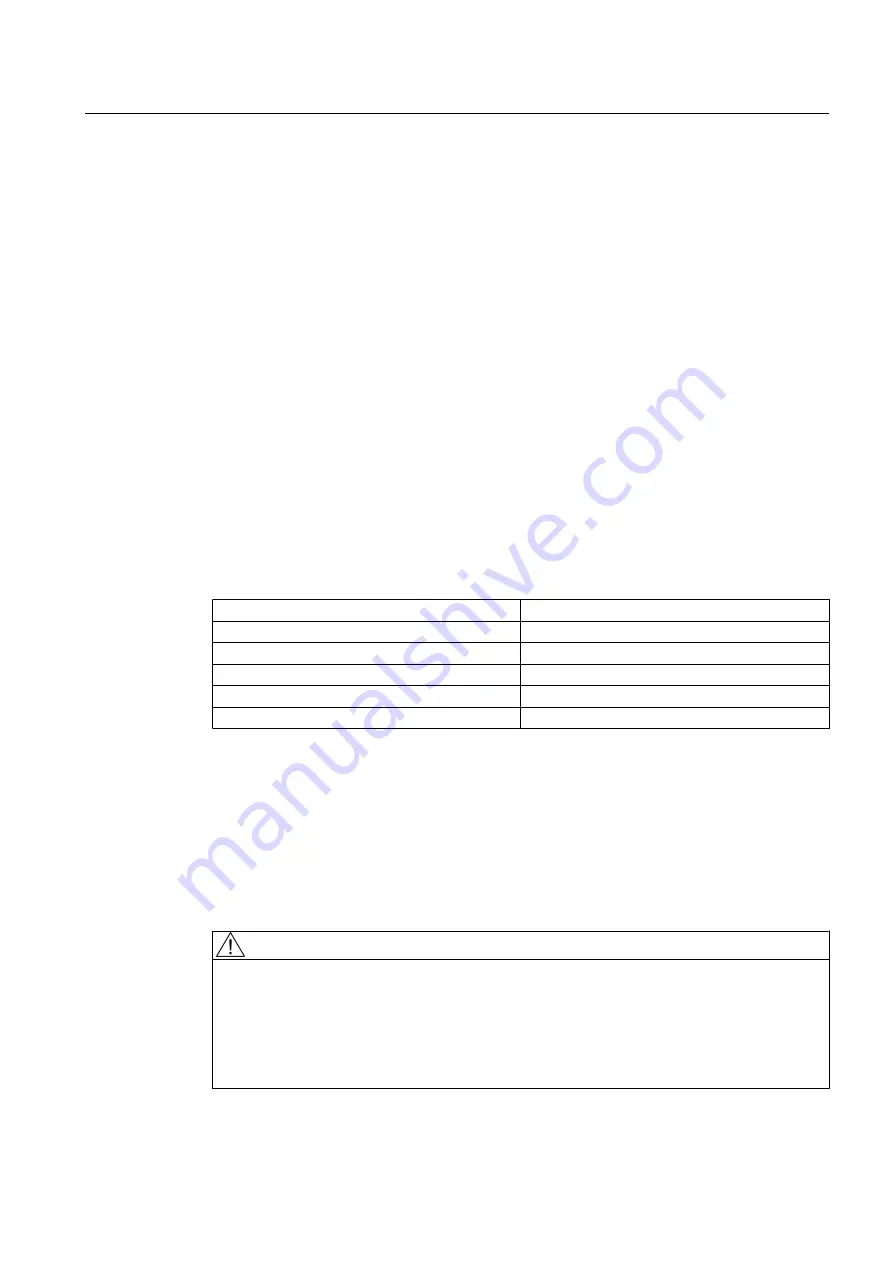
1. Unscrew the cable entry plate.
2. Drill the required number of holes or threads in the required size into the cable entry plate.
The thickness of the plate is selected in such a way as to give a sufficient number of turns
when the holes are tapped.
Please note that you are responsible for ensuring that the entry plate still has sufficient
strength after the holes have been drilled and tapped.
3. Mount the cable entry plate and the cables with the cable glands onto the terminal box.
After the cables have been inserted into the terminal box, tighten the cable glands and parts
for strain relief to the torque specified by the manufacturer.
4. Seal the screwed sockets on the cable glands in accordance with the degree of protection.
Use only sealing plugs, cable entries and conductor entries, that are certified and marked for
use in the respective hazardous area (the zone).
6.2.8
Minimum air clearances
After proper installation, verify that the minimum air clearances between non-insulated parts
are maintained. Be aware of any protruding wire ends.
Table 6-3
Minimum air clearance dependent on rms value of the alternating voltage U
rms
Rms value of the alternating voltage V
rms
Minimum air clearance
≤ 500 V
8 mm
≤ 630 V
10 mm
≤ 800 V
12 mm
≤ 1000 V
14 mm
≤ 1250 V
18 mm
Values apply at an installation altitude of up to 2000 m.
When determining the required minimum air clearance, the voltage value in the table may be increased
by a factor of 1.1, so that the rated input voltage range is taken into account during general use.
6.2.9
Cable ends with wire end sleeves
Preferably use end sleeves instead of soldering cable ends. Before connecting, correctly clamp
the end sleeve onto the cable to establish a connection capable of conducting current.
WARNING
Securely and reliably clamping and enclosing the end of the conductor
If the end of the conductor is not correctly enclosed by the end sleeve, but is clamped together
with it, then this can lead to overheating. The temperature class of the machine can be
exceeded. This can trigger ignition of an explosive mixture. This can result in death, serious
injury or material damage.
● Insert only one conductor end into each end sleeve. Attach the end sleeve correctly.
Electrical connection
6.2 Connecting
SIMOTICS XP 1MD4/1MD5
Operating Instructions 05/2015
55
Summary of Contents for SIMOTICS XP 1MD4
Page 2: ...13 07 2015 11 26 V8 00 ...
Page 10: ...Table of contents SIMOTICS XP 1MD4 1MD5 10 Operating Instructions 05 2015 ...
Page 12: ...Introduction SIMOTICS XP 1MD4 1MD5 12 Operating Instructions 05 2015 ...
Page 20: ...Safety notes 2 11 Ventilation SIMOTICS XP 1MD4 1MD5 20 Operating Instructions 05 2015 ...
Page 26: ...Description SIMOTICS XP 1MD4 1MD5 26 Operating Instructions 05 2015 ...
Page 50: ...Assembling 5 3 Installing the machine SIMOTICS XP 1MD4 1MD5 50 Operating Instructions 05 2015 ...
Page 74: ...Operation 8 7 Faults SIMOTICS XP 1MD4 1MD5 74 Operating Instructions 05 2015 ...
Page 90: ...Maintenance 9 2 Repair SIMOTICS XP 1MD4 1MD5 90 Operating Instructions 05 2015 ...
Page 110: ...Disposal 11 4 Disposal of components SIMOTICS XP 1MD4 1MD5 110 Operating Instructions 05 2015 ...
Page 126: ...Index SIMOTICS XP 1MD4 1MD5 126 Operating Instructions 05 2015 ...
Page 127: ...AE EC Declaration of Conformity U161 AD EC Declaration of Conformity U163 AA R No 20000h U165 ...