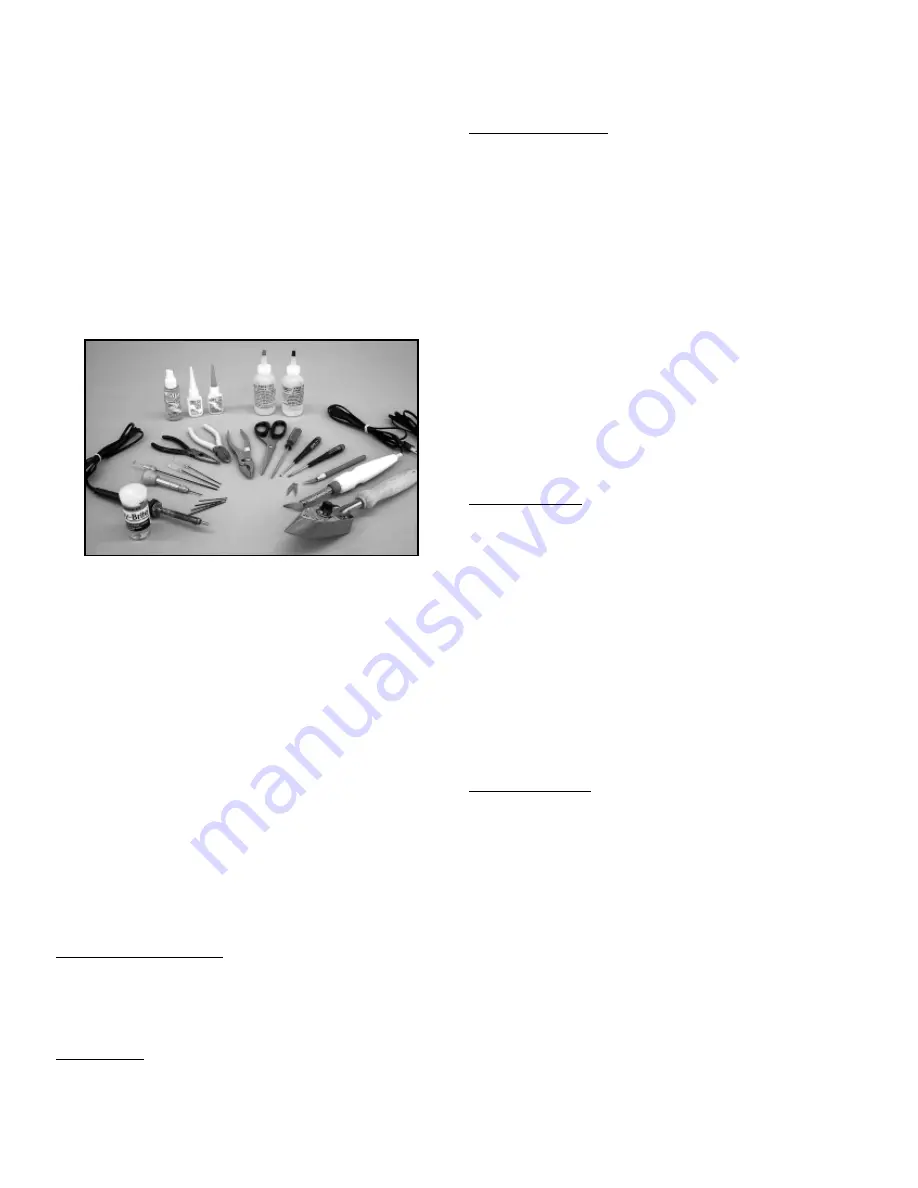
2
We suggest covering the iron’s shoe with a thin cotton cloth, such
as an old T-shirt, to prevent scratching the film. The iron should be
set to about 220
O
F - 250
O
F (104
O
C - 121
O
C). Use the heated
iron to lightly shrink the material - do not press on it. Then, lightly
iron the material back down to the wood. You can also use a
hobby-type heat gun to re-shrink the covering but you must be
careful around seams or color joints.
Re-heating seams may
cause them to “creep”, making them unsightly.
For part number reference, your FOUR-STAR 60 ARF was
covered in AeroKote
™
film with the following part numbers:
#SIGSTL311 Bright Red or #SIGSTL330 Bright Yellow.
REQUIRED TOOLS:
For proper assembly, we suggest you have the following tools and
materials available:
A selection of glues - SIG Thin and Thick CA and
SIG Kwik-Set 5-Minute Epoxy
Threadlock Compound, Such as Loctite
®
Non-Permanent Blue
Screwdriver Assortment
Pliers - Needle Nose & Flat Nose
Diagonal Wire Cutters
Small Allen Wrench Assortment
Pin Vise for Small Dia. Drill Bits
Hobby Knife With Sharp #11 Blades
Scissors
Heat Iron and Trim Seal Tool
Masking Tape
Paper Towels
Small Power Drill With Selection of Bits
Dremel
®
Tool With Selection of Sanding and Grinding Bits
A soldering iron and solder.
COMPLETE KIT PARTS LIST:
The following is a complete list of all parts contained in this kit.
Before beginning assembly, we suggest that you take the time to
inventory the parts in your kit.
BASIC AIRCRAFT PARTS:
❑
1 each
Fuselage
❑
1 each
Right & Left Wing Panel Set with Ailerons.
❑
1 each
Horizontal Stabilizer & Elevator Set.
❑
1 each
Vertical Fin & Rudder Set
WIRE PARTS:
❑
1 each
Formed Elevator Joiner Wire
❑
1 each
Formed Tailwheel Wire
❑
2 each
2-56 x 1 1/4” Threaded Rods; servo end of elevator
& rudder pushrods
❑
2 each
2-56 x 3 1/2” Threaded Rods; control surface end of
elevator & rudder pushrods
❑
2 each
4-40 x 8” Threaded Rods; aileron pushrods
METRIC HARDWARE:
❑
1 each
M2 x 20mm Phillips Head Screw; for tailwheel
installation
❑
2 each
M2 Flat Metal Washers; for tailwheel installation
❑
1 each
M2 Hex Nut; for tailwheel installation
❑
1 each
2mm I. D. Wheel Collar with set screw; for tailwheel
installation
❑
1 each
Allen "L" Wrench; for 2mm wheel collar
❑
3 each
M4 x 16mm Phillips Head Screws; for main landing
gear attachment
❑
4 each
M4 x 22mm Phillips Head Screws; for engine mount
attachment
❑
2 each
M4 x 30mm Phillips Head Screws; main wheel axles
❑
2 each
M4Hex Nuts; for axles
❑
6 each
M4Flat Metal Washers; (4) for engine mount
(2) for axles
❑
2 each
4mm I. D. Wheel Collars with set screws; for axles
❑
1 each Allen "L" Wrench; for 4mm wheel collars
❑
4 each
#2 x 8mm Phillips head washer style sheet metal
screws; for canopy
❑
4 each
Nylon "button" washers; for canopy
U.S. HARDWARE:
❑
2 each
1/4-20 x 1-1/2”Nylon Wing Bolts; for wing mounting
❑
1 each
2-56 x 3/4” Threaded Brass Coupler; for carb end of
throttle pushrod
❑
3 each
2-56 Nylon R/C Links; for elevator (1), rudder (1),
throttle (1)
❑
3 each
2-56 Solder R/C Links; for elevator (1), rudder (1),
throttle (1)
❑
1 each
Short, Right Nylon Control Horn; for aileron
❑
1 each
Short, Left Nylon Control Horn; for aileron
❑
1 each
Medium, Right Nylon Control Horn; for rudder
❑
1 each
Medium, Left Nylon Control Horn; for elevator
❑
8 each
#2 x 3/4” Sheet Metal Screws; for control horns
❑
2 each
4-40 Metal R/C Links; for aileron (2)
❑
2 each
4-40 Solder R/C Links; for aileron (2)
❑
2 each
4-40 Hex Nuts; for aileron (2)
MISCELLANEOUS:
❑
1 each
12mm Hardwood Front Wing Joiner
❑
1 each
6mm Plywood Rear Wing Joiner
❑
2 each
2mm Plywood Wing Hold-Down Plates
❑
1 each
3mm Plywood Aileron Positioning Guide
❑
1 each
3mm Formed Aluminum Main Landing Gear
❑
1 each
Molded Clear Plastic Canopy
❑
1 set
4pc. Adjustable Engine Mounts, 60-size
❑
22 each CA Hinges; for ailerons (12), elevator (6), rudder (4)
❑
2 each
8.5cm dia. (approx. 3.35”) Main Wheels
❑
1 each
30mm dia. (approx. 1.17”) Tailwheel
❑
1 each
Formed Metal Tailwheel Strap
❑
1 each
2-1/2” dia. Spinner assembly
❑
1 each
10mm sq. X 94mm Balsa; Fuel Tank Retainer
❑
2 each
1cm x 8cm x 20cm Foam Rubber; for radio packing
❑
1 each
2mm x 3.15mm x 26cm Plastic Throttle Pushrod
Tube
❑
1 each
380cc (12.8 oz.) Plastic Fuel Tank with Hardware
❑
1 each
.065" O. D. x 18" Stranded Steel Cable - for throttle
pushrod
Summary of Contents for FOUR-STAR 60
Page 18: ...18 R ...