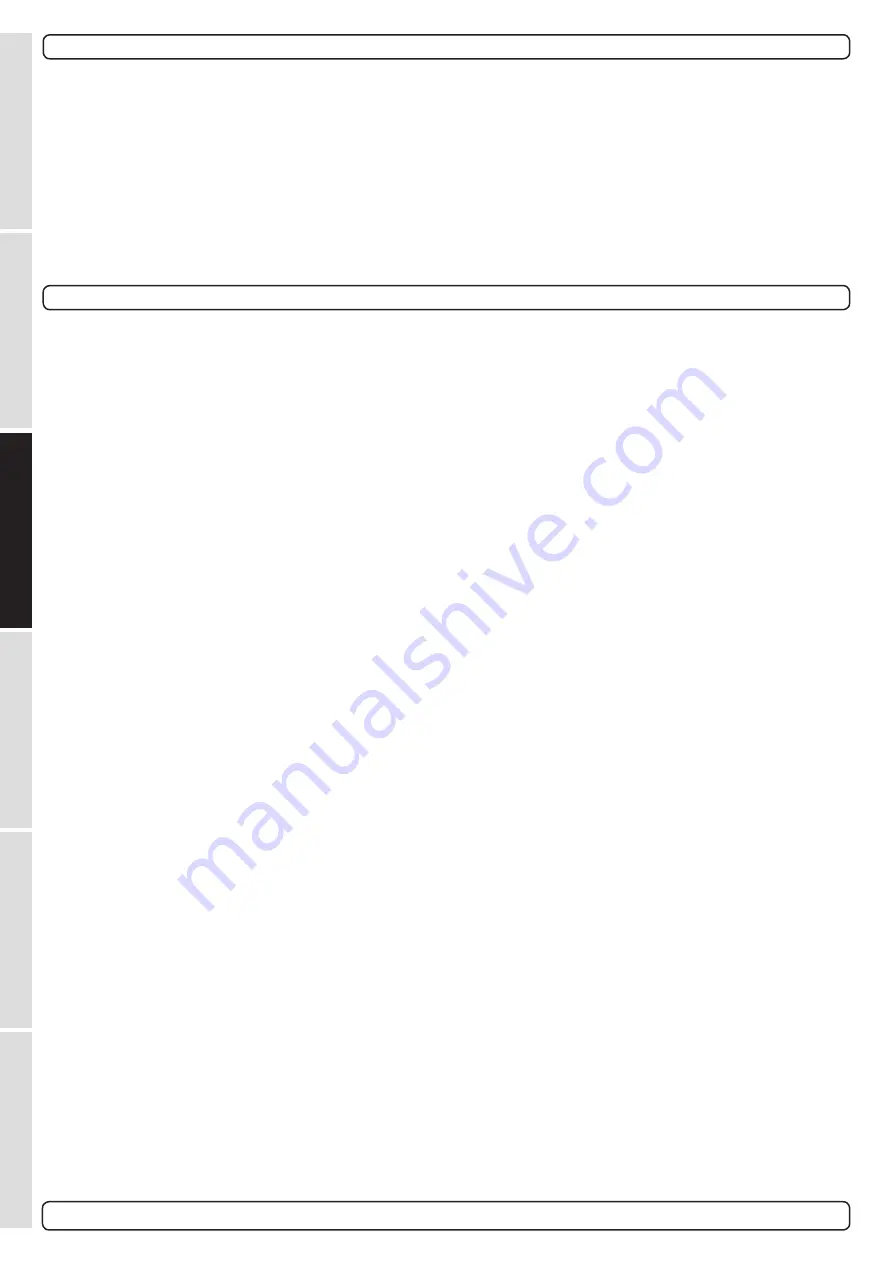
Before you start to install the electric wiring and connections, it’s important to remove the positive battery terminal.
Side-Power hydraulic systems comes with a prewired electrical control/junction box.
Cables to be installed are:
• 12V or 24V DC power feed to control/junction box. Use 1.5 mm
2
wire size.
• From the junction box to each of the control and info panels. Use 1 mm
2
wire size (3-9 lead multi cable, depending on type of
control panel).
• Non-Thruster consumers are not prewired by Side-Power. Use 1 mm
2
multi cable.
More detailed information is found in the unique electrical wiring schematic.
Electrical wiring
10
SYSTEM OVER
VIEW
INST
ALLA
TION
ST
ART UP
USER MANUAL
SER
VICE
TECHNICAL
SPECIFICA
TIONS
CHECK LIST
Before startup:
Hoses and fittings are in accordance to the hose list in the unique hydraulic system drawing. (Sizes and pressure ratings)
All connections are tight and secure.
Oil level is ok.
The oil tank is properly fastened and grounded.
There is enough space arond the oil tank to change filters, fill oil and inspect the gauges and indicators.
The oil tank is placed high enough to pressurize the pump feed port. (oil level above the pump)
Cooling water is connected to the oil coolers. (approx 15 l/min, max 30°C)
30°C)
Pump drive direction will correspond with the power source drive direction
Front mounted pump is alligned to the power source crank shaft, and fixed to move with the power source.
The pump is prefilled with oil.
The drain line is connected to the upper drain port at the pump.
The LS line is connected to the pump. Correct adaptor/fittings is used (NOT JIC threads).
A drain line is connected to the thruster(s).
After
startup:
Standby pressure is 10-30 bar. (seen at the pressure gauge at the control valve on the oil tank)
No leakages.
Oil level/temp is ok.
The thrust direction is in accordance to the joystick movement.
All control stations are connected and working properly.
The oil pressure when running each of the hydraulic consumers is in accordance to the setup in the system manual.
The filter indicators are ok when running a large consumer (high oil flow).
Hydraulic system serial no.: ....................................
Standby pressure: ............... bar
System work pressure (bowthruster): ............... bar
System work pressure (sternthruster): ............... bar
System work pressure (extra consumer #1): ............... bar
(..#2): ............... bar
(..#3): ............... bar
The hydraulic thruster system has been installed as per the instructions in this manual and all points in checklist above have been
controlled.
Signed: ................................................................................................
Date: ....................................................................................................
Sidepower Hydraulic System
2.3 - 2006