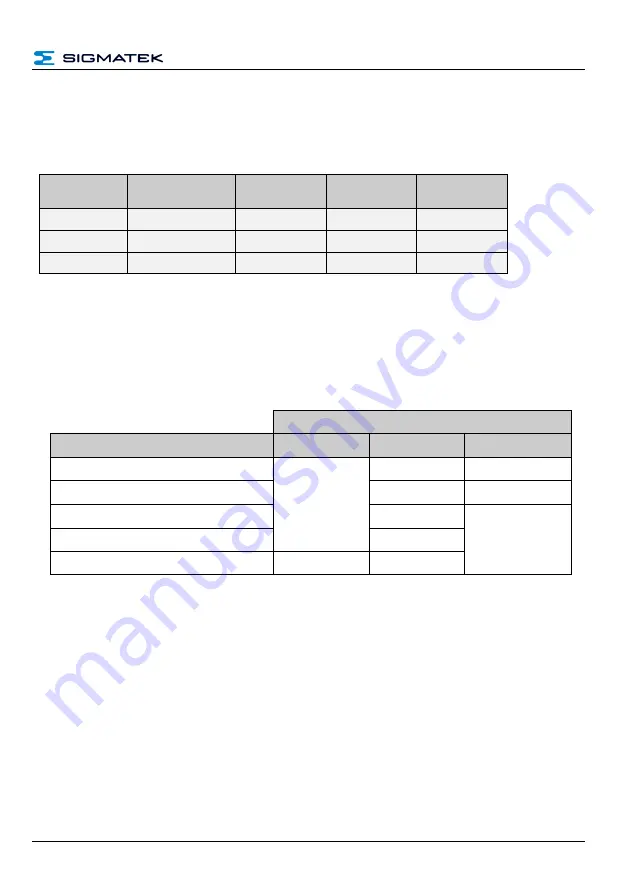
S-DIAS SAFETY CPU MODULE
SCP 111
04.11.2020
Page 27
6.2
Overview of Commands
The number of button presses corresponds to the number of light pulses in LED B during the
End sequence.
Commands
Number of button
presses
LED C1
LED C2
LED C3
QUIT_ERROR
1
X
CLR_CFG
2
X
X
SET_VERIFIED
3
X
X
X
6.3
Overview of Module Status and Commands
The following tables show a sample of the statuses in which the system can be found, the
commands that can be active during the respective status and their functions (see the Safety
System Handbook for the Module Status).
Command
System status
QUIT_ERROR
CLR_CFG
SET_VERIFIED
Check-Configuration
X
Time-restricted operational mode
X
X
Operational mode
X
Service mode
X
Error
X