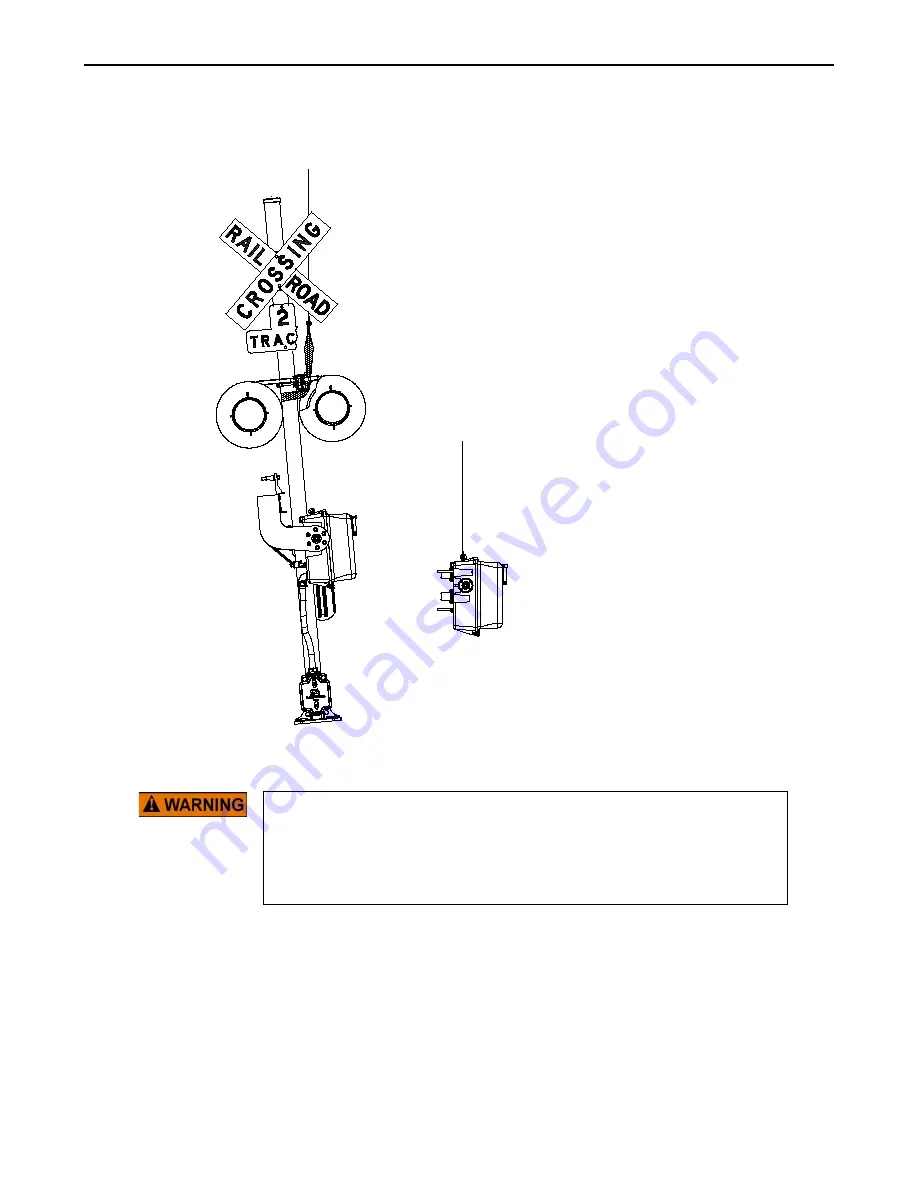
ENTRANCE GATE INSTALLATION AND SETUP
4-3
SIG-QG-21-01
NOVEMBER 2021
Version: A
Figure 4-1
Lifting Gate Assembly Recommendation
WARNING
DO NOT LIFT COMPLETE GATE ASSEMBLY WITH LIFTING EYE
IN TOP OF MECHANISM HOUSING. DOING SO MAY RESULT IN
PERSONAL INJURY AND/OR DAMAGE TO THE MECHANISM.
3.
Clamp the mechanism in place.
Lift the mechanism and set it on top of the support clamp.
Secure the mechanism to the mast with the four, square head machine bolts, two saddles, nuts
and washers. Use a 1-1/8” wrench or socket to tighten the nuts to a torque range of
95 to 105 ft-lbs.
MECHANISM ONLY CAN BE
LIFTED INTO PLACE USING
THE LIFTING EYE PROVIDED
RECOMMENDATIONS FOR LIFTING
PRE-ASSEMBLED SIGNALS WITH
GATE MECHANISM.
1. SIGNAL ASSEMBLY MUST BE
WITHOUT ARM AND COUNTERWEIGHTS
2. LIFT POINT SHOULD BE A
MINIMUM OF 15" ABOVE GATE
MECHANISM.
3. LIFTING SLING CAN BE USED
AROUND MAST AND UNDER THE
JUNCTION BOX CROSSARM FOR
LIGHTS AS SHOWN
WEIGHT = 209 Lbs.
WEIGHT (AS SHOWN) = 560 Lbs.
Weight (as shown) = 461 lbs.
Weight = 110 lbs.
Recommendations for lifting pre-assembled
signals with gate mechanism:
1) Signal assembly must be without arm and
counterweights.
2) Lift point should be a minimum of 15” above gate
mechanism.
3) Lifting sling can be used around mast and under
the junction box crossarm for lights as shown.
Mechanism can only be
lifted into place using the
lifting eye provided.