below
the bottom plate. This will stop water flowing between
the bottom plate and the concrete floor.
See note on page 7.
80mm
100mm
7.5mm
20mm
Concrete Floor
Base Plate
Wall Cladding
5
RAISED BASE PLATE OPTION
(For sheds placed on a raised concrete floor)
No doubt by now you will have decided what sort of base you are putting down.
Please read the section that applies to your situation.
If you choose to pour a concrete base you will need to decide whether you wish to raise the base plate of your shed.
This allows the cladding to protrude below the surface of the concrete and ensures a water tight pad.
See concrete pad specifications below
By choosing this option you will need to make the pad to the specification below.
Summary of Contents for SS1507
Page 1: ...ASSEMBLY INSTRUCTIONS SS1507 BASE SIZE 1 520m x 0 685m ...
Page 2: ......
Page 14: ......