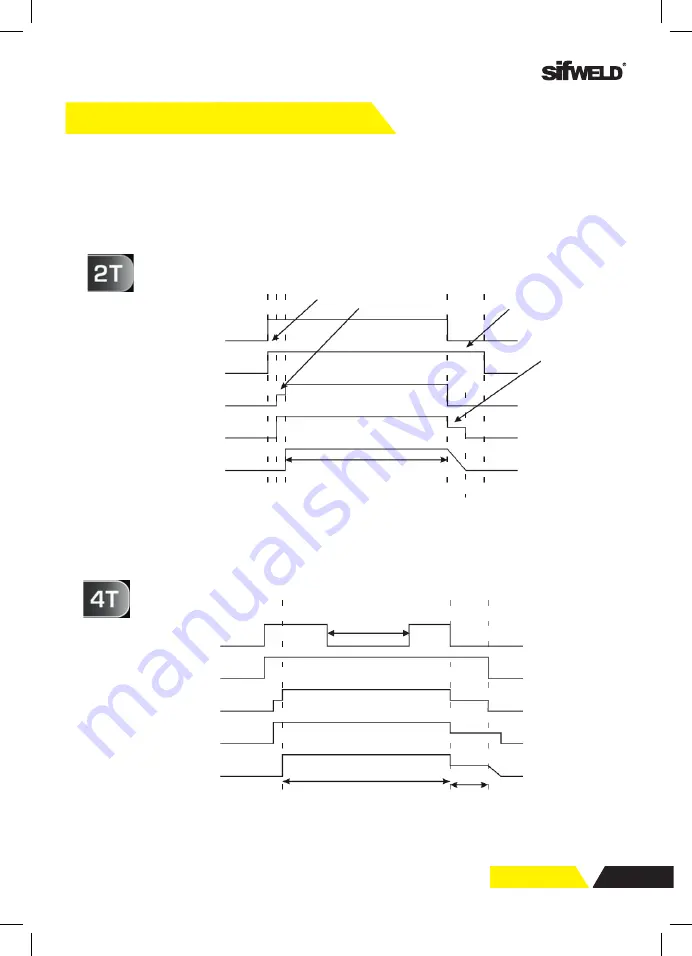
13
2.2 Further Controls Explained
TRIGGER MODE DISPLAY
•
When 2T operation is selected, pressing trigger starts air, touch and lift arc to start.
Release trigger to stop air and arc.
PANEL FUNCTIONS & DESCRIPTIONS
10
Further Controls Explained
Trigger mode display (2)
⚫
When 2T operation is selected, pressing trigger starts gas, touch and lift arc to start.
Release trigger to stop gas and arc.
⚫
When 4T operation is selected, press and release trigger to start gas, touch and lift
arc to start. Press and release trigger again to stop gas and arc.
Pre Gas Time
Slow Feed Time
Post Gas Time
Welding conditions
Gun Switch
Gas Supply
Wire Feed
Output Voltage
Output Current
Burn back Time
2T mode (ON/OFF)
Welding conditions
Gun Switch
Gas Supply
Wire Feed
Output Voltage
Output Current
End Current conditions
Self-Locking Function
4T mode (Latching)
•
When 4T operation is selected, press and release trigger to start air, touch and lift arc to start.
Press and release trigger again to stop air and arc.
PANEL FUNCTIONS & DESCRIPTIONS
10
Further Controls Explained
Trigger mode display (2)
⚫
When 2T operation is selected, pressing trigger starts gas, touch and lift arc to start.
Release trigger to stop gas and arc.
⚫
When 4T operation is selected, press and release trigger to start gas, touch and lift
arc to start. Press and release trigger again to stop gas and arc.
Pre Gas Time
Slow Feed Time
Post Gas Time
Welding conditions
Gun Switch
Gas Supply
Wire Feed
Output Voltage
Output Current
Burn back Time
2T mode (ON/OFF)
Welding conditions
Gun Switch
Gas Supply
Wire Feed
Output Voltage
Output Current
End Current conditions
Self-Locking Function
4T mode (Latching)