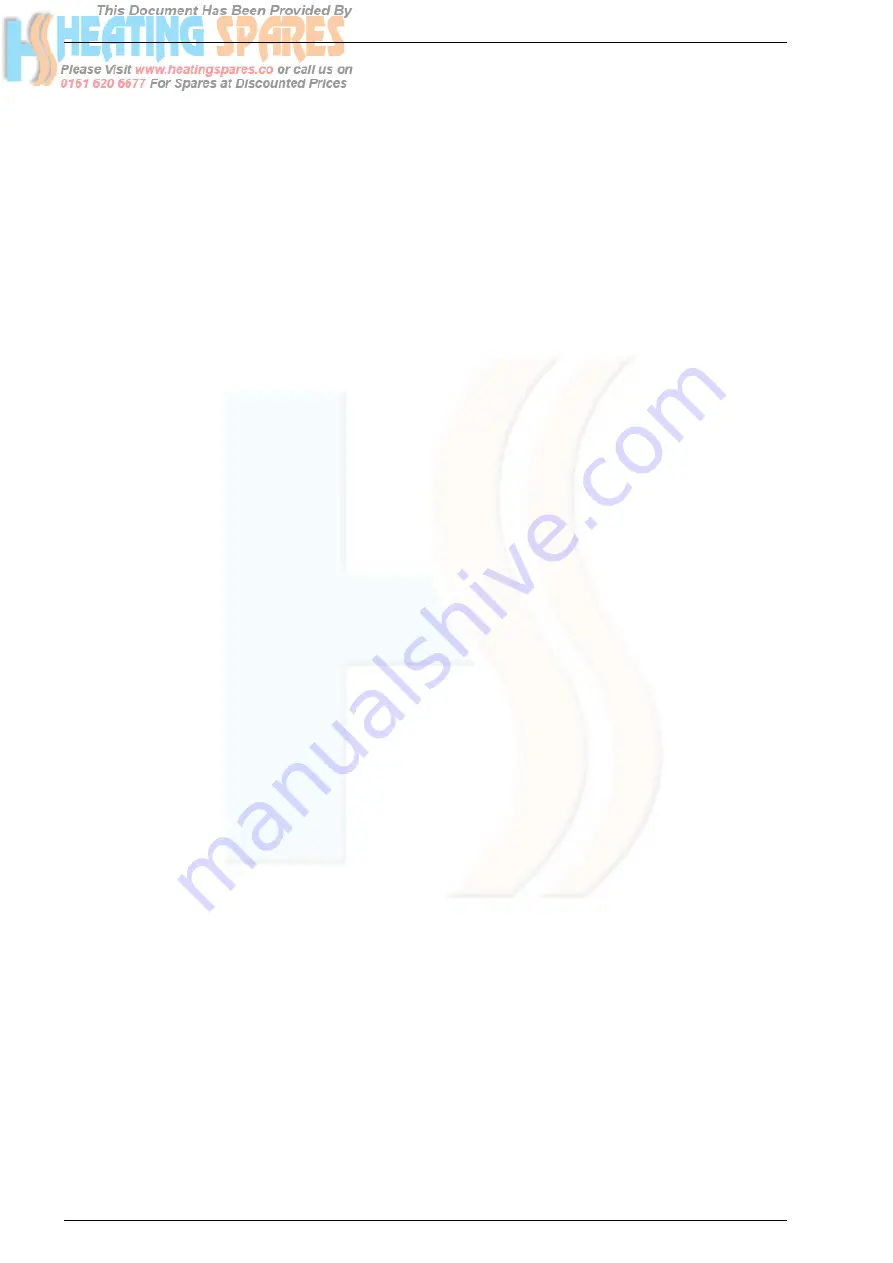
Supplied By www.heating spares.co Tel. 0161 620 6677
2.4
VENTILATION REQUIREMENTS
Detailed recommendations for air supply are given in
B55440: 2.
The following notes are for general guidance:
– It is not necessary to have a purpose provided air vent in
the room or compartment in which the appliance is in
installed.
2.5
GAS SUPPLY
– The gas inst allation should be in accordance with
BS6891. The gas required for the boiler is specified in
Table 4.
– Ensure that the pipework from the meter to the appliance
is of adequate size.
– The governor at the meter must give a constant outlet pres-
sure of 20 mbar (8 inwg) when the appliance is running.
– The gas supply line should be purged.
NOTE: Before purging open all doors and windows, also
extinguish any cigarettes, pipes, and any other naked
flames.
– The complete installation must be tested for gas soundness.
2.6
ELECTRICITY SUPPLY
The appliance MUST be earthed. A mains supply of 230V -
50 Hz single phase is required.
All external controls and wiring MUST be suitable for mains
voltage.
Wiring should he in 3-core PVC insulated cable NOT LESS
than 0.75 mm [24 x 0.2 mm] to BS6500, Table 16. Wiring
external to the boiler MUST be in accordance with current lEE
Wiring Regulations [B5 7671] and local regulations. The sup-
ply connection to the flying lead provided MUST be made to a
fused double pole switch, having a 3 mm [1/8 in] contact
separation in both poles, serving only the boiler and system
controls; the fuse rating should be 3 amp. This connection
should be readily accessible and be made adjacent to the boi-
ler. All fuses must be ASTA approved to BS 1362.
2.7
EXTERNAL CONTROLS AND COMPONENTS
The boiler is intended for use with a 230 V room thermostat.
The appliance requires a live feed from this to operate the
appliance and external circulating pump.
The pump MUST be wired to the appliance.
The connection is made to the terminal block as described in
section 3.7.1
2.8
WATER SYSTEMS
2.8.1 General
This appliance is designed for connection to the following
types of indirect domestic systems:
– Fully pumped, sealed central heating systems.
– Fully pumped, open vented central heating systems.
– Combined, gravity domestic hot water and pumped central
heating systems.
The domestic hot water cylinder must be of the indirect type
with a separate feed and vent pipes. Single feed cylinders
must not be used.
The pump, including isolation valves, should be fitted in the
heating flow pipe from the appliance.
The pump should provide suitable flow to maintain an 11°C
temperature rise between the pumped flow and return pipes
connected to the appliance. Details of the appliance pressure
drop are provided in Table 4.
System drain cocks should be fitted at the lowest points in the
system in order to provide adequate drain points. BS5442 pro-
vides information for the protection of the boiler due to freezing.
A frost thermostat should be fitted to the system controls.
2.8.2 Treatment of Water Circulating Systems
– All recirculatory systems will be subject to corrosion
unless an appropriate water treatment is applied. This
means that the efficiency of the system will deteriorate as
corrosion sludge accumulates within the system, risking
damage to pump and valves, boiler noise and circulation
problems.
– For optimum performance after installation this boiler
and its associated central heating system must be
flushed in accordance with the guidelines given in BS
7593 “Treatment of water in domestic hot water central
heating systems”.
– This must involve the use of a proprietary cleanser, such as
BetzDearborn Sentinel X300 or X400, or Fernox Superfloc.
Full instructions are supplied with the products, but for
immediate information please contact BetzDearborn (0151
420 9563) or Fernox (01799 550 811) directly.
– For long term protection against corrosion and scale,
after flushing it is recommended that an inhibitor such as
BetzDearborn Sentinel X100, or Fernox MB-1 or Copal is
dosed in accordance with the guidelines given in BS 7593.
Failure to flush and add inhibitor to the system may
invalidate the appliance warranty.
– It is important to check the inhibitor concentration after
installation, system modification and at every service in
accordance with the manufacturer’s instructions. (Test
kits are available from inhibitor stockists).
2.8.3 Requirements for open vented systems
A 22 mm copper vent pipe must be connected to the top of
the boiler flow pipe and terminate above the cold feed/expan-
sion tank. It must be suitably positioned to allow any dischar-
ge into the cold feed tank/expansion and must be on a conti-
nuous rise from the boiler flow pipe where it is connected.
The cold feed/expansion tank must have a capacity of at least
22 litres. The cold feed pipe from the cold feed/expansion
tank should be 15 mm copper.
The cold feed/expansion tank should have a lid. The bottom cold
feed/expansion tank must be no less than 1.2 m (one-point-two)
and no more than 30 m above the top of the appliance.
2.8.4 Requirements for sealed water systems
A sealed system must only be filled by a competent person
using one of the approved methods shown in fig. 4.
The system design should incorporate the connections appro-
5