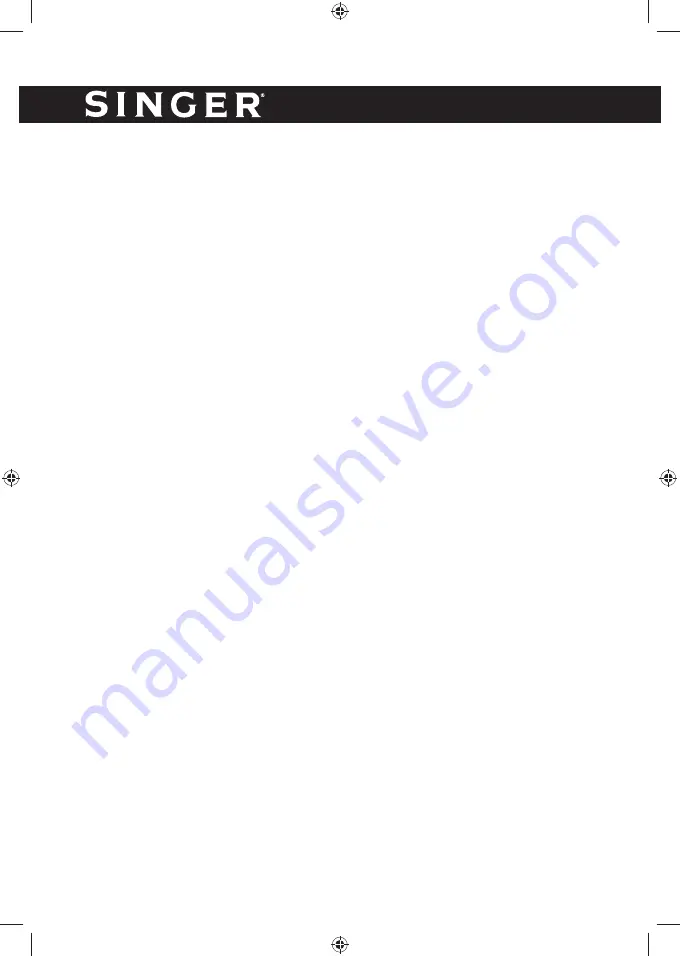
23
ENGLISH
11.Repair to intrinsically safe components
Do not apply any permanent inductive or capacitance loads to the circuit with-
out ensuring that this will not exceed the permissible voltage and current per-
mitted for the equipment in use.
Intrinsically safe components are the only types that can be worked on while
live in the presence of a
fl
ammable atmosphere. The test apparatus shall be
at the correct rating.
Replace components only with parts speci
fi
ed by the manufacturer. Other parts
may result in the ignition of refrigerant in the atmosphere from a leak.abling
Check that cabling will not be subject to wear, corrosion, excessive pressure,
vibration, sharp edges or any other adverse environmental effects. The check
shall also consider the effects of aging or continual vibration from sources such
as compressors or fans.
12. Cabling
Check that cabling will not be subject to wear, corrosion, excessive pressure,
vibration, sharp edges or any other adverse environmental effects. The check
shall also consider the effects of aging or continual vibration from sources such
as compressors or fans.
13. Detection of
fl
ammable refrigerants
Under no circumstances shall potentially sources of ignition be used in the
searching for or detection of refrigerant leaks. A halide torch (or any other de-
tector using a naked
fl
ame) shall not be used.
14. Leak detection method
For systems containing
fl
ammable refrigerants, the following methods for de-
tecting leaks are acceptable:
Electronic leak detectors can be used for the detection of
fl
ammable refrig-
erants, but the sensitivity may not be suf
fi
cient or may require recalibration
(the instrument calibration should be performed in a refrigerant-free environ-
ment) to ensure that the leak detector does not become a potential The ignition
source, and applies to the measured refrigerant, the leak detector should be
set to the lowest
fl
ammable concentration of the refrigerant (in percent), cali-
brated with the used refrigerant and adjusted to the appropriate gas concentra-
tion test range (max. 25%)
The leak detection
fl
uid is suitable for most refrigerants, but do not use oxygen-
Summary of Contents for SDHM-10L SMART OUT
Page 1: ...SDHM 10L SMART OUT Dehumidifier GB INSTRUCTION MANUAL GR R290...
Page 2: ...GB ENGLISH 3 GR E 28...
Page 28: ...28 T R290 R290 ODP GWP R290 R290...
Page 29: ...29 R290 4 m2...
Page 30: ...30...
Page 31: ...31 SINGER...
Page 32: ...32...
Page 33: ...33 1 service 2 SINGER SINGER SINGER...
Page 34: ...34 3 Singer 4 24...
Page 36: ...36...
Page 37: ...37 3 50 50 70 70 POWER POWER SETTING 30 80 5 5 30 35 40 45 80 MODE MODE...
Page 38: ...38 1 55 RH 2 MODE 3 MODE 4 MODE...
Page 39: ...39 FAN FAN FAN TIMER X 0 24 Timer 1 24 24 1 Timer Timer 5 Timer Timer 5 Timer...
Page 40: ...40 CHILDLOCK LOCK 3 LOCK 3 AIR CLEAN SLEEPMODE Sleep Sleep Sleep...
Page 41: ...41 LED DISPLAY SETTING...
Page 42: ...42 5 20 18 5 25 18 23 120 12 18 25...
Page 43: ...43 5 12 20 1 2 3...
Page 44: ...44 1 2 3 Drying...
Page 45: ...45 SILVER 5 35...
Page 46: ...46 R290 0 236ohm 0 236 ohm...
Page 47: ...47 100m3 h...
Page 48: ...48 1 2 3 4...
Page 49: ...49 5 6 7 8...
Page 50: ...50 9...
Page 51: ...51 10 11...
Page 52: ...52 12 13 14 25 OFN...
Page 53: ...53 15 16...
Page 54: ...54 17 H...
Page 55: ...55 80 18 19...
Page 56: ...56...
Page 57: ...57 SSM EMC Directive 2014 30 EU LVC Low Voltage Directive 2014 35 EU ROHS Directive 2011 65 EU...
Page 58: ...58 NOTES...
Page 59: ...59 NOTES...