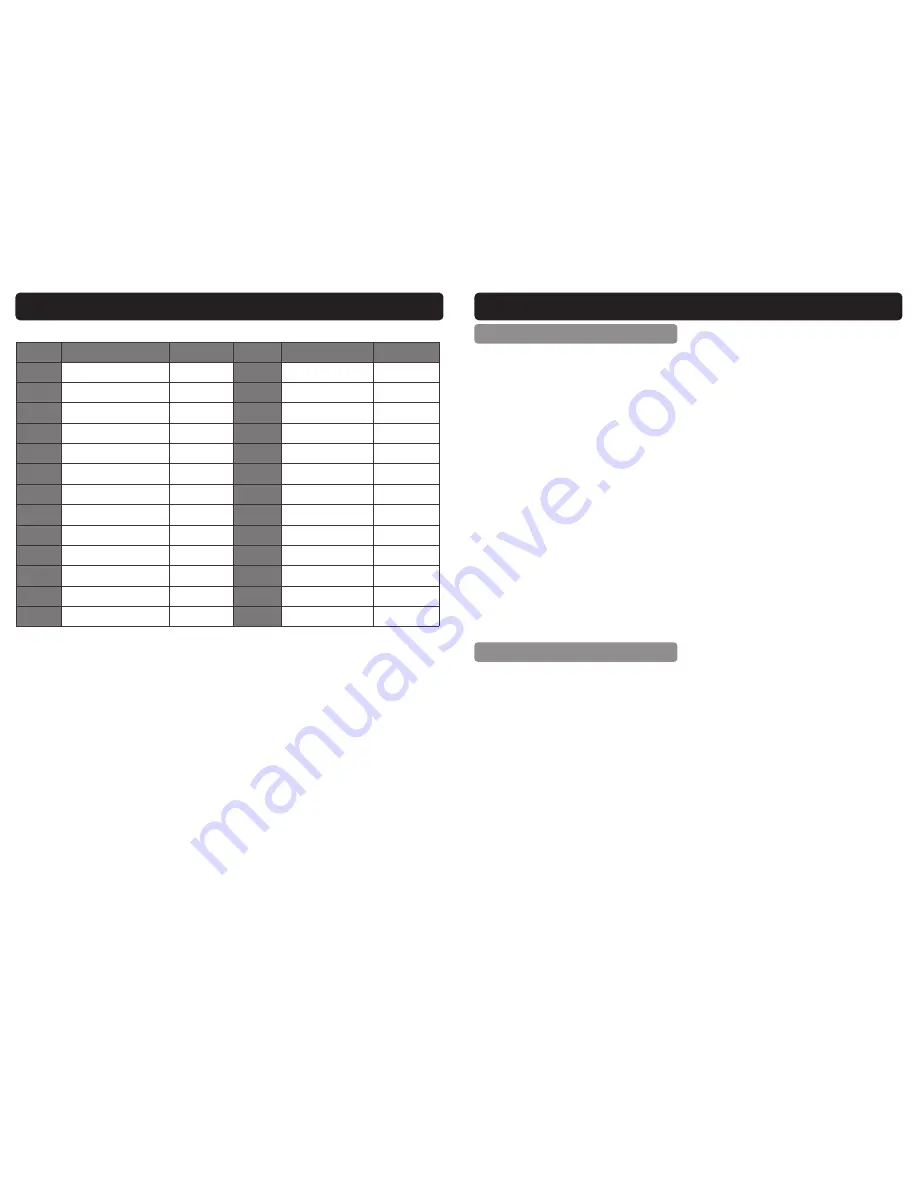
30
PARTS LIST WFU 05776
Ref. No.
Description
Sip Part No.
Ref. No.
Description
Sip Part No.
1.
Spool Cover
WE02-00357
14.
Wire Feed Motor
WE02-00370
2.
Torch Rest
WE02-00358
15
Plastic Hinge
WE02-00371
3.
Enclosure
WE02-00359
16
Dinse socket
WE02-00372
4.
Potentiometer
WE02-00360
17
Reel Hub Assembly
WE02-00373
5.
Front panel
WE02-00361
18.
Control Socket
WE02-00374
6.
Potentiometer Knob
WE02-00362
19.
Cable Support
WE02-00375
7.
Wire Feed Pot Knob
WE02-00363
20.
Solenoid Valve
WE02-00376
8.
Push Fit Water Socket
WE02-00364
21.
Push Fit Water Socket WE02-00377
9.
Plastic Euro Surround
WE02-00365
22.
Control Cable
WE02-00378
10.
Euro Torch Socket
WE02-00366
23.
Gas Hose
WE02-00379
11.
Castor Wheel
WE02-00367
24.
Connecting Cable
WE02-00380
12.
Bottom Frame
WE02-00368
25.
Earth Lead Complete
WE02-00381
13.
Left Side Panel
WE02-00369
7
SAFETY INSTRUCTIONS….cont
ELECTRIC SHOCK
FIRE
Electric inverter welders have the potential to cause a shock that could lead to injury or
death. Touching electrically ‘hot’ parts can cause fatal shocks and severe burns; While
welding, all metal components connected to the welder are electrically ‘hot’.
Keep your body and clothing dry. Never work in a damp area without adequate
insulation against electrical shock, stay on a dry duck board, or rubber mat when
dampness or sweat can not be avoided. Sweat, sea water or moisture between
the body and an electrically ’hot’ part or grounded metal reduces the body sur-
faces electrical resistance enabling dangerous and possibly lethal currents to flow
through the body.
Never
allow live metal parts to touch bare skin or any wet clothing, be sure weld-
ing gloves are dry.
Before welding, check for continuity; Be sure the earth clamp is connected to the
work-piece as close to the welding areas as possible. Grounds connected to
building frame work or other remote locations from the welding area reduce effi-
ciency and increase the potential electric shock hazard. Avoid the possibility of
the welding current passing through lifting chains, crane cables or other electric
paths.
During normal operation, the heat and sparks created during the welding process have
the potential to ignite flammable liquids, gases or other combustible material.
All inflammable materials must be removed from the area.
Have a suitable fire extinguisher available close by.
Causes of fire and explosion include; combustibles reached by the arc, flame, fly-
ing sparks, hot slag or heated material, misuse of compressed gases and cylin-
ders and short circuits.
Flying sparks or falling slag can pass through cracks along pipes, through win-
dows or doors and through walls or floor openings and out of sight of the opera-
tor; Sparks and slag can fly up-to 10 metres.
Keep equipment clean and operable; Free of oil, grease and of metallic particles
(in electrical parts) that can cause short circuits.
If combustibles are in the area.
Do not
weld , move the work if practical to an
area free of combustibles, avoid paint spray rooms, dip tanks, storage areas and