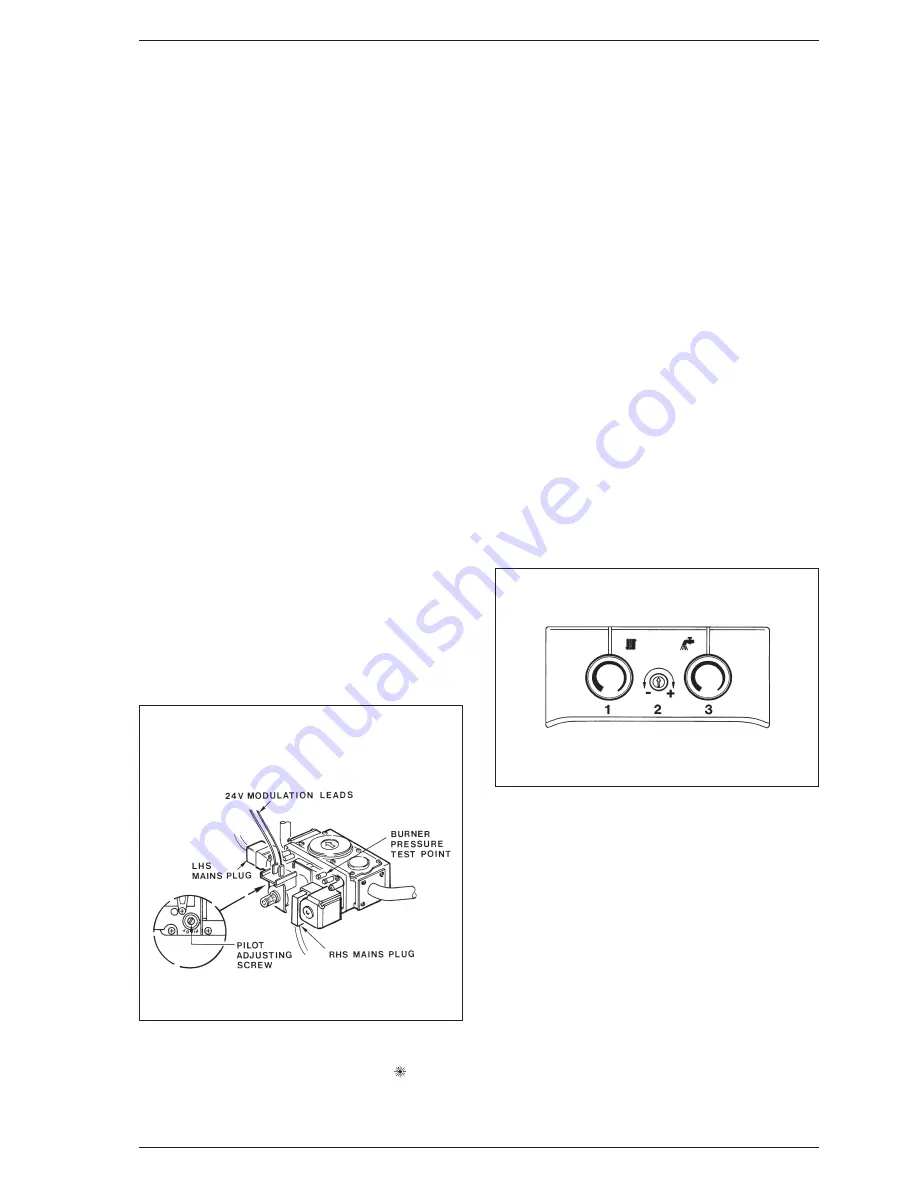
14
Before commissioning the appliance, the whole gas installa-
tion including the meter MUST be purged and tested for gas
soundness in accordance with BS6891: 1988.
IMPORTANT: open all doors and windows, extinguish
naked lights, and DO NOT SMOKE whilst purging the
gas line.
Before commencing the commissioning procedure,
ensure that the gas service cock is turned on, the elec-
tricity supply is isolated, and that the D.H.W. and C.H.
isolation valves are in the closed position.
4.1
FILLING THE WATER SYSTEM
– Open the C.H. flow and C.H. return valves (fig. 2).
– Loosen the automatic air vent cap (19 fig. 2) on the flow
pipe near the heat exchanger, and the manual vent
above the pump (15 fig. 2).
– Open all radiator valves and system air vents. Fill the
system with water using one of the approved methods
described in section 2.9 to about 0.5 bar greater than
the system design pressure. Close all air vents. Do not
forget the one near the pump!
– Check the system for water soundness.
– Completely drain the appliance and heating system,
thoroughly flush the system, and refill the system design
pressure.
– Open the D.H.W. inlet valve, open any hot tap, clear of
air bubbles. Close hot tap.
4.2
COMMISSIONING THE BOILER
– Remove the screw and connect a pressure gauge to the
burner pressure test point on the gas valve (fig. 16).
– Ensure that the Summer/Winter switch on the facia panel
(2 fig. 24) is set to the SUMMER position “
” (D.H.W.
Only), turn the D.H.W. thermostat (3 fig. 17) to maxi-
mum (fully clockwise), and turn on the electrical supply.
Fully open any D.H.W. tap and the burner will light.
– Allow the boiler to run for at least 2 minutes and check
that the burner pressure is as stated in section 1.3. The
D.H.W. burner pressure is factory set and should not
require adjusting. If the burner pressure is low, check
that the appliance has not begun to modulate (this will
occur if the D.H.W. flow rate is low. If modulation is
suspected, open all D.H.W. taps to maximise flow and
recheck burner pressure). If it is necessary to adjust the
D.H.W. burner pressure the method is described in sec-
tion 8.6.
– Reduce the D.H.W. draw off rate to the minimum neces-
sary to maintain the burner alight by carefully adjusting
the D.H.W. inlet valve and check that the burner pressu-
re decreases in response to D.H.W. temperature rise.
Fully open the inlet valve.
– Close the D.H.W. tap and ensure that the burner is
extinguished and the pump stops.
4.3
SETTING THE C.H. INPUT
– Turn the Summer/Winter switch (2 fig. 24) to the WIN-
TER position “
❄
" and turn the time clock override swit-
ch (24 fig. 24) to the override position “
●
”. Ensure that
the room thermostat (if fitted) is calling for heat. Turn
the C.H. thermostat knob (1 fig. 17) to maximum (fully
clockwise) and the burner will light.
– Allow the boiler to run for at least 2 minutes and check
the burner pressure. The heating input is factory set as
follows:
- 20.9 kW (71,300 Btu/h) for
“SUPER 90”
which is
required to give 15.8 kW (54,000 Btu/h) output;
- 20.6 kW (70,300 Btu/h) for
“SUPER 102”
which is
required to give 17.4 kW (59,400 Btu/h) output;
– If the heating output is to be adjusted, proceed as fol-
lows:
– refer to section 1.3 and establish the desired burner
pressure;
– remove the plastic cover protecting the potentiometer
(2 fig. 17);
– set the burner pressure as required using a small
screwdriver on potentiometer.
Rotate the screw anti-clockwise to reduce the burner
pressure;
– operate the Summer/Winter switch a few times and
check that the correct burner pressure is maintained.
– Replace the plastic cover over potentiometer.
4
COMMISSIONING AND TESTING
Fig. 16
SIT 827 NOVA
Fig. 17