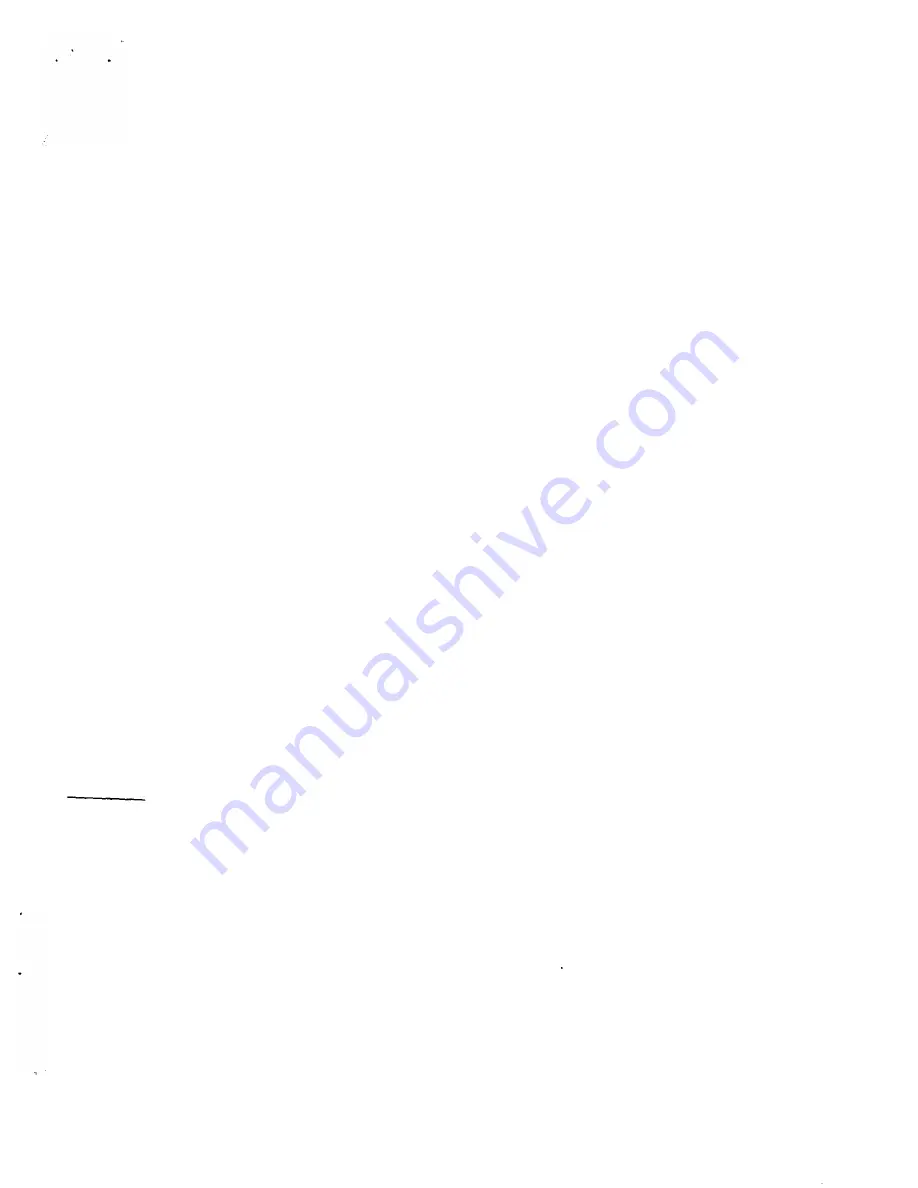
when the plunger is positioned 1-11/16 to 1-13/16 inch (42.9-46mm) above the floor line, and causes trip
ping of breaker contacts when it is raised to a level not more than 2-1/16 inch (52.4mm) above the floor
line. The latch tripping rod associated with the foot lever should be clear of the trip latch by up to 1/32
inch (0.8mm) maximum in the relaxed position (18, Fig. 6).
The foot lever can be padlocked by matching holes in the breaker frame with those in the lever arm. In the
padlocked position, the foot lever will be halfway down; the breaker will be trip-free; the interlock plunger
will be between 2 and 2-1/4 inches (50.8-57.2mm) from the floor line and will hold the breaker in any
of the three positions within the cubicle.
T RIP LATCH ADJUSTMENTS
Trip Latch Clearance- To change the clearance between the trip latch and trip latch rollers. The "stop
bar" ( 143, Fig. 48) height adjustment wil l accomplish this purpose. Loosen "lower link stop", (36, Fig. 11)
and rotate to permit maximum "lower trip link" movement. Adjust "stop bar" height as follows:
T RIP LATCH CLEA RANCE (Fig. 11)
1.
First determine that .030 to .060 (0.76 to 1.52mm) clearance exists between plate (22, Fig.
3)
and stop washers (54, Fig. 3) on bottom of vacuum interrupters with breaker open. (Note that
this clearance is measured on different screws than distance "A".) If this clearance is less than
specified, and the gap between the latch and latch rollers is less than .030 to .060 (0.76 to 1.52
mm) proceed as follows:
1.1 Loosen jam nut (146, Fig. 46).
1.2 Rotate stop bar ( 143, Fig. 46) to rotate radius arm and four bar linkage until the .060
(1. 52mm) gap is obtained over the stop washers (54, Fig. 3). This adjustment should also
bring the latch and latch rollers with in the specified tolerance. Retighten jam nut ( 146,
Fig. 46).
1.3 If after step 1.2 the setting of the lower link stop (36, Fig. 11) prevents the latch roller
link from rotating sufficiently to achieve the required .030 to .060 (0.76 to 1. 52mm)
gap, readjust the lower link stop to the proper position.
2.
If the gap over the stop washers (54, Fig. 3) in step
1
above is within tolerance, and the latch to
latch roller gap is over .060 (1.52mm), it may be adjusted to tolerance by rotating the lower link
stop (36, Fig. 11).
CAUTION
THE OPENING STOP NUTS UND E R STOP WASHERS (54, FIG. 3} SHOUL D NO RMALLY NOT BE AD
JUSTE D IN THE FIELD UNLESS A N EW VACUUM INTE R RUPT E R ASSEMBLY IS B E ING INSTALL
E D ON THE C I RCUIT B R EAK E R.
Trip Latch Bite -Trip latch bite is established by setting the latch tail top surface 5/16" (7.9mm} below
surface of self-clinching nut as shown in Fig. 20. Lock securely with jam nut. One turn of adjusting screw
will alter the gap 0.062 inches ( 1.57mm). This setting will produce a latch bite of 0.259 to 0.111 inches
(6.58 - 2.82mm} as shown.
T RIP
LATCH CHECK
SENSO R ADJUSTMENTS (Fig. 20A and 20B)
The magnetically operated hall effect switch (sensor) and actuating magnet are to be pre-assembled
to the operator. The unit is to be adjusted by advancing the threaded bushing through the tapped hole
'
until a gap of .040 - .000 + .015 ( 1.02- .00/+.38mm) is achieved between the surface of the switch and the
top of the shrink tubing holding the magnet actuator assembly to the trip latch. With this gap achieved, the
sensor may be locked in place.
-10-
www
. ElectricalPartManuals
. com