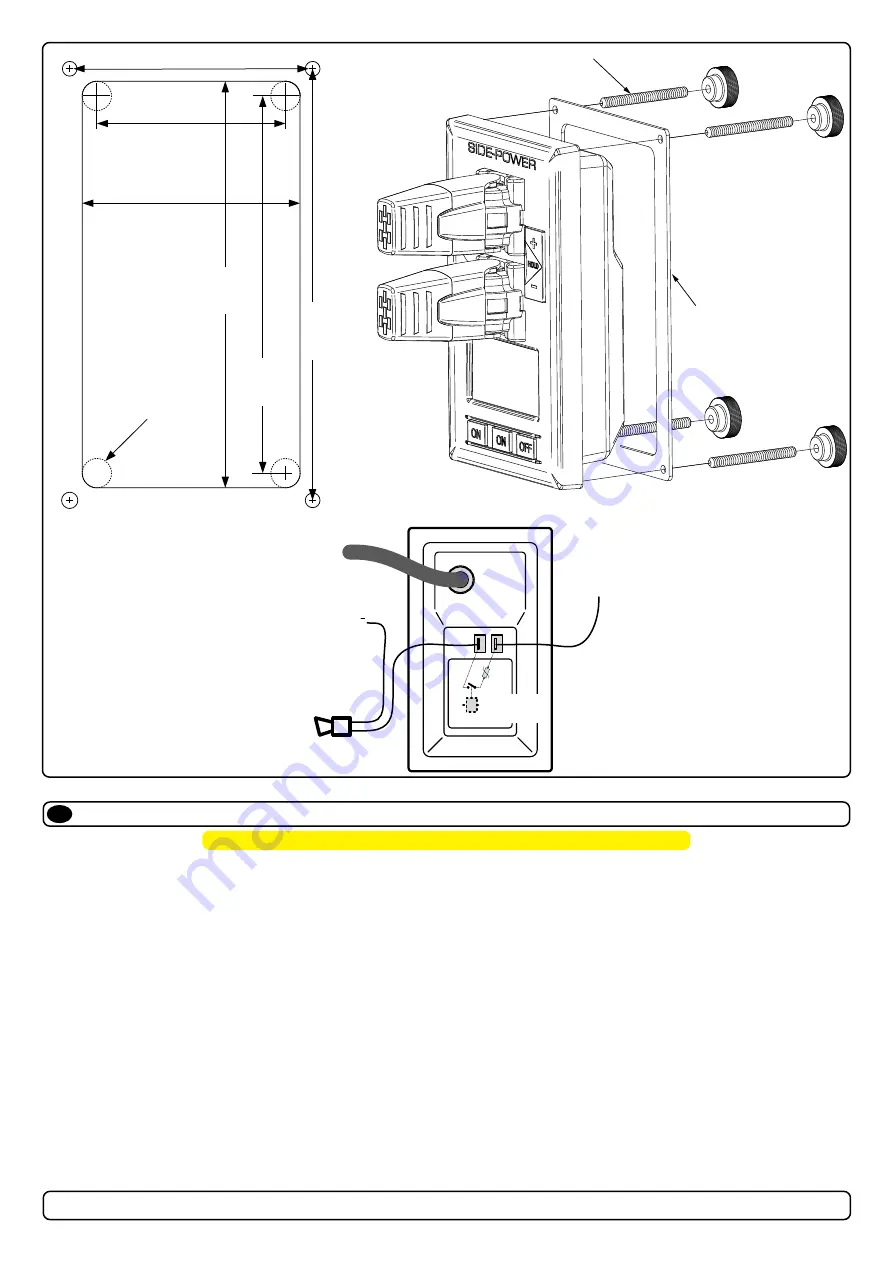
22
6146
2
2019
-
SH 360
Control Panel Installation
EN
Find a suitable location for the control panel where it does not obstruct or is obstructed by other devices. Install the control panel on a fl at surface where
it is easy to use.
1. Use the supplied cut-out template to mark the area to remove on your control dash.
2. Cut out the area per template for the control panel. (
NB: If the front surface around your cut out is jagged or chipped, use a sealant
to assist the gasket.)
3. Place the gasket to the back face of the panel
4. Plug cables into the connectors at the rear of the control panel.
5. Insert the control panel in place and fasten screws.
6. Insert the control panels covering caps.
MC_0042
!
Please refer to the graphic for special considerations relating to your model
!
MG_0063
GASKET
4x SCREWS
58 mm
67 mm
125 mm
116 mm
132.7 mm
75.7 mm
Ø 4.5 mm
Ø 4.5 mm
Ø 4.5 mm
Ø 4.5 mm
(S-link)
External alarm buzzer
12V / 24V DC - max 0,5A
External alarm / buzzer connection
Supply
+ 12V / 24V DC
-
+
Ø 4.5 mm
Rear
side
of pa
nel
Internal
fuse / relay