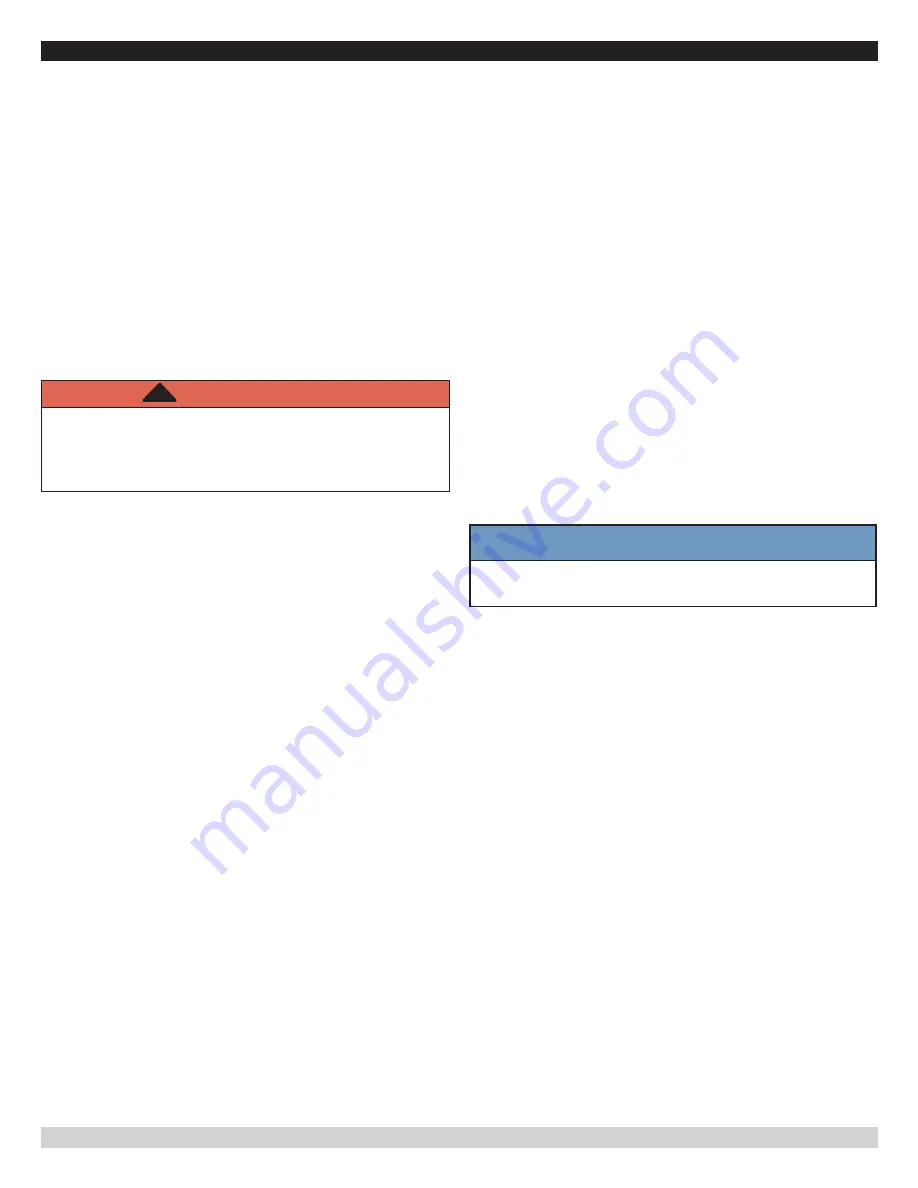
3
P/N 473915000
GENERAL BOILER MAINTENANCE
General Maintenance During Operation
• Have a qualified service technician perform preventive
maintenance prior to heating season.
• Preventive maintenance of oil fired boiler reduces
operating costs.
• Boiler and vent pipe should be inspected for
accumulation of soot or scale deposits periodically but
a least once every year before start of the heating
season. When soot is present on the section walls of
the flue ways, improper combustion will result, causing
additional sooting and scaling until flue ways are
completely closed.
• Boiler installer should have provided an emergency
power isolation switch located within 5 feet of the
boiler.
WARNING
Electrical shock hazard. Disconnect power to
boiler with emergency power isolation switch when
servicing boiler. Failure to do so could result in death
or serious injury.
!
Oil Burner Maintenance
Have a qualified service technician perform oil burner
maintenance.
1.
Oil Burner Motor - Add two-three drops of non-
detergent electric motor oil to each cup located at front
and rear of motor if so equipped. Excessive oiling will
shorten life expectancy of motor.
2.
Fuel Filter - Replace to prevent contaminated fuel from
reaching nozzle. A partially blocked fuel filter can lead
to premature failure of the fuel pump.
3.
Fuel Pump - Replace pump screen and clean pump to
maintain reliable fuel delivery to nozzle.
4.
Ignition Electrodes - Clean and adjust per
manufacturer's recommendations, to maintain reliable
ignition of the oil.
5.
Nozzle - Replace annually to maintain safer and reliable
combustion efficiency.
6.
Fan and Blower Housing - Keep clean, and free of dirt,
lint and oil to maintain proper air fuel requires to burn.
Boiler Cleaning Instructions
• Have a qualified service technician perform cleaning.
• Shut off all electrical power to boiler/burner and shut
off fuel supply.
• Remove 4 bolts for access to combustion chamber. If
boiler is equipped with flexible fuel lines, swing door
open.
• Remove vent connector.
• Remove baffles for cleaning. 4,5,6 section boilers are
factory equipped with pair of baffles installed in third
pass (two inner flueways).
• Clean 3rd pass - insert 2" diameter x 42" long wire
or fiber bristle brush into each of the two 3rd passes.
Using long strokes, push brush all the way through the
boiler until brush has exited the smoke box opening.
Pull the brush all the way forward until it exits the front
of the boiler. Continue this operation for the entire
length of flue way until clean. Repeat operation in other
3rd pass flue way.
• Clean 2nd pass - insert 2" diameter x 42" long wire
or fiber bristle brush into each of the two 2nd passes.
Using long strokes, push brush all the way through the
boiler until brush hits back wall of reversing chamber.
Pull the brush all the way forward until it exits the front
of the boiler. Continue this operation for the entire
length of flue way until clean. Repeat operation in other
2nd pass flue way.
• Vacuum loose debris in bottom of combustion chamber
and smoke box.
• See Installation, Operation & Maintenance Manual for
more information.
Shutting Down The Boiler for Extended Periods
of Time
NOTICE
Keep oil supply valve shut Off if burner is shut down
for extended period of time.
• Turn off electrical power to boiler using field
installed fused disconnect switch if boiler is shut
down for extended period.
• When restarting boiler from extended shut-down,
follow Operating Instructions in the Installation,
Operation & Maintenance Manual.