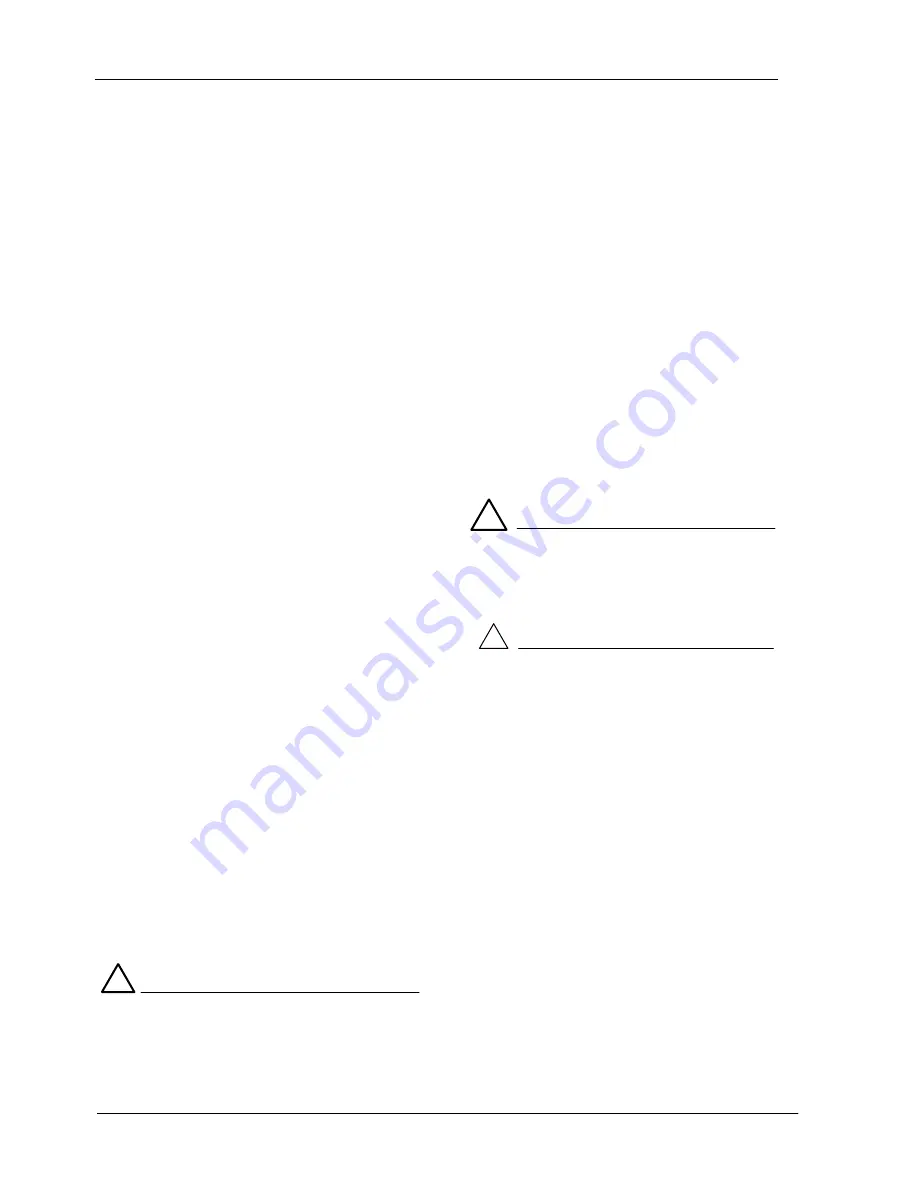
Maintenance and fault tracing
7SV512
V1
106
C53000---G1176---C91
7
Maintenance and fault tracing
Siemens digital protection relays are designed to re-
quire no special maintenance. All measurement and
signal processing circuits are fully solid state and
therefore completely maintenance free. Input mod-
ules are even static, relays are hermetically sealed or
provided with protective covers.
If the device is equipped with a back-up battery for
saving of stored annunciations and the internal time
clock, the clock module should be replaced after at
least 10 years of operation. (refer to Section 7.2).
This recommendation is valid independent on
whether the battery has been discharged by occa-
sional supply voltage failures or not.
As the protection is almost completely self-moni-
tored, from the measuring inputs to the command
output relays, hardware and software faults are au-
tomatically annunciated. This ensures the high avail-
ability of the relay and allows a more corrective rath-
er than preventive maintenance strategy. Tests at
short intervals become, therefore, superfluous.
With detected hardware faults the relay blocks itself;
drop-off of the availability relay signals ”equipment
fault”. If there is a fault detected in the external mea-
suring circuits, generally an alarm is given only.
Recognized software faults cause the processor to
reset and restart. If such a fault is not eliminated by
restarting, further restarts are initiated. If the fault is
still present after three restart attempts the protec-
tive system will switch itself out of service and indi-
cate this condition by the red LED ”Blocked” on the
front plate. Drop-off of the availability relay signals
”equipment fault”.
The reaction to defects and indications given by the
relay can be individually and in chronological se-
quence read off as operational annunciations under
the address 5100, for defect diagnosis (refer to Sec-
tion 6.4.2).
If the relay is connected to a local substation auto-
mation system (LSA), defect indications will also be
transferred via the serial interface to the central con-
trol system.
Ensure that the connection modules are not
damaged when removing or inserting the
device modules! Hazardous voltages may
occur when the heavy current plugs are
damaged!
! Warning
7.1
Routine checks
Routine checks of characteristics or pick-up values
are not necessary as they form part of the continu-
ously supervised firmware programs. The planned
maintenance intervals for checking and mainte-
nance of the plant can be used to perform operation-
al testing of the protection equipment. This mainte-
nance serves mainly for checking the interfaces of
the unit, i.e. the coupling with the plant. The follow-
ing procedure is recommended:
--- Read-out of operational values (address block
57) and comparison with the actual values for
checking the analog interfaces.
--- Simulation of an internal short-circuit with 4 x I
N
for
checking the analog input at high currents.
Hazardous voltages can be present on
all circuits and components connected
with the supply voltage or with the meas-
uring and test quantities!
!
Warning
Test currents larger than 4 times I
N
may
overload and damage the relay if applied
continuously (refer to Section 3.1.1 for
overload capability). Observe a cooling
down period!
!
Caution!
www
. ElectricalPartManuals
. com