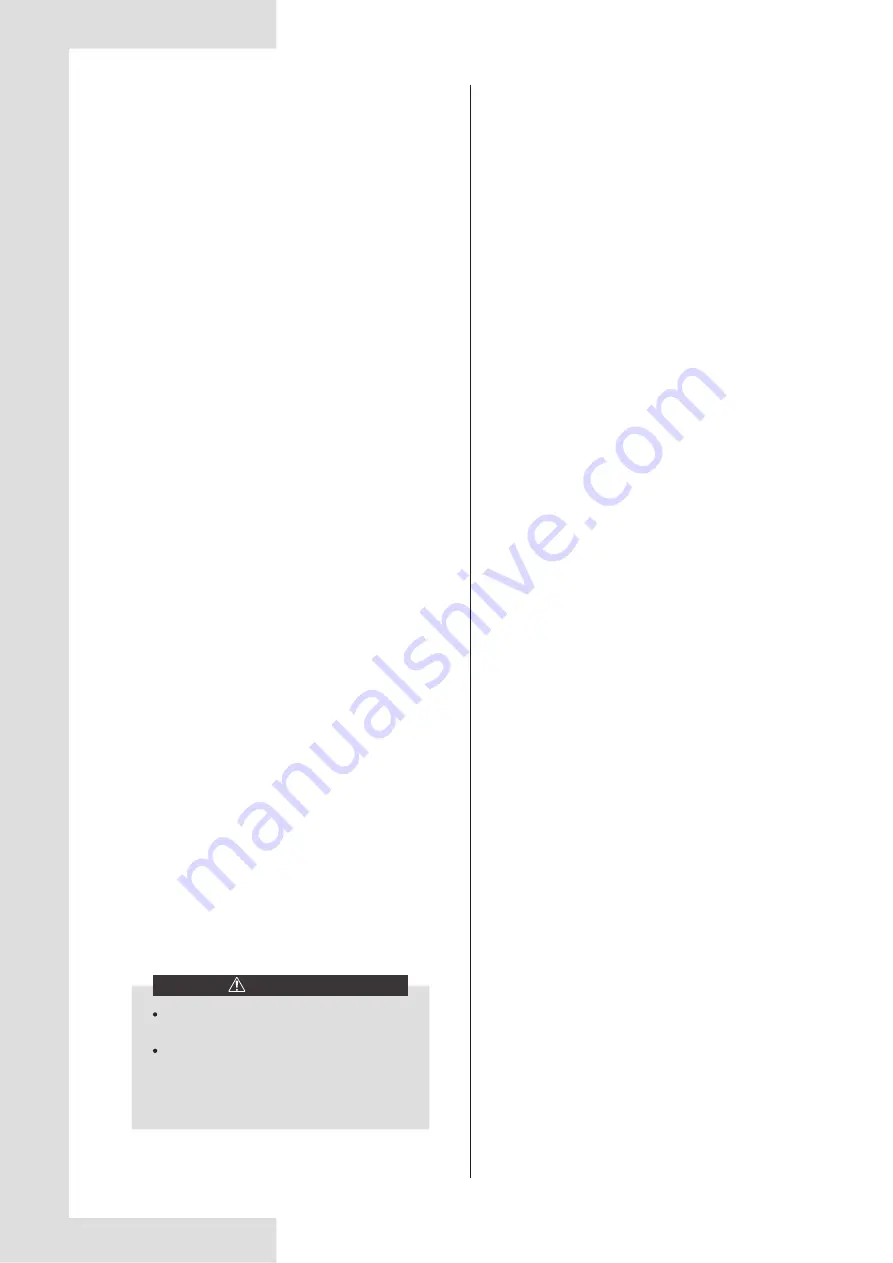
11.8 Refrigeration system
Determine whether refrigerant is needed by checking the
value of suction and discharge pressure and check
whether there is a leakage. Air tight test must be made if
there is a leakage or parts of refrigerating system is to be
replaced. Take different measures in the following two
different conditions from refrigerant injection.
1) Total leakage of refrigerant. In case of such situation,
leakage detection must be made on the pressurized
nitrogen used for the system. If repair welding is needed,
welding cannot be made until all the gas in the system is
discharged. Before injecting refrigerant, the whole
refrigeration system must be completely dry and of
vacuum pumping.
11.7 First startup after shutdown
1) If the unit that is shutdown for standby is placed in an
environment where the outdoor temperature is lower than
0°C, the water in the water system should be drained.
2) Water pipe may be frozen when the chilled water target
flow controller and anti-freezing temperature senor become
ineffective at running, therefore, the target flow controller
must be connected in accordance with the connection
diagram.
3) Frost crack may happen to water-side heat exchanger at
maintenance when refrigerant is injected to the unit or is
discharged for repair. Pipe freezing is likely to happen any
time when the pressure of refrigerant is below 0.4Mpa.
Therefore, the water in the heat exchanger must be kept
flowing or be thoroughly discharged.
11.11 System antifreezing
In case of freezing at the water-side heat exchanger interval
channel, severe damage may be caused, i.e. heat exchange
may be broken and appears leakage. This damage of frost
crack is not within the warranty scope, so attention must be
paid to antifreezing.
When the degree of vacuum is reached, inject refrigerant into
the refrigeration system with refrigerant bottle. Appropriate
amount of refrigerant for injection has been indicated on the
nameplate and the table of main technical parameters.
Refrigerant must be injected from the low pressure side of
system.
The injection amount of refrigerant will be affected by the
ambient temperature. If the required amount has not been
reached but no more injection can be done, make the chilled
water circulate and start up the unit for injection. Make the low
pressure switch temporarily short circuit if necessary.
Connect vacuum pumping pipe at the fluoride nozzle
at low-pressure side.
Remove air from the system pipe with vacuum pump.
The vacuum pumping lasts for above 3 hours.
Confirm that the indication pressure in dial gauge is
within the specified scope.
2) Refrigerant supplement. Connect refrigerant injection bottle on
the fluoride nozzle at low-pressure side and connect pressure
gauge at low pressure side.
11.9 Disassembling compressor
Follow the following procedures if compressor needs to be
disassembled:
1) Cut off the power supply of unit.
2) Remove power source connection wire of compressor.
3) Remove suction and discharge pipes of compressor.
4) Remove fastening screw of compressor.
5) Move the compressor.
11.10 Auxiliary electric heater
When the ambient temperature is lower than 2°C, the
heating efficiency decreases with the decline of the outdoor
temperature. In order to make the air-cooled heat pump
stably run in a relatively cold region and supplement some
heat lost due to de-frosting. When the lowest ambient
temperature in the user’s region in winter is within
0°C~10°C, the user may consider to use auxiliary electric
heater.
Please refer to relevant professionals for the power of
auxiliary electric heater.
Make chilled water circulate and start up unit, and make the low
pressure control switch short circuit if necessary.
Slowly inject refrigerant into the system and check suction and
discharge pressure.
Connection must be renewed after injection
is completed.
Never inject oxygen, acetylene or other
flammable or poisonous gas to the
refrigeration system at leakage detection and
air tight test. Only pressurized nitrogen or
refrigerant can be used.
CAUTION
The folowing preparations should be made for re-startup of unit
after long-time shutdown:
1) Thoroughly check and clean unit.
2) Clean water pipe system.
3) Check pump, control valve and other equipments of water pipe
system.
4) Fix connections of all wires.
5) It is a must to electrify the machine 12 hours before
starup.
33
Summary of Contents for SCV EB Series
Page 1: ...AIR COOLED CHILLER UNIT INSTALLATION AND USER MANUAL SCV XXX B AIR CONDITIONING...
Page 2: ...Original instructions...
Page 3: ......
Page 49: ......
Page 50: ...NOTE 44...
Page 51: ......
Page 52: ...0 1 234 56 0 7 8 234 0 9 1 7 1 0 6 16 3 5 9 4 260 88 4 260 88 08 88 688 0 4 08 4 6 4A8 60 B...