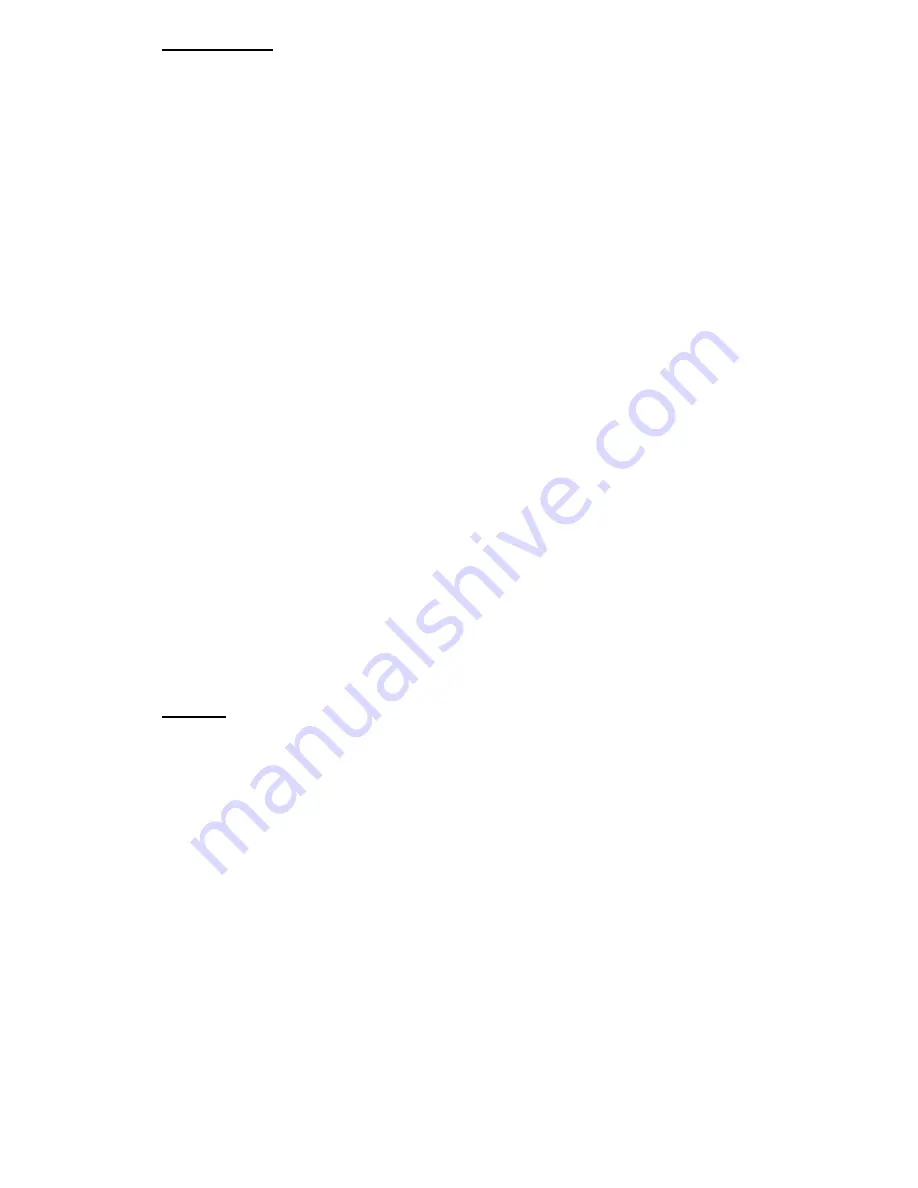
5
PROCESSING
In a dark box, load the film on the reel (see REEL LOADING). Slide the reel on the spindle.
If there is room on the spindle, use the SPACER (goes on last) to conserve chemistry.
Place the spindle inside the PROCESS DRUM. Cover the spindle with the lid (one side is
shaped to go over the spindle). Clip the tank together. You are now light tight.
Push the PROCESS TANK to the left in the TROUGH till the SNOUT seats itself inside the
COUPLING. The two stainless pins of the spindle should go on opposite sides of the
STAPLE on the rotate motor.
Look to make sure you have enough solution in the chemical bottles. Empty the DUMP
bottle. Turn the unit ON. Use PLUS to select the type of film you are processing. Push
START to begin the process.
The unit will ask you how many rolls (35 mm) are being processed. Use “PLUS to select :
“2” for 1 or 2 rolls of 35mm or 1 roll of 120/220. Use SPACER.
“4” for 3 or 4 rolls of 35mm, 2 rolls of 120/220 or a 4x5 sheet film holder.
“6” for 5 or 6 rolls of 35mm, 3 rolls of 120/220 or 2 4x5 holders (8 sheets). Use SPACER
“8” for 7 or 8 rolls of 35mm, 4 or 5 rolls of 120/220.
The unit uses about 3 ½ oz (105 ml) of each solution per 35mm roll.
If you want to change the developing times see PUSH PROCESSING.
The unit will load the first solution into the internal heating tank, heat it to the proper
temperature, warm the processing drum with warm air and then start the process
automatically. As the unit is processing one solution it prepares the next solution. The film
DRUM has an independent temperature sensor that controls the warm air blowing on the
DRUM. This fine tunes the solution to an accurate temperature for very consistent
results.When one solution is finished it is drained out and the prepared solution in the heating
tank is pumped into the DRUM. The same procedure is repeated for all the necessary
solutions. The unit will signal at the end of the wet processing. Remove the PROCESS DRUM.
Insert the PLUG in the COUPLING and wipe out the TROUGH with a paper towel.
DRYING
Up to 4 rolls of 35 mm film can be dried in the included TURBO DRYER on reels. The film
can also be dried any other way. The base of 120 film is too thin for drying on a reel, and
must be dried by other means. Disc drying requires an accessory dryer (Part AF-DD).
Place the TURBO DRYER vertically in the TROUGH so that the cut away portion of the
TURBO DRYER covers the air vent in the side of the TROUGH. Shake out each reel 4
times over a sink with a vigorous snap of the wrist to remove excess solution. Replace
the reels on the spindle and put the spindle in the TURBO DRYER
Push START to begin drying. The unit will FLUSH itself as it is drying. The unit MUST BE
ALLOWED TO FLUSH itself after every processing run. The required drying time will vary
with the amount of film and the relative humidity of the room. If the film is not fully dry
when the dryer stops (15 min.), dry again. Rinse all reels, spindle and drum with COLD
water. Room air dry - hot air may distort the parts. RINSE, DO NOT IMMERSE THE DRUM.
If you get drying marks, try the following: a) use distilled water for the last step. b) dilute
the wetting agent or stabilizer. c) use softened water. d) external rinse in distilled water.
e) squeegee and hang up to dry.
Film with drying marks can be re-rinsed and dried
again.
Summary of Contents for SK-8RG
Page 13: ...13...
Page 16: ...16...
Page 19: ...19 blank sheet for page count insert wiring diagram...