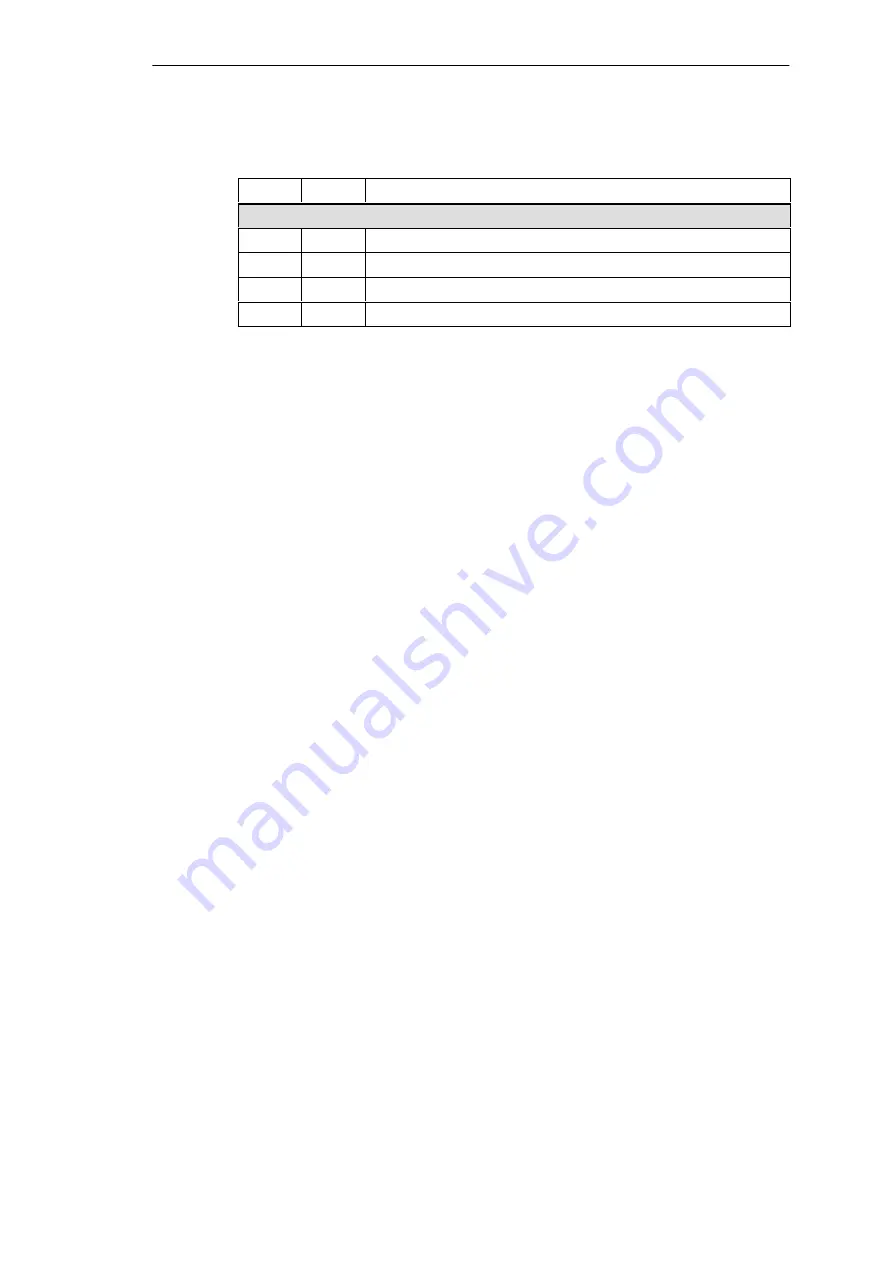
Diagnostics
7-9
IM 178-4
C79000-G7076-C178-01
Table 7-9 Structure of the Channel-Specific Section of the Diagnostic Data (1 means
error)
Byte Content/Meaning
Bit
reserved
25
0..7
00
H
(reserved)
26
0..7
00
H
(reserved)
27
0..7
00
H
(reserved)
28
0..7
00
H
(reserved)
* For example incorrect sensor type or reserved values not 0 or normalization value too high.