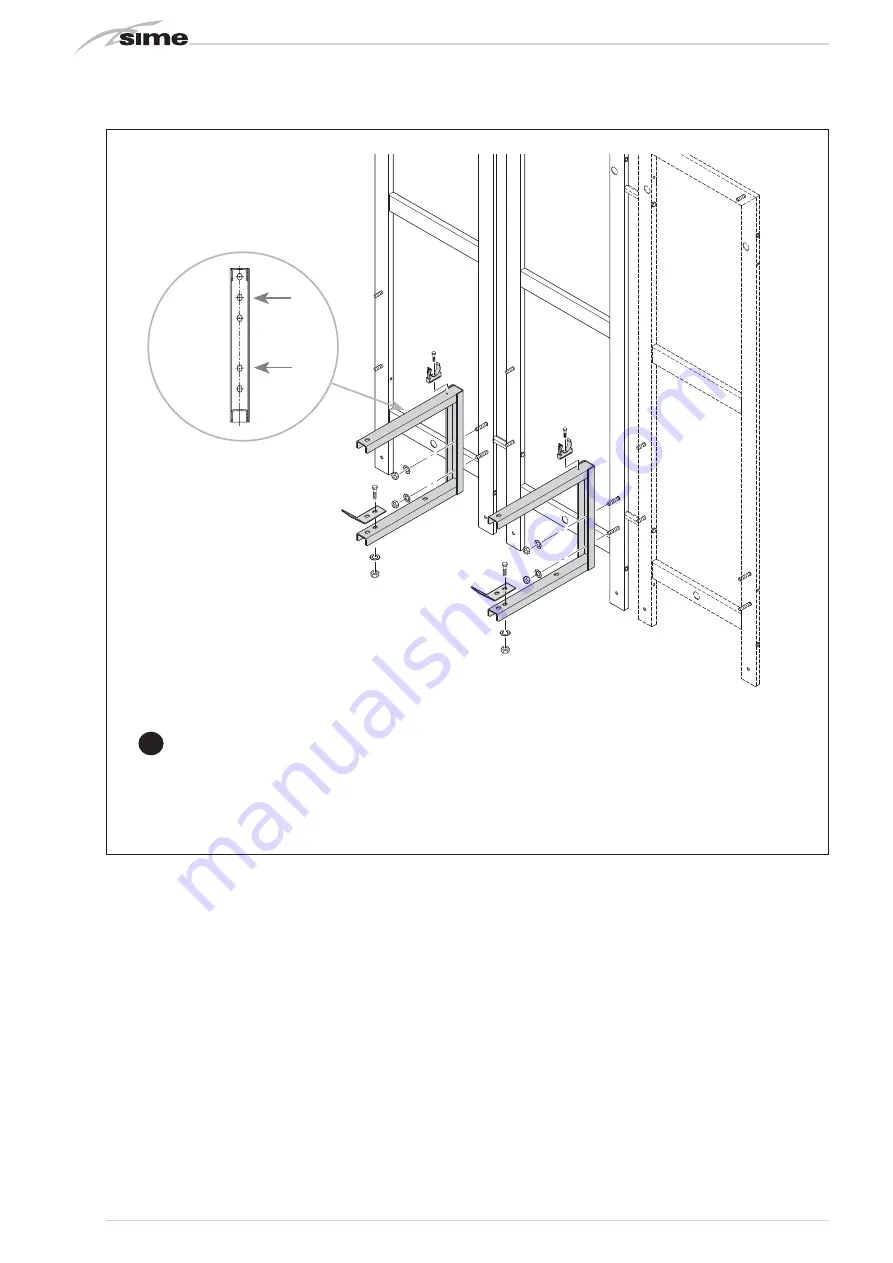
18
2
Mount the collector supporting brackets, fastening them to the frame using the
washers and M10 nuts.
The position where to place the washer and bracket blocking nut is indicated by
two arrows in correspondence with the frame studs to be used.
Mount the supports of the condensate drain collector, fastening them to the
supporting brackets, using the M5 screws.
Summary of Contents for MURELLE EQUIPE 220 ErP
Page 26: ...26 6 CASCADE MANAGEMENT 2 INSTALLER BUTTONS cd...
Page 43: ......