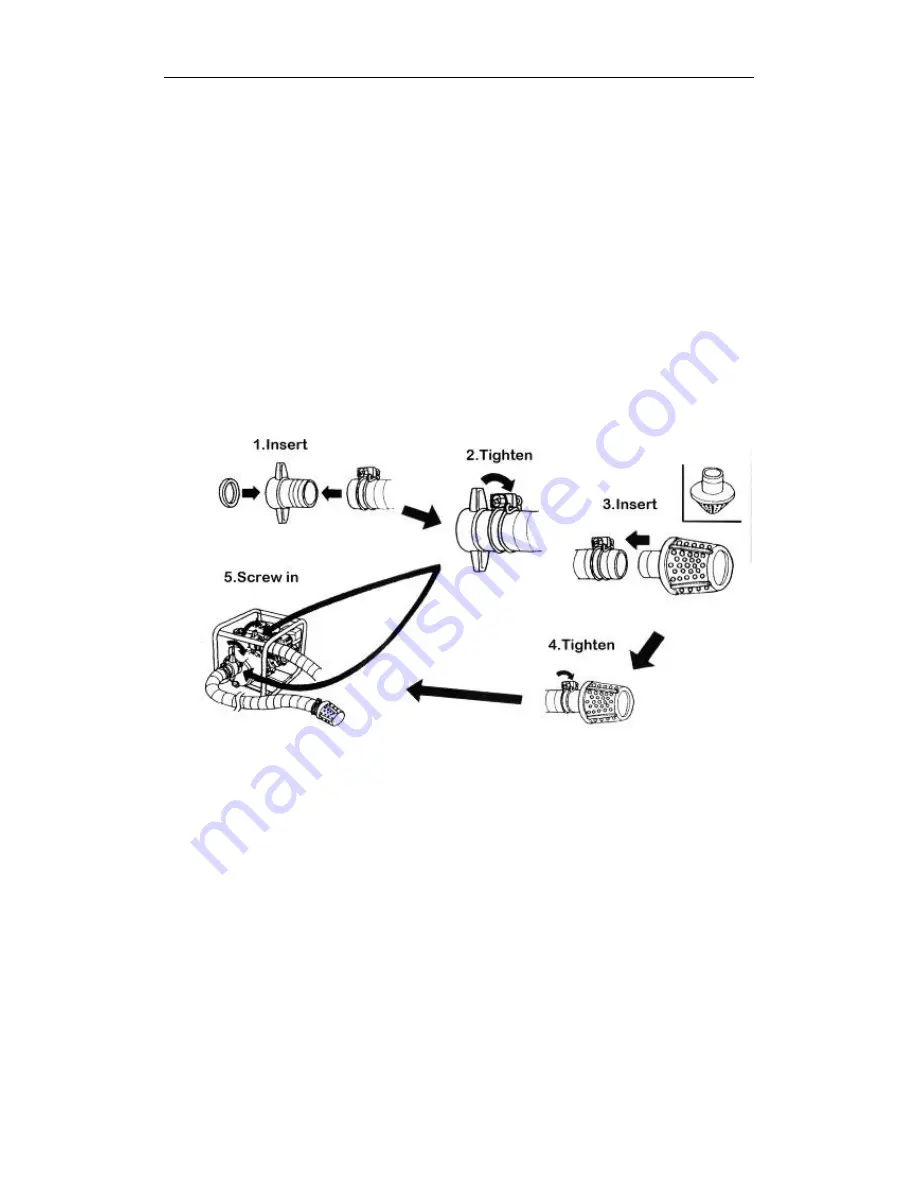
PRE-OPERATION PREPARATION
Suction Hose
The first step in preparing the pump for operation is to install the suction
hose. For
the suction hose,
use a reinforced-wall or wire braided hose to prevent suction collapse. A short hose is recommended
over a
long
hose.
The
pumps have standard National Pipe Threads on them; therefore, any
standard
hose set will
fit with the pump.
If your hoses
arc
metric threads or any other standard, please give our
company a call and we may carry a
full line of
adapters or provide
you with a
possible solution.
NOTE: Always install the provided strainer on the end of the suction hose before pumping. If gravel or
debris enters the pump, the impeller can he seriously damaged.
Shown below
is
the pump hose utilizing
a
barbed connection and hose clamp. If you already
have specialized hose, disregard the following diagram. When using the barbed connection
setup, make sure to use a hose clamp to properly secure the hose to the barb connector.
Discharge hose
The second step is
to
install the discharge hose. The discharge hose can be fabric, just make
sure to use a hose clamp to secure the hose to the barb. This will prevent the hose from
disconnecting under high pressure.
Note: A short and large-diameter hose is preferred over any other. A
short and large
diameter
will
provide lower
fluid
friction
and
improve efficiency.
Summary of Contents for PROFESSIONAL SERIES 30TP
Page 6: ...Wiring Diagram optional for electric start models only ...
Page 14: ......