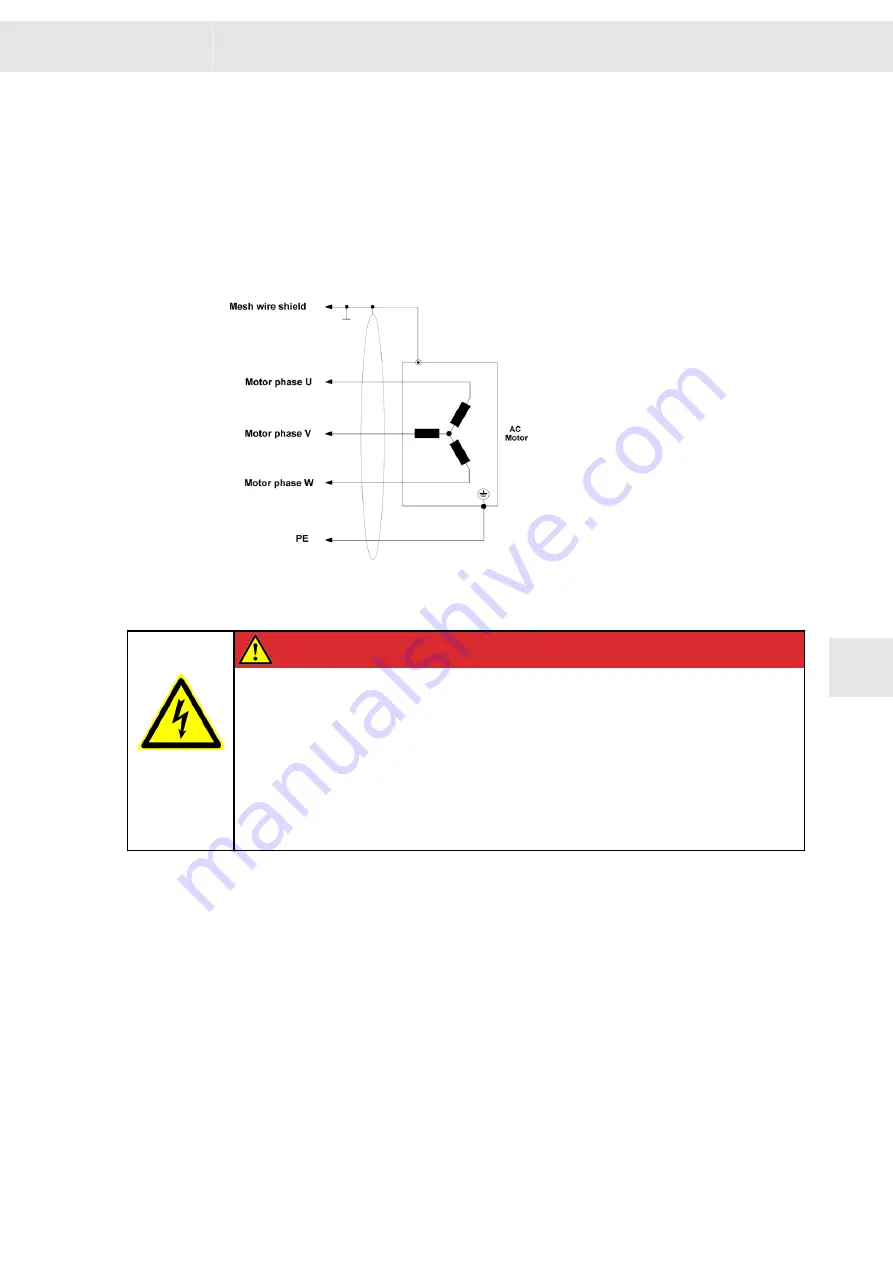
9
Connection Examples
The following sections provide connection examples for the individual connectors of
the device.
9.1
X2/X13 – Motor Phases
Ground the motor housing in the machine!
DANGER
Dangerous shock currents
Earthing and shielding measures are required to protect devices and persons. To
ensure the safety of the operator earthing must be carried out with low impedance.
With respect to the ground connection one of the following actions must be done:
▶
connect the motor housing to the ground of the machine or
▶
connect the ground terminal of the motor connector to the central ground point
of the machine.
Consider the following with regard to shielding: Always use shielded motor cables!
W
Connection Examples
Drive Amplifier SD2B / SD2B plus - Hardware Description
47
9
Summary of Contents for SD2B
Page 1: ...Drive Amplifier SD2B SD2B plus Hardware Description P TD 0000312 8 2019 09 09 SIEB MEYER W ...
Page 4: ...Chapter Overview W 4 Drive Amplifier SD2B SD2B plus Hardware Description ...
Page 8: ...Content W 8 Drive Amplifier SD2B SD2B plus Hardware Description ...
Page 12: ...General Information W 12 Drive Amplifier SD2B SD2B plus Hardware Description 2 ...
Page 22: ...Unit Assembly Complying EMC W 22 Drive Amplifier SD2B SD2B plus Hardware Description 4 ...
Page 26: ...Drive Amplifier SD2B SD2B plus W 26 Drive Amplifier SD2B SD2B plus Hardware Description 5 ...
Page 32: ...Device variant SD2B W 32 Drive Amplifier SD2B SD2B plus Hardware Description 6 ...
Page 38: ...Device variant SD2B plus W 38 Drive Amplifier SD2B SD2B plus Hardware Description 7 ...
Page 66: ...Status Display and Error Messages W 66 Drive Amplifier SD2B SD2B plus Hardware Description 10 ...
Page 80: ...Safety Circuit Restart Lock STO W 80 Drive Amplifier SD2B SD2B plus Hardware Description 13 ...
Page 82: ...Appendix W 82 Drive Amplifier SD2B SD2B plus Hardware Description 14 A ...