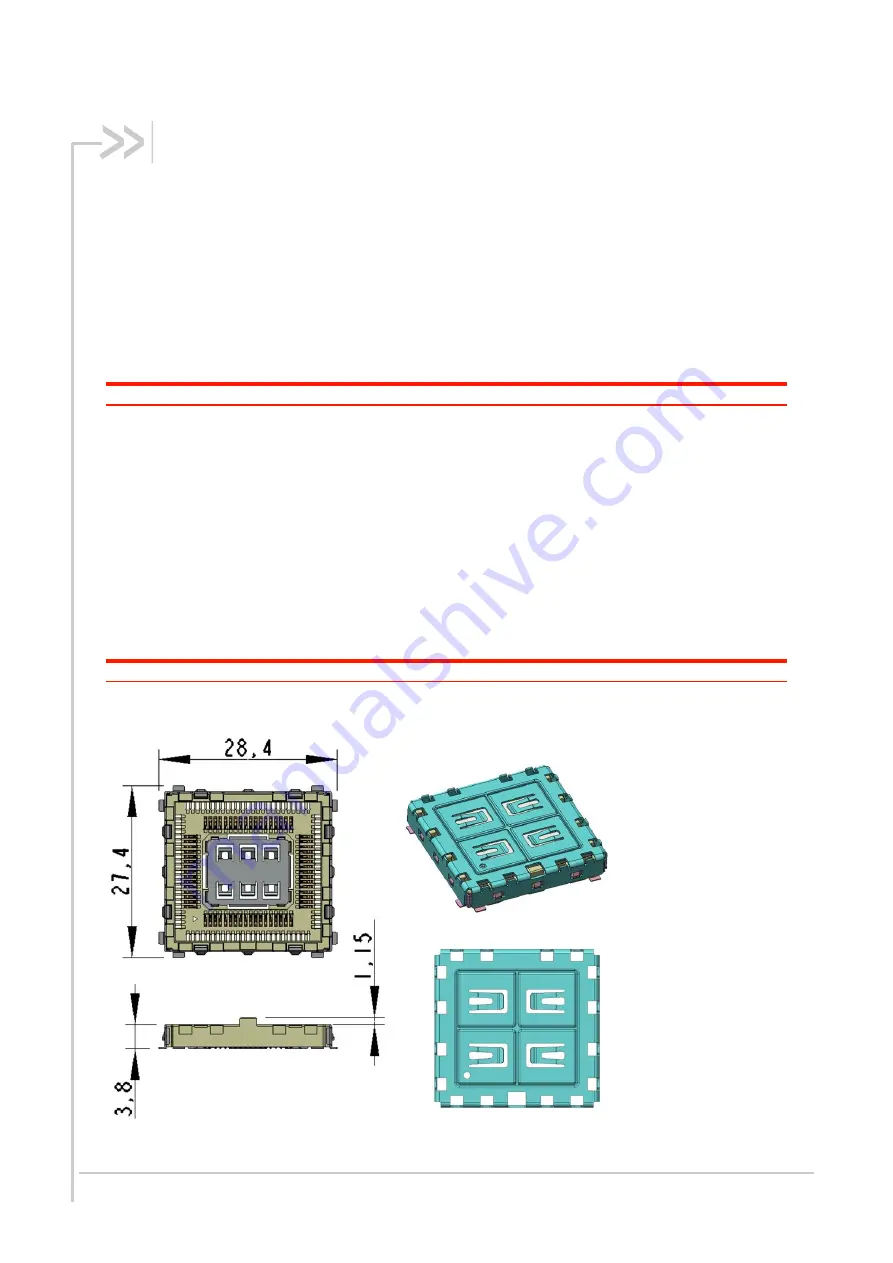
4115102
Rev 1.1
February 21, 2014
12
3. Handling
3.1.
Storage of the AirPrime Snap-in Socket
3.1.1.
Storage Condition
AirPrime Snap-in socket can be stored in their original packages, over the course of up to 1 year.
They can withstand a storage temperature range between -40°C to +85°C, nevertheless when packed
into T&R the upper storage temperature is decreased to +40°C due to T&R packaging material.
Tip:
For optimal results, the recommended storage temperature is +20°C +/- 10 degrees.
3.2.
Component Package
3.2.1.
Package Description
The AirPrime Snap-in socket is a scalable QFP 27.4x28.4 mm, pitch 0.8 mm.
Height with the cover assembled: 4.9 ±0.2 mm.
Number of contacts: 66 Pins
Weight: Snap-in socket with cover 2.5 mm: 4.7 g (TBC)
Note:
The AirPrime Snap-in socket if for use with the AirPrime HL Series modules.
For additional information, refer to the product technical specifications listed in section 1.2 Reference
Documents.
Figure 3.
AirPrime Snap-in Socket