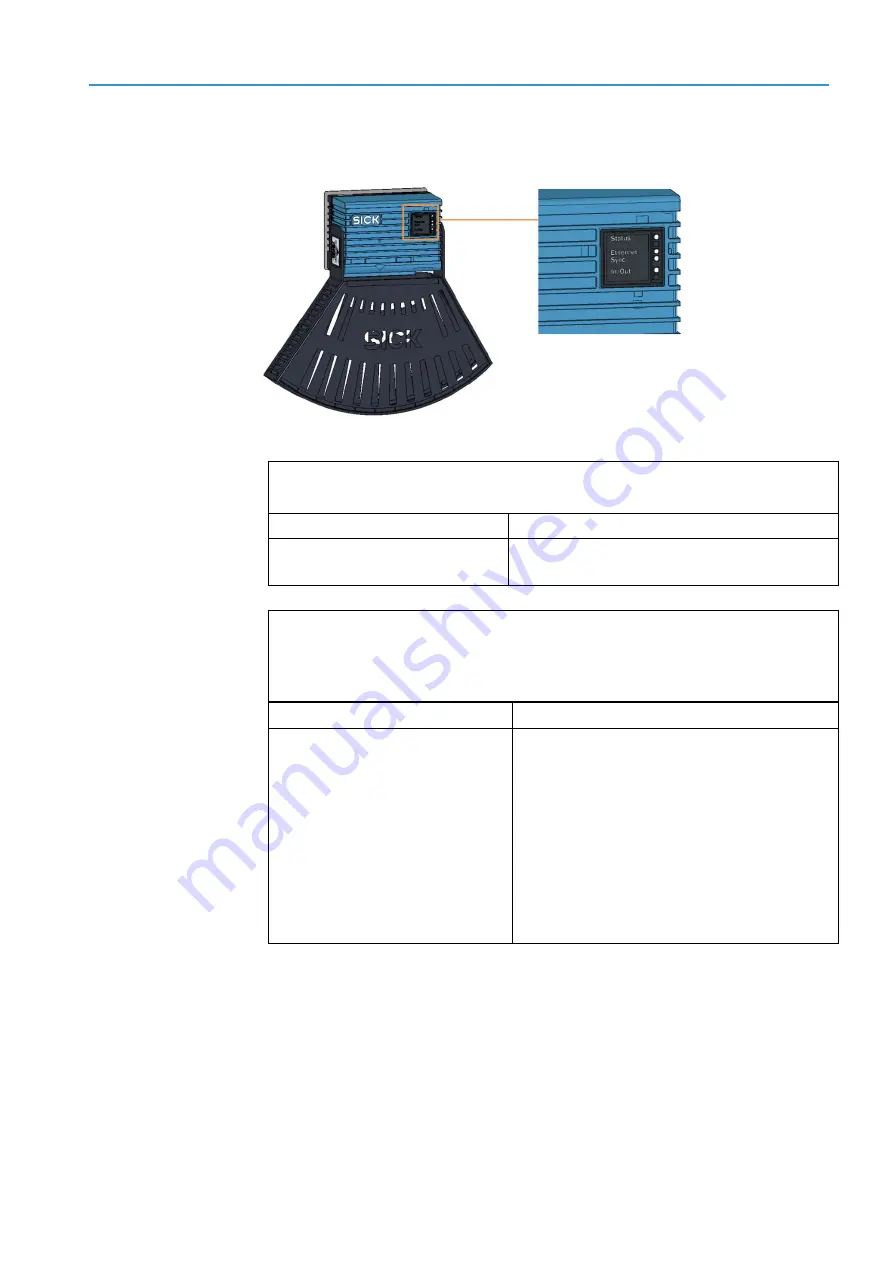
FAULT DIAGNOSIS
8
47
8025816/V1-0/2020-07-06|SICK
Subject to change without notice
OP ERA T ING INS T RU C T IO NS | VMS4400 Contour Verification
8.2
Fault indications of the components
8.2.1
Fault indication on the LMS4x21
Fig. 30: Status indicators on the LMS4x21
Fault indication
The Status LED does not light up.
Fault cause
Possible solution to the problem
Fuse is defective.
▸
Check the fuse block in the cabinet and,
if necessary, replace the defective fuse.
Fault indication
The Status LED lights up red.
The 2D LiDAR sensor independently monitors beam generation and automatically shuts
it down in the event of irregularities. The sensor no longer sends any measured values.
Fault cause
Remedy
Error during initialization or
self-test.
LMS4x21 is not in measuring
mode or is in measuring mode,
but errors have occurred.
▸
Check the voltage supply.
▸
Interrupt the voltage supply to the LMS4x21.
▸
Restore the voltage supply.
If the fault persists or occurs again after
the voltage supply has been restored:
▸
Check the device status using SOPAS
(see below).
▸
If errors are listed there, contact SICK Service.
Tab. 4: Fault indication on the 2D LiDAR sensor