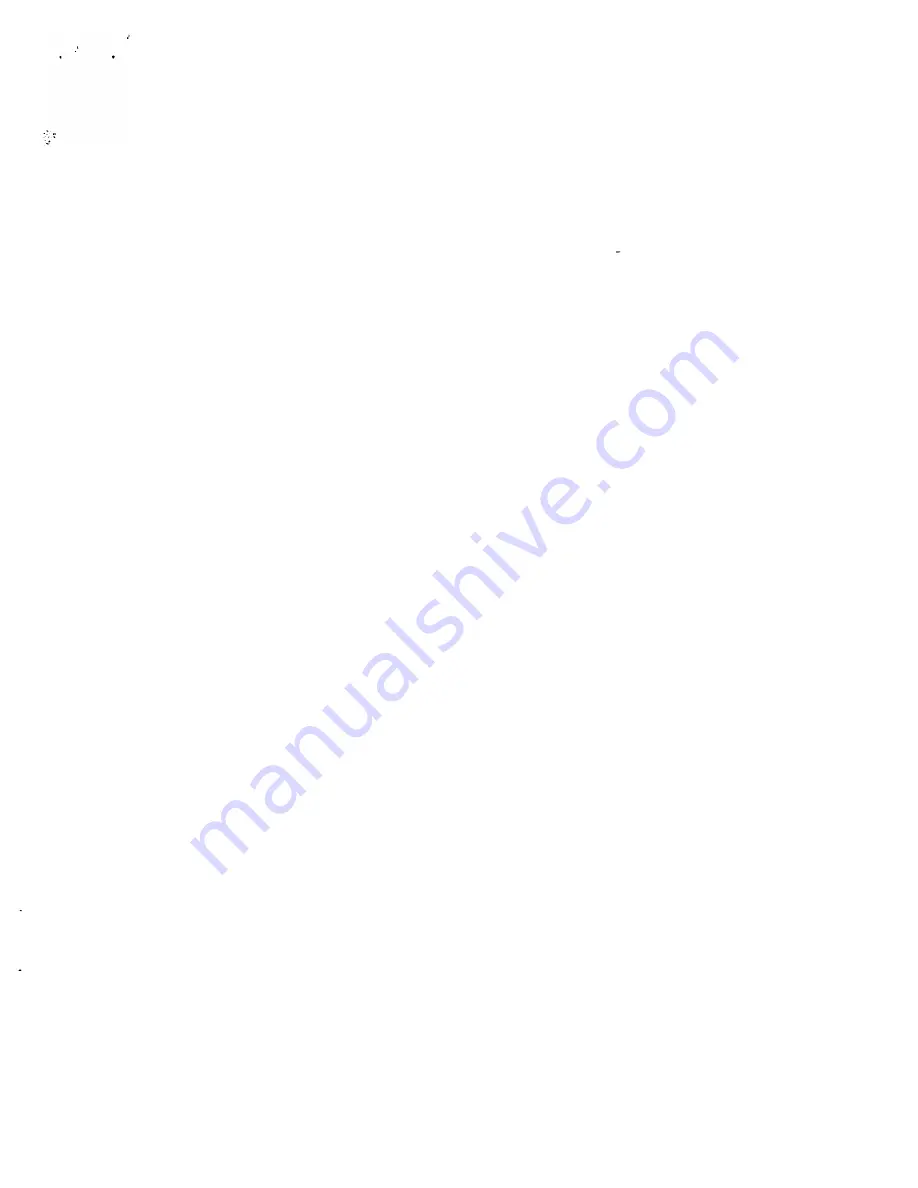
s
p
r
i
n
g
( 1 1 ,
Fig.
8),
will
immediately reset the four
bar
linkage
(12).
If the closing springs
(6)
are not
charged, the linkage reset spring
(11)
will
not reset the four bar linkage
(12)
until just before
the
closing springs (6)
are
completely charged.
ELECTRICAL CONTROL
Schematic
The normal control for this operator is contained in a control panel mounted at the rear of the
unit. It consists of the motor cutoff switch
(10,
Fig.
6),
anti -pumping relay
(30,
Fig.
6),
and
the close latch check switch
(16,
Fig.
6).
The control arrangement schematic diagram is shown
in Fig.
9.
Spring Charging
The spring charging motor power is supplied through terminals
3
and
4,
Fig.
9.
The mechanical
interlock is a switch operated by the breaker release lever (foot lever) which opens the motor
circuit when the lever is depressed. The close latch check switch is closed when the close
latch
(9, Fig. 6)
is in the reset position. The
88
switches are shown with the closing springs
discharged. When the control is energized, the motor starts to charge the springs. The
88
switch is operated by a roll pin striker
(37,
Fig.
6)
mounted in the ratchet wheel
(4,
Fig.
6}.
As the ratchet wheel and drive blocks charge the springs, the ratchet wheel revolves to the
position of full compression, dead center.
B
eyo
n
d dead center position, the springs aid rotation
and cause the motor cutoff switch striker to depress the actuator
(35,
Fig.
6)
of the
88-1
switch,
opening the motor circuit and the
88-3
contact in the anti -pumping relay circuit. The spring
charging motor coasts to a stop with the driving pawl
(2,
Fig.
6)
oscillating freely on the
smooth portion of the ratchet wheel .
Closing
The standard control schematic for a stored energy operator is shown in Fig.
9.
When the close
control switch is closed, the circuit from terminal
7
through
88-2
and
52Yl
to
52B
to terminal
6
energizes the closing coi
I, closing the breaker.
As soon as the closing springs are discharged, the
88-3
switch contact closes to energize the
52Y
relay. If the close control switch remains closed, the
52Y
relay remains picked up through
contact
52Y2.
Control switch has to be released to reset control for another closing operation.
This forms the anti -pumping relay circuit which prevents the circuit breaker from reclosing
immediately after a trip free operation. If control power is momentarily lost during closing,
upon re-energization, the
52Y
relay picks up instantaneously through contact
88-3
maintaining
the anti -pumping relay circuit prior to complete spring charging.
Close Latch - Mechanical and Electrical Interlocks
The close latch
(9,
Fig.
7)
must be fully reset to receive the cam mounted spring release rollers
at the end of the charging cycle. To insure the close latch is in this fully reset position, an
electrical and mechanical interlock is provided.
-8-
www
. ElectricalPartManuals
. com