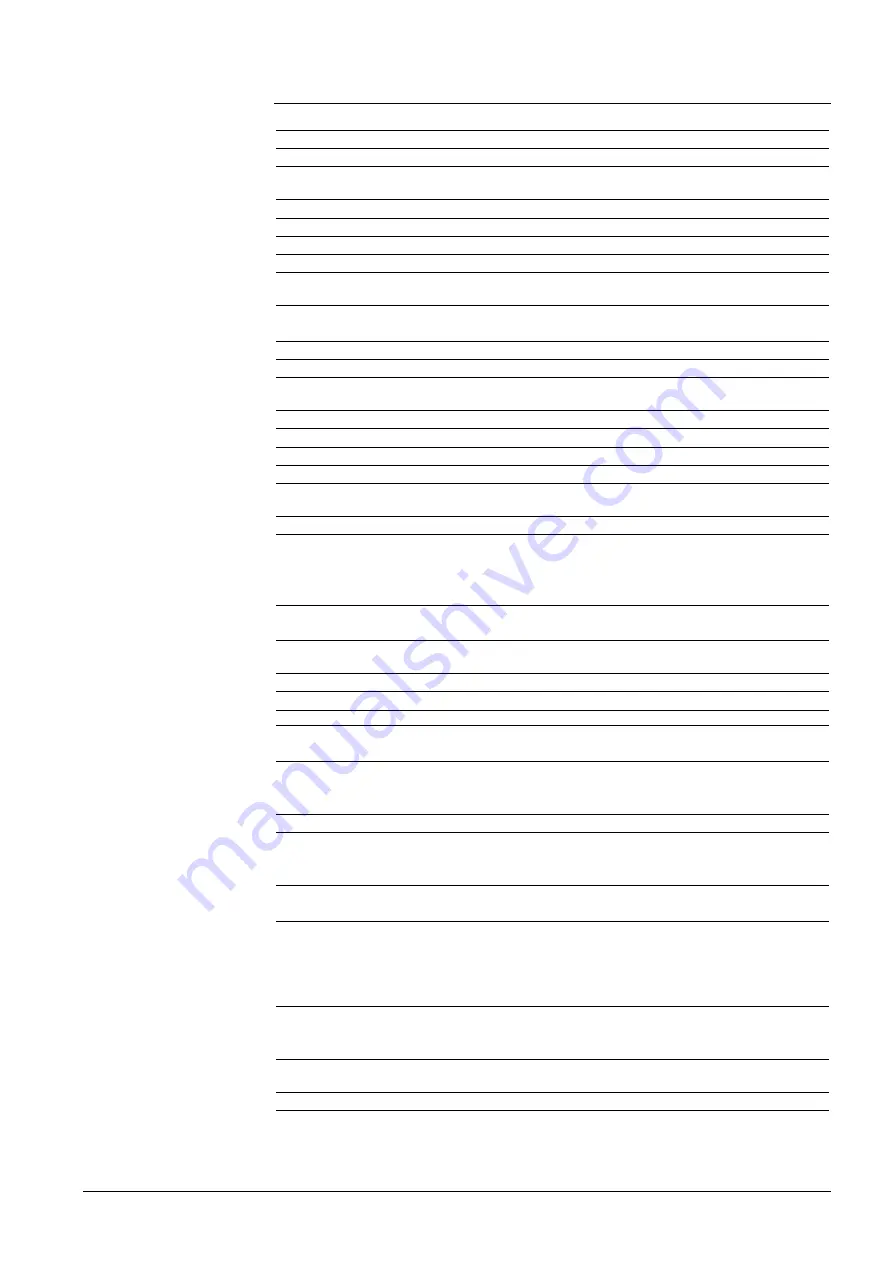
113/126
Siemens Building Technologies
Basic documentation RVD240
CE1P2384en
HVAC Products
34 Technical data
27.05.2004
34 Technical
data
Power supply
Rated voltage
AC 230 V ±10 %
Rated frequency
50 Hz
Max. power consumption
8.5 VA, 6.5 W, cos
ϕ
>0.7
Functional data
Reserve of clock
12 h
Software class
A
Classifications to
EN 60730
Mode of operation
type 1b (automatic controls)
Degree of contamination
normal contamination
Inputs
Sensor inputs (B…)
Sensing element
refer to subsection 1.3 “Equipment
combinations”
Max. number of sensors per input
1
Measuring range
0…150 °C
Digital input (H5)
Low-voltage up to
U <10 V
Switching current
I
≥
2 mA (for reliable operation)
Voltage with contact open
DC 12 V
Voltage with contact closed
DC 2…5 mA
Contact resistance
R
≤
80
Ω
Outputs
Switching outputs
Rated switching voltage
AC 24…230 V
Rated current
Outputs Y1, Y2, Q1, Q2, Q3, Y7/Q4, Y8/K6 AC 0.02…1(1) A
Outputs Y5, Y6
AC 0.02…2(2) A
Switch-on current
max. 10 A max. 1 s
Max. rating as mixing valve relay Y1, Y2, Y5,
Y6, Y7, Y8
15 VA
PMW output
Idle voltage
12 V
Max. internal resistance
1,340
Ω
Frequency 2,400
Hz
Interfaces
PPS
Connection (to the room unit)
2-wire connection, interchangeable
LPB
Connection
2-wire connection, not interchange-
able
Bus loading number E
3
Detailed information for Standard Controls:
Basic System Data
Data Sheet N2030
Local Process Bus
Data Sheet N2032
Detailed information for OEMs:
Local Process Bus
Basic Documentation P2370
Perm. cable lengths
To the sensors
Copper cable 0.6 mm dia.
20 m
Copper cable 1.0 mm
2
80
m
Copper cable 1.5 mm
2
120
m
To the room unit
Copper cable 0.6 mm dia.
37 m
Copper
cable
≥
0.8 mm dia.
75 m
Degrees of protection
Degree of protection of housing to IEC 60529
IP 40D
Safety class to EN 60730
II