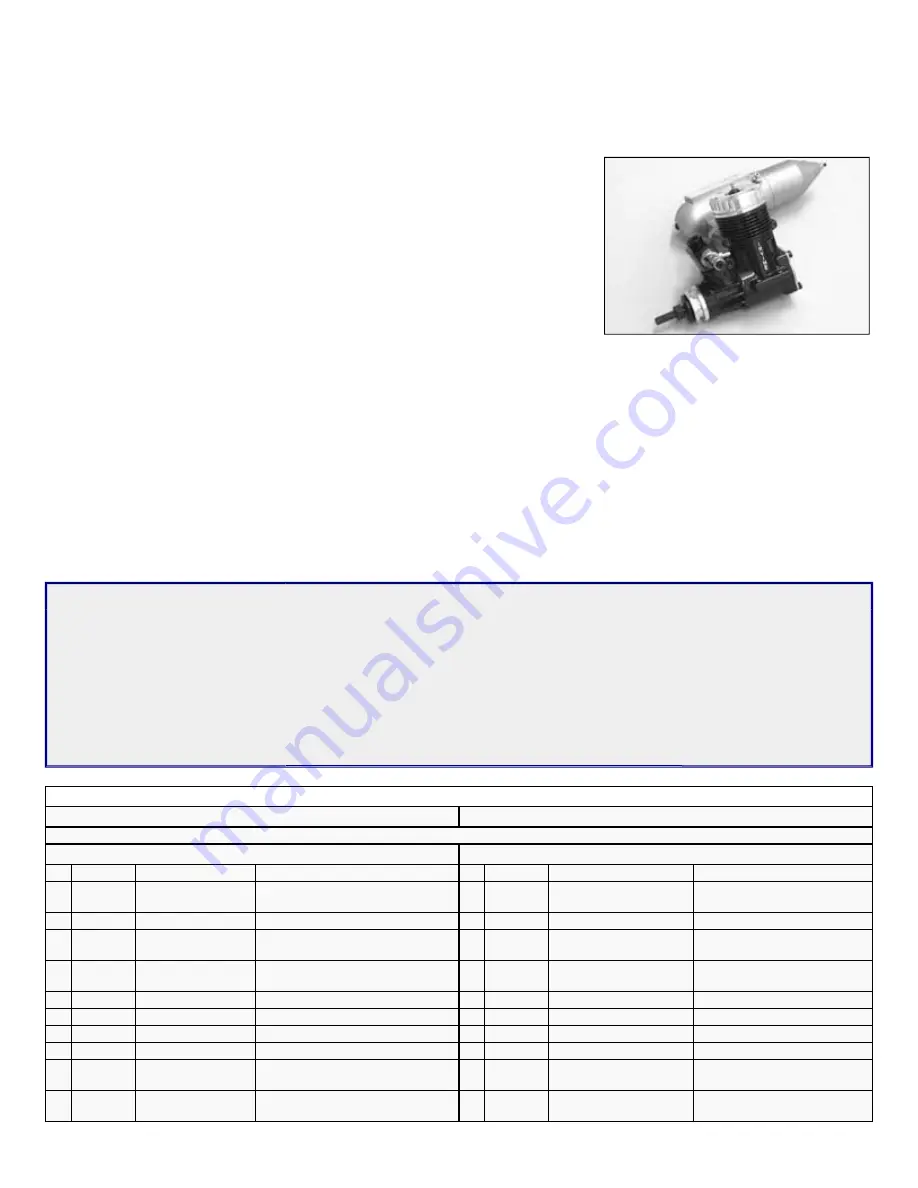
.
Engine Selection
Engine choices for the SEALANE are many. The SEALANE has been designed to produce excellent performance when using
the recommended engine sizes. Do not use an engine larger than recommended.
2-stroke engines are a perfect choice to power your SEALANE. Any plain-bearing or
bearing equipped .40 to .45 sport engine would be a good choice. For example, a
great choice would be the Irvine .40 engine. Like all Irvine engines, the .40 is
powerful, reliable, and quiet. Whatever engine you choose, take the time to carefully
break it in according to the manufacturer’s instructions. A good running, reliable
engine is a minimum requirement for the enjoyment of this or any R/C model aircraft.
The SEALANE can also use a variety of 4-stroke engines. Any 4-stroke engine in
the .40 - .50 displacement range should provide plenty of power. An important thing to
remember is that typical 4-stroke engines have their throttle arms usually located
differently than throttle arms on 2-stroke engines. If you want to power this model with
a 4-stroke engine, you will likely have to install a new, relocated throttle cable tube. While this is not difficult, it is something to
consider when choosing an engine.
Covering Material And Waterproofing
Your SEALANE has been designed to be completely covered with any of the popular plastic iron on covering materials on the
market. These covering materials are waterproof and by carefully overlapping the seams approximately 3/32", your SEALANE
will be almost waterproof.
The only place on the model where water can enter the fuselage is at the joint where the wing attaches. Our prototype models
were made with relatively tight fitting wings, with no additional sealing, and very little water was able to enter the fuselage.
Required Tools
A selection of glues:
A selection of hand tools, such as:
Sig Thin CA
Sig Medium CA
Sig thin CA applicator tips
Sig Kwik-Shot Accelerator
Sig Epoxy Glue (15 Minute
Working Time)
Regular size and miniature
screwdrivers
Regular size and miniature
pliers
Tweezers or small hemostats
Hobby knife with several new
#11 blades
Sandpaper-assorted grits
Sig Modelers “T” pins
Drill Motor
1/16” Drill Bit
3/16” Drill Bit
1/4” Drill Bit
Covering Iron
Wax Paper
Fuel Proof Paint
Small Paint Brush
Razor saw or
Hacksaw blade
Pencil
Small 90° Square
Masking tape and
Rubber bands
COMPLETE KIT PARTS LIST
Laser Cut Parts
There are 13 Laser Cut Sheets included in this kit. Use the illustrations on the following pages to identify these parts.
Wooden Parts
Qty Assembly Name
Size & Material
Qty Assembly Name
Size & Material
1
Fuselage
Fuse Nose Top
Stringer
1/4”x1/4”x13” Balsa Stick
2
Fuselage
Fuse Nose Top Sheet
3/32”x3”x13” Balsa Sheet
28
Fuselage
Fuse Bottom Sheet
3/32”x3”x3” Balsa Sheet
1
Fuselage
Windshield Top Block
1”x1”x4-1/2” Balsa Block
1
Fuselage
Nose Block
4”x2-3/4”x3” Balsa Block
1
Fuselage
Windshield Top Sheet
3/32”x1-3/4”x4-1/2” Balsa
Sheet
1
Fuselage
Fuse Aft Bottom
Block
1/4”x2-1/2”x6” Balsa Sheet
2
Fuselage
Bolt Block & Firewall
Reinf
1/4”x1/4”x7” Balsa Triangle
2
Fuselage
Servo Tray Support 1/4”x1/4”x5-1/4” Balsa Stick
1
Fuselage
Switch Wire Guide
1/4”x1/4”x1” Spruce Stick
4
Wing
Main Wing Spars
1/4”x1/4”x30” Spruce
2
Wing
Trailing Edges
1/4”x1/4”x30” Balsa Stick
4
Wing
Trailing Edge Sheet 3/32”x1”x30” Balsa Sheet
2
Wing
Leading Edges
3/8”x3/8”x27” Balsa Stick
2
Wing
Leading Edge Sheet 3/32”x3”x30” Balsa Sheet
2
Wing
Leading Edge Sheet
3/32”x3 1/8”x30” Balsa Sheet
8
Wing
Center Section
Sheet
3/32”x3”x12” Balsa Sheet
4
Wing
Cap Strip Material
3/32”x1/4”x36” Balsa Stick
2
Wing
Wing Tip
1-1/2”x1-1/2”x11-1/2” Balsa
Triangle
4
Wing
Tip Float Anchor
1/2”x15/16”x1.15” Hardwood
Summary of Contents for Sealane
Page 5: ... ...