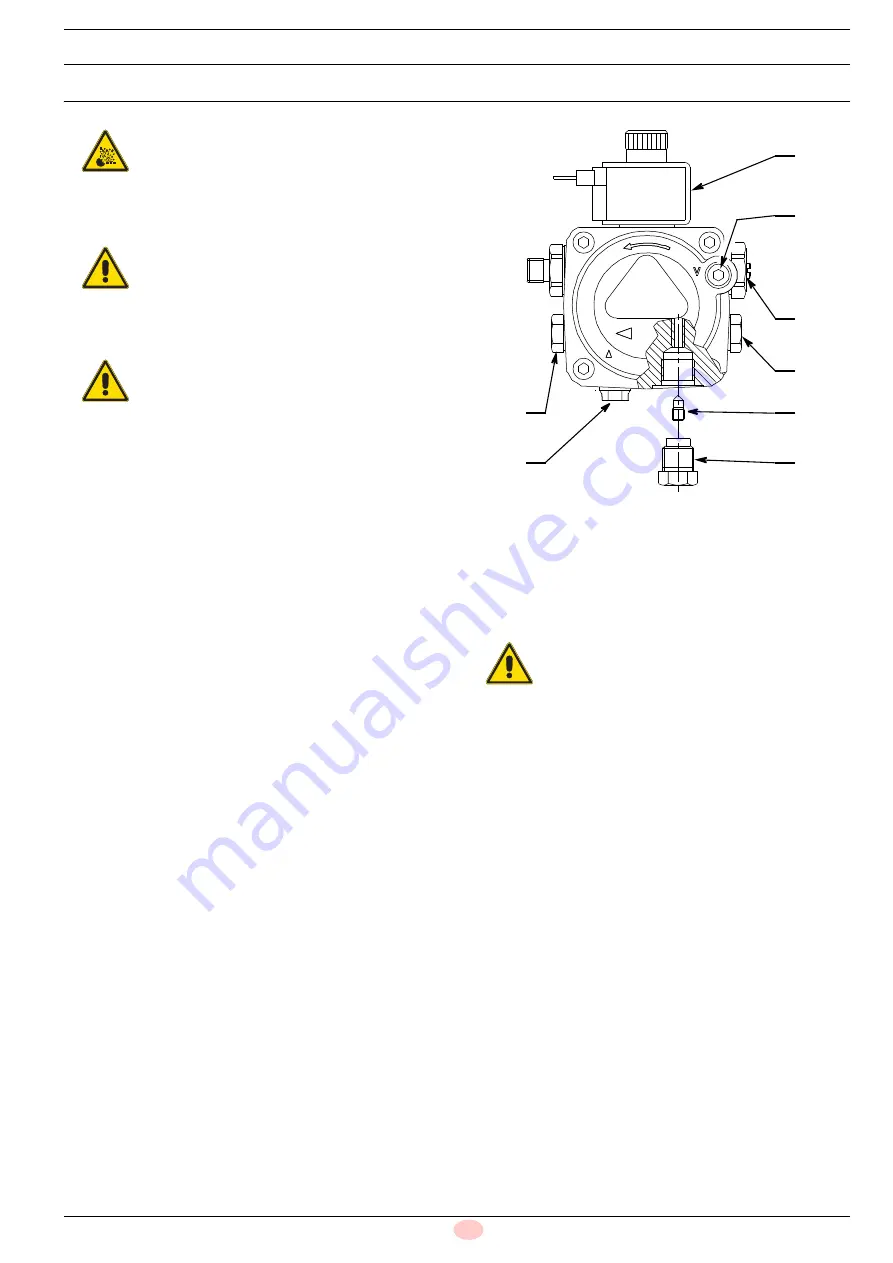
11
20119857
GB
Installation
5.7
Hydraulic systems
5.7.1
Pump
The pump is designed to allow working with two pipes.
In order to obtain one pipe working it is necessary to unscrew the
return plug 2)(Fig. 9), remove the by-pass screw 3) and then
screw again the plug 2).
Explosion danger due to fuel leaks in the pres-
ence of a flammable source.
Precautions: avoid knocking, attrition, sparks and
heat.
Make sure the fuel interception tap is closed be-
fore performing any operation on the burner.
WARNING
The fuel supply line must be installed by qualified
personnel, in compliance with current standards
and laws.
WARNING
Before starting the burner, make sure that the tank
return line is not clogged.
Obstructions in the line could cause the sealing
organ located on the pump shaft to break.
Gas oil suction line
2
Return line plug
3
By-pass screws
4
Manometer connection
5
Pressure adjuster
6
Vacumeter connection
7
Gas oil solenoid
8
Auxiliary pressure test
points
WARNING
Check periodically the flexible pipes conditions.
If necessary, install a filter on the fuel supply line.
Fig. 9
7
6
5
4
3
2
1
8
D9630
Summary of Contents for 20119424
Page 21: ......