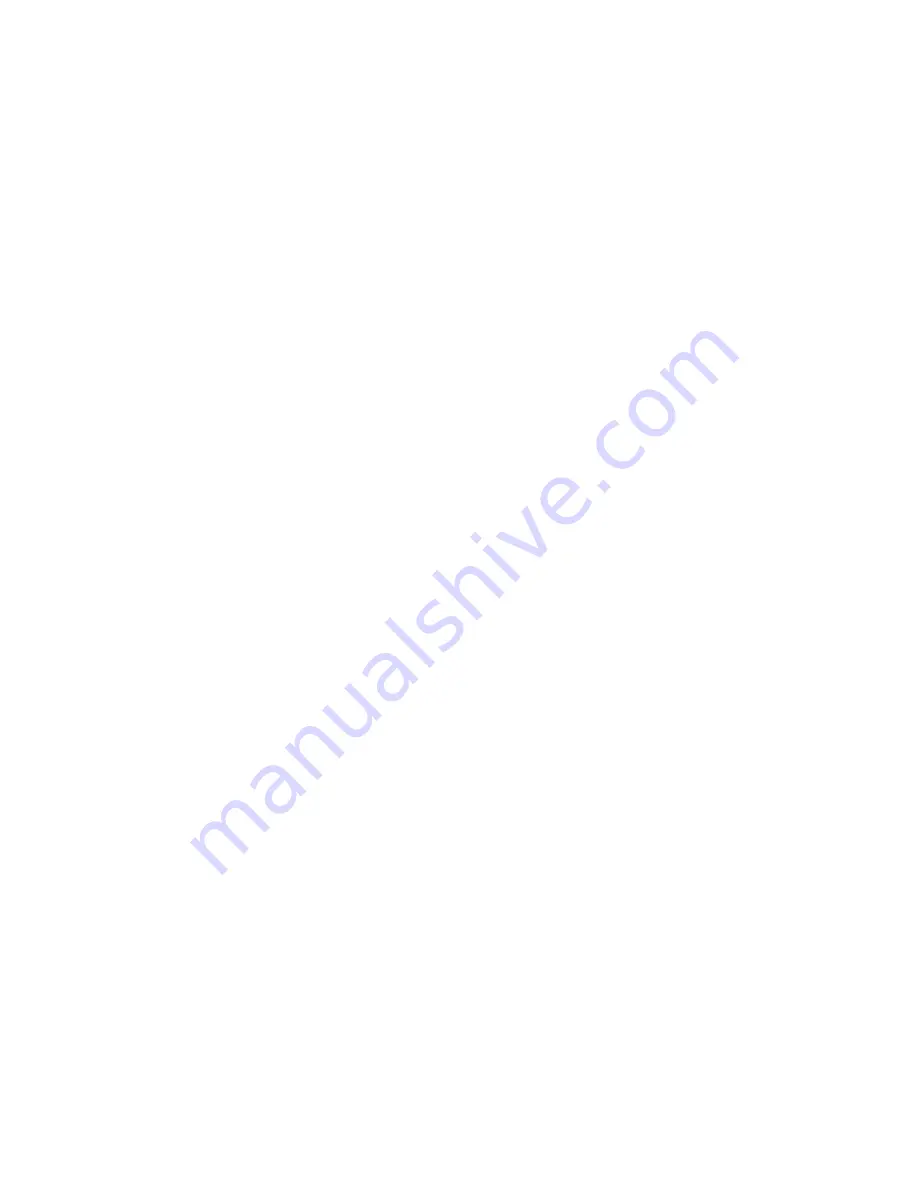
Functional safety for SIPART PS2 FF
A5E00489774-02, 10/2013
23
4.
Set the setpoint to 50% using a local operation (manual operation) or bus communication.
5.
Reduce the intake pressure (P
z
) to a third of the maximum supply pressure.
6.
Verify that the valve returns to the safety position.
7.
Check the filters in the pneumatic connections for contamination and clean them if necessary.
2.5
Safety-related characteristics
The safety characteristics necessary for use of the system are listed in the SIL declaration of conformity. These values apply
under the following conditions:
●
The positioner is only used in applications with low demand rate for the "Low demand mode".
●
"Jumper" on the basic electronic system was plugged into the left position facing the terminals at position "Shut Down
enabled" or removed completely.
●
The positioner is blocked against unwanted and unauthorized changes/operation.
●
The shut-off signal for the positioner is generated at the input for the safety shutdown (terminals 81 and 82) by a safe
system which meets at least SIL 2. The LOW level has a maximum of 4.5 V at the input terminals.
●
The connected actuator must be singe-acting and return the valve to the safe end position by spring force in the following
scenario:
–
At a chamber pressure (Y1 connection) up to a third of the maximum available intake pressure (P
z
connection)
●
The air outlet does not contain any additional cross-sectional contractions leading to an increased dynamic pressure. In
particular, a silencer is only allowed if icing or other contamination is ruled out.
●
The restrictor in the Y1 circuit may not be completely closed during operation.
●
The auxiliary pneumatic power is free of oil, water and dirt in line with:
DIN/ISO 8573-1, maximum class 2
●
The average temperature viewed over a long period is 40 °C.
●
Fault rates are calculated on the basis of a mean time to repair (MTTR) of 8 hours.
●
In case of a fault, the pneumatic outlet of the positioner is depressurized. A spring in the pneumatic actuator must move
the valve to the pre-defined, safe end position.
●
A dangerous failure of the positioner is when the pressure outlet is not depressurized, or the safety position is not
reached, with a LOW level of maximum 4.5 V at the input for the safety shutdown.
C
Appendix
C.1
Meaning of the SIPART PS2 FF diagnostics values
Convention
The parameter names in the following descriptions comprise two components. The name of the parameter comes first. This
is followed by the name of the corresponding communication object in square parentheses.
Communication objects whose names commence with "RB" are assigned to the resource block. The other communication
objects belong to the transducer block.
0 - device descriptor
Communication object: [RB.DESCRIPTOR]
The content of the resource block parameter "DESCRIPTOR" is a visible 32-byte string. The string is output in the bottom
display line.
Use this parameter to display the device descriptor. If the displayed string has more than five characters, it is possible to
scroll using the increment or decrement button.