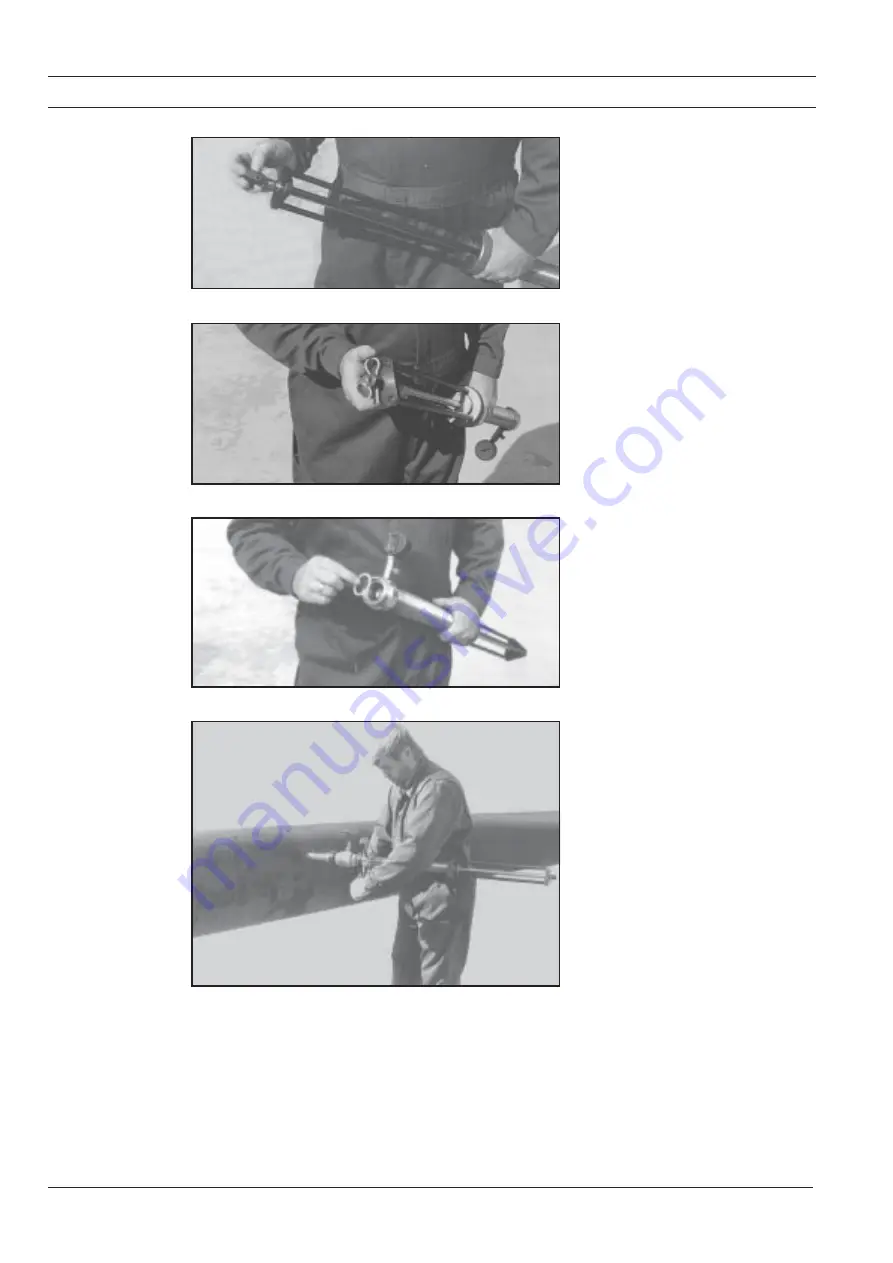
SFIDK.PS.029.Y1.02
14
SITRANS F US SONOFLO
Mount the hex screw nut in the end of the
mandrel.
Mount the spring clip through the nut and
mandrel.
Make sure that the gasket is mounted
and not damaged.
Mount the lock tool on the ball valve. It is
essential that both lock tool and ball
valve have been thoroughly tightened
by means of the hook spanners.