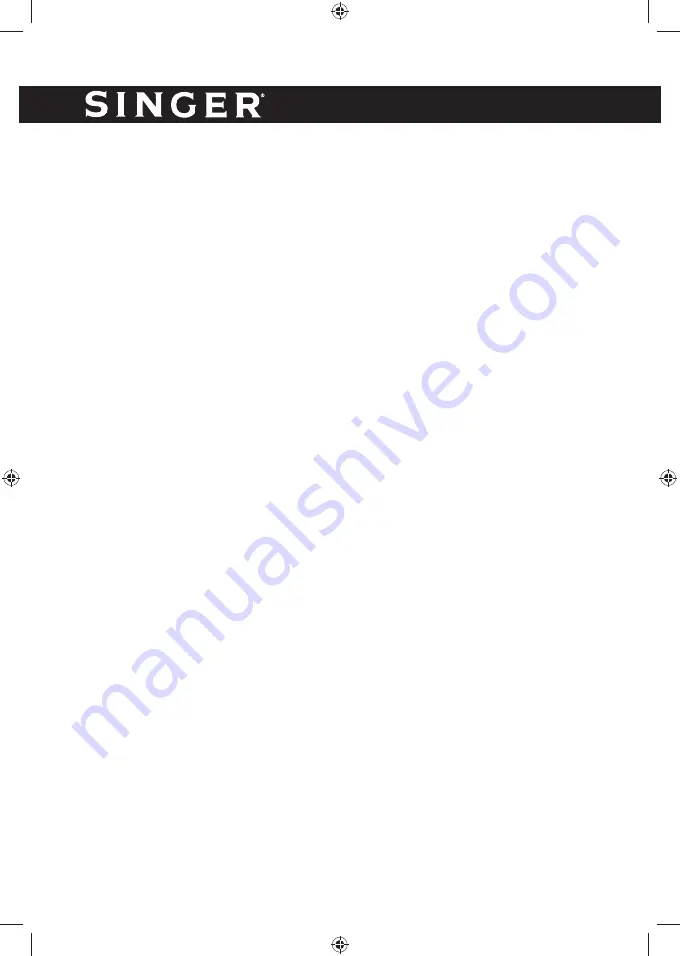
24
ENGLISH
ated solvents to prevent oxygen and refrigerant from reacting and corroding
the copper pipeline If leakage is suspected, all open
fl
ames should be re-
moved from the site or extinguished If a leak occurs where welding is required,
all refrigerant should be recovered, or the refrigerant should be completely
isolated away from the leak (using shut-off valves). Before welding and during
welding, use oxygen-free. Nitrogen (OFN) puri
fi
es the entire system.
15. Removal and evacuation
When performing maintenance or other operations on the refrigeration circuit,
conventional procedures shall be used. However, for
fl
ammable refrigerants it
is important that best practice is followed since
fl
ammability is a consideration.
The following procedure shall be adhered to:
• remove
refrigerant.
•
purge the circuit with inert gas.
• Evacuate
vacuum.
•
purge with inert gas.
•
open the circuit by cutting or brazing.
The refrigerant charge shall be recovered into the correct recovery cylinders.
For appliances containing
fl
ammable refrigerants the system shall be purged
with oxygen-free nitrogen to render the appliance safe for
fl
ammable refriger-
ants. This process may need to be repeated several times. Compressed air or
oxygen shall not be used for purging refrigerant systems.
For appliances containing
fl
ammable refrigerants, refrigerants purging shall be
achieved by breaking the vacuum in the system with oxygen-free nitrogen and
continuing to
fi
ll until the working pressure is achieved, then venting to atmos-
phere, and
fi
nally pulling down to a vacuum. This process shall be repeated
until no refrigerant is within the system. When the
fi
nal oxygen-free nitrogen
charge is used, the system shall be vented down to atmospheric pressure to
enable work to take place. This operation is absolutely vital if brazing opera-
tions on the pipe-work are to take place.
Ensure that the outlet for the vacuum pump is not close to any potential ignition
sources and that ventilation is available.
16. Charging procedures
In addition to conventional charging procedures, the following requirements
shall be followed.
•
Ensure that contamination of different refrigerants does not occur when
Summary of Contents for SDHM-10L SMART OUT
Page 1: ...SDHM 10L SMART OUT Dehumidifier GB INSTRUCTION MANUAL GR R290...
Page 2: ...GB ENGLISH 3 GR E 28...
Page 28: ...28 T R290 R290 ODP GWP R290 R290...
Page 29: ...29 R290 4 m2...
Page 30: ...30...
Page 31: ...31 SINGER...
Page 32: ...32...
Page 33: ...33 1 service 2 SINGER SINGER SINGER...
Page 34: ...34 3 Singer 4 24...
Page 36: ...36...
Page 37: ...37 3 50 50 70 70 POWER POWER SETTING 30 80 5 5 30 35 40 45 80 MODE MODE...
Page 38: ...38 1 55 RH 2 MODE 3 MODE 4 MODE...
Page 39: ...39 FAN FAN FAN TIMER X 0 24 Timer 1 24 24 1 Timer Timer 5 Timer Timer 5 Timer...
Page 40: ...40 CHILDLOCK LOCK 3 LOCK 3 AIR CLEAN SLEEPMODE Sleep Sleep Sleep...
Page 41: ...41 LED DISPLAY SETTING...
Page 42: ...42 5 20 18 5 25 18 23 120 12 18 25...
Page 43: ...43 5 12 20 1 2 3...
Page 44: ...44 1 2 3 Drying...
Page 45: ...45 SILVER 5 35...
Page 46: ...46 R290 0 236ohm 0 236 ohm...
Page 47: ...47 100m3 h...
Page 48: ...48 1 2 3 4...
Page 49: ...49 5 6 7 8...
Page 50: ...50 9...
Page 51: ...51 10 11...
Page 52: ...52 12 13 14 25 OFN...
Page 53: ...53 15 16...
Page 54: ...54 17 H...
Page 55: ...55 80 18 19...
Page 56: ...56...
Page 57: ...57 SSM EMC Directive 2014 30 EU LVC Low Voltage Directive 2014 35 EU ROHS Directive 2011 65 EU...
Page 58: ...58 NOTES...
Page 59: ...59 NOTES...