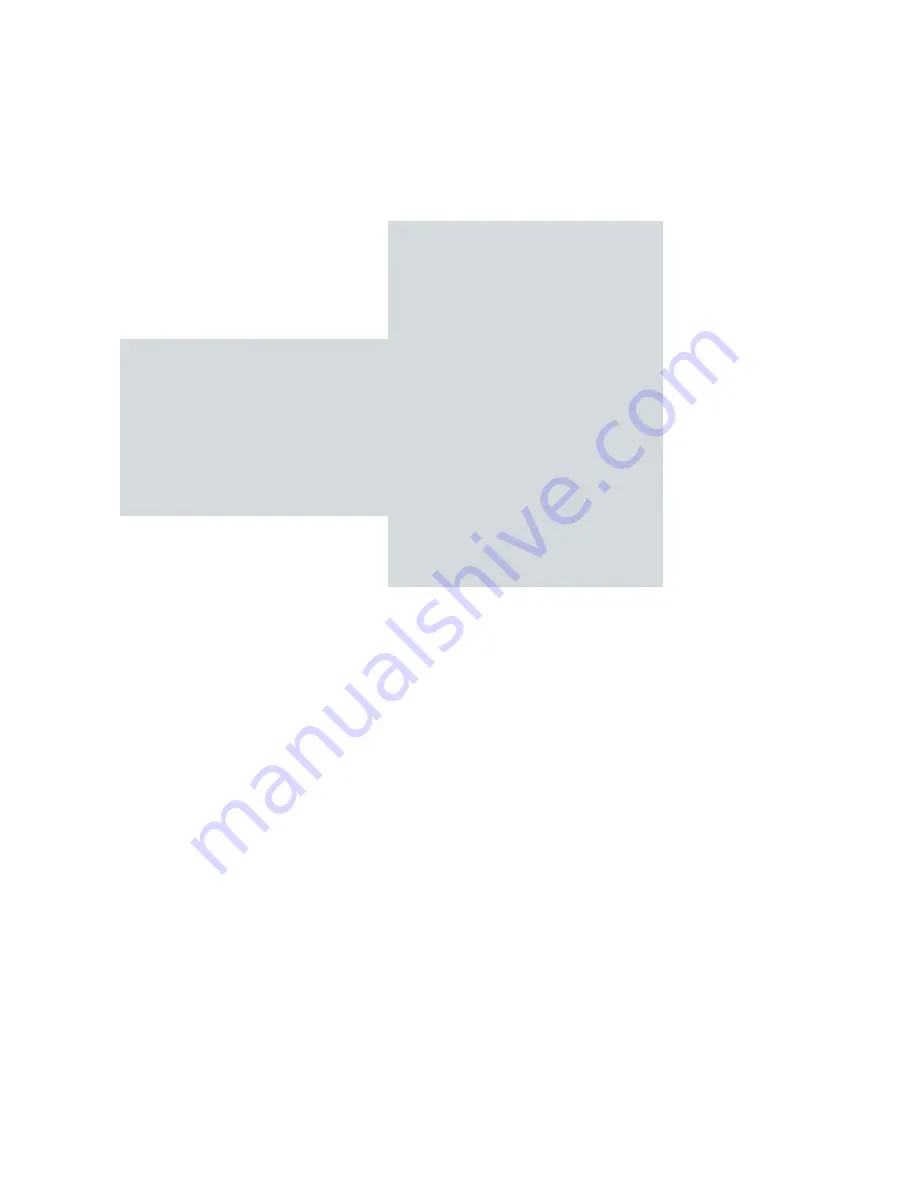
4. Notify Siemens medium-voltage
customer service immediately of any
damage, at +1 (800) 347-6659 or
+1 (919) 365-2200 outside the U.S.
5. Arrange for a carrier inspection of the
damage immediately.
Important:
Do not move the equipment
from the place it was set when unloading.
Also, do not remove or disturb packaging
or wrapping material prior to carrier
damage inspection. Equipment must be
inspected by carrier prior to handling after
receipt. This eliminates loss due to claims
by carrier that the equipment was
damaged or further damaged on site after
unloading.
6. Be sure the equipment is properly
protected from any further damage by
covering it properly after unloading.
7. If practical, make further inspection for
possible concealed damage while the
carrier’s inspector is on site. If
inspection for concealed damage is not
practical at the time the carrier’s
inspector is present, it must be done
within 15 days of receipt of the
equipment. If concealed damage is
found, the carrier must again be
notified and inspection made prior to
taking any corrective action to repair.
Also notify Siemens immediately at +1
(800) 347- 6659 or +1 (919) 365-2200
outside the U.S.
8. Obtain the original carrier inspection
report and forward it with a copy of the
noted delivery receipt to Siemens.
Approval must be obtained by Siemens
from the carrier before any repair work
can be performed.
Before approval can be obtained,
Siemens must have the documents
referenced in the paragraph above. The
carrier inspection report and/or driver’s
signature on the delivery receipt does
not constitute approval to repair.
Receiving, handling and
storage
Note:
Any determination as to whether the
equipment was properly loaded or properly
prepared by shipper for over-the-road
travel cannot be made at the destination.
Shipments are not released from the
factory without a clear bill of lading.
Approved methods are employed for
preparation, loading, blocking and tarping
of the equipment before it leaves the
Siemens factory. If the equipment is
received in a damaged condition, this
damage to the equipment has to have
occurred while en route due to conditions
beyond Siemens‘ control. If the procedure
outlined above is not followed by the
consignee, purchaser or their agent,
Siemens cannot be held liable for repairs.
Siemens will not be held liable for repairs
in any case where repair work was
performed prior to authorization from
Siemens.
Handling procedure
1. Carefully remove the shipping carton
from the circuit breaker. Keep the
shipping pallet for later use if the
circuit breaker is to be stored prior to
its installation.
2. Inspect for concealed damage.
Notification to carrier must take place
within 15 days to assure prompt claim
resolution.
3. Each circuit breaker should be lifted
appropriately to avoid crushing the side
panels of the circuit breaker, or
damaging the primary disconnect
assemblies.
Type 38-3AH3 vacuum circuit breakers
weigh between 800 and 1,000 lbs
(364-455 kg), plus an additional 125
pounds (57 kg) for the pallet and
packaging.
4. The palleted circuit breaker can be
moved using a properly rated fork-lift
vehicle. The pallets are designed for
movement by a standard fork-lift
vehicle.
7