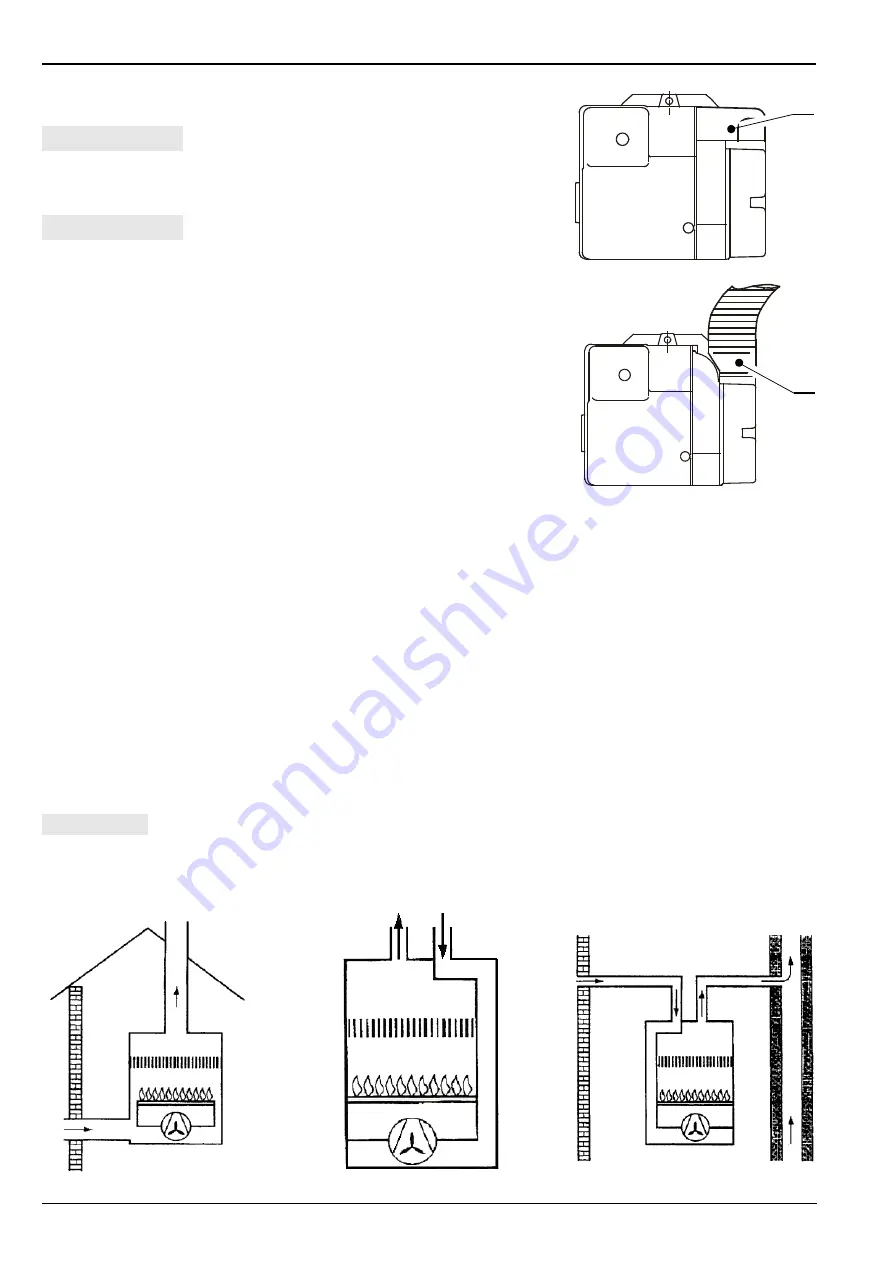
3126
4
3.2 BURNER ASSEMBLY
In case of
CF
applications, the burner shall not operate without pro-
tection
(A)
of the suction inlet.
FOR CORRECT BF APPLICATION, THE BURNER MUST BE
INSTALLED ON AN APPROPRIATE BF BOILER.
In case of
BF
applications an optional snorkel and gasket are availa-
ble replacing
(A)
with
(B)
. This item can be supplied separately.
The combustion air supply is through a flexible or rigid pipe connect-
ed to the air intake.
Consequently, you must comply with the following requirements and
instructions:
The combustion air intake tube must be:
- fastened securely to the burner;
- made of a suitable material, with temperature characteristics in
the range - 30 °C to 80 °C;
- in compliance with all requirements of applicable regulations in force in the country of destination.
The intake-tube / burner system must not allow a loss of over 2 m
3
/h at 0.5 mbar:
for instance, the above requirements will be met if you use flues for pressure exhaust of flue gases (the
condensation kind).
Make sure the air intake tube’s inlet is positioned so that it is not likely to be obstructed by foreign matter
and, where necessary, use suitable screens.
The temperature of the incoming air must not exceed 40 °C;
The inside diameter of the hose must be at least 80 mm.
The intake tube can be up to 6 metres in length.
Warning
: length is reduced if there are bends in the intake section.
For instance, using a tube with a smooth inside surface, you must allow for the following losses:
- for each 45° bend, tube length is reduced by 0.5 m;
- for each 90° bend, tube length is reduced by 0.8 m.
BURNER INSTALLATION MUST COMPLY WITH ONE OF THE INSTALLATIONS ILLUSTRATED IN THE
FIGURES BELOW.
Under no circumstances should the air’s entry in the hose intake area be obstructed.
The hose must not be blocked in any way or feature a shutting device (valves, membranes etc.).
Coaxial tubes must not be installed for any reason.
D5884
A
B
D5883
CF APPLICATION
BF APPLICATION
ATTENTION
S7851
S7853
S7876