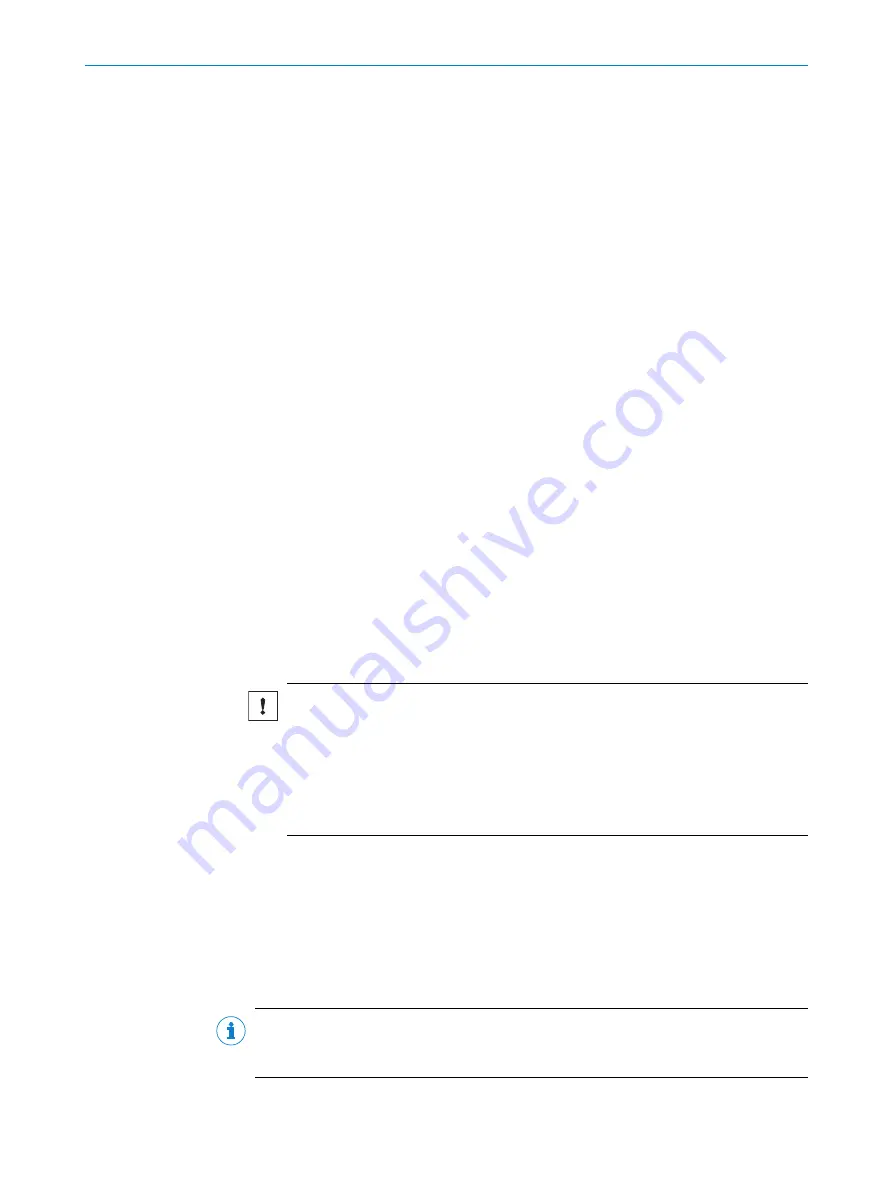
5
Mounting
5.1
Mounting instructions
•
Observe the technical data.
•
Protect the sensor from direct and indirect sunlight.
•
To prevent condensation, avoid exposing the device to rapid changes in tempera‐
ture.
•
The mounting site has to be designed for the weight of the device.
•
The device can be mounted in any position.
•
It should be mounted so that it is exposed to as little shock and vibration as possi‐
ble. Optional mounting accessories are available,
•
During mounting, make sure there is no reflective surface behind the reference
target,
•
To avoid inaccurate measurements when installing multiple devices: Make sure
that the laser spot of one device is not in the visible range of another device,
"Mutual interference", page 21
•
Avoid having shiny or reflective surfaces in the scanning range, e.g., stainless
steel, aluminum, glass, reflectors, or surfaces with these types of coatings.
•
Protect the device from moisture, contamination, and damage.
•
Make sure that the status indicator is clearly visible.
•
Do not subject the device to excessive shock or vibrations. In systems subjected to
heavy vibrations, secure the fixing screws with screw-locking devices.
•
The M3 x 4 screws included with delivery are intended for mounting the mounting
clamps via the blind hole threads on the rear or underside of the device. If the
mounting clamps are not used or if other screws are used, the screws must not be
screwed into the thread by more than 2.8 mm.
5.2
Mounting device
1.
Mount the LiDAR sensor using the designated fixing holes,
.
NOTICE
Risk of damaging the device!
the device will be damaged if the tightening torque of the mounting screws is too
high or if the maximum screw-in depth of the blind hole threads is exceeded.
b
Observe maximum tightening torque.
b
Use suitable mounting screws for the blind hole threads of the device and
observe the maximum screw-in depth.
2.
Make the electrical connection. Attach and tighten a voltage-free cable,
necting the device electrically", page 28
3.
Switch on the supply voltage.
4.
Align the vertical center line of the field of view of the device with the center of the
area to be monitored. The marking on the upper side of the optics cover serves as
a bearing alignment aid.
5.3
Mutual interference
NOTE
Optical sensors and other IR light sources can influence the measurement and detec‐
tion capabilities of the device.
MOUNTING
5
8024355/15I9/2019-09-30 | SICK
O P E R A T I N G I N S T R U C T I O N S | TiM8xxP
21
Subject to change without notice